Unbolted in Fairfield (Update on the 2022 Bell 407 GXP Crash)
On the 4th of June 2022, a Bell 407 GXP helicopter crashed in a field near Fairfield, New Jersey. I wrote about it at the time. The final report and docket have now been released and so I want to take a closer look. I’ll repeat the basic details from the other post so that there’s no need to read both.
The following is a video of the crash of the Bell recorded by a surveillance camera. It shows the helicopter flying normally, aligned to the runway, and then begin a gentle climb. There appears to be a slight turn to the right and then the helicopter rotates clockwise around the main rotor mast. A few seconds later, the rotation stops and the helicopter begins to rotate counterclockwise and descends quickly towards the ground.
The operator offers helicopter tours of New York City and private charter services around the northeast United States. On the 4th of June 2022, the Bell 407 GXP registered as N98ZA departed Essex County Airport (CDW) in New Jersey for a repositioning flight to John F. Kennedy International Airport (JFK) in Queens, New York. The pilot held instructor ratings for helicopter and instrument helicopter, with 872 hours flight time, of which 29 were on type. He had received 16 hours ground instruction on the Bell 407 and five hours of flight training before completing his commercial competency/proficiency check.
The departure seemed normal and the helicopter started the flight heading southeast at 500 feet above mean sea level. Five minutes later, about two miles south of Teterboro, the pilot said “What is going on here?”
He contacted ATC and requested a return to Essex County Airport. The controller asked if the pilot needed assistance but the pilot said no.
The helicopter turned left to return to the airport, travelling at about 85 knots. The pilot told the airport tower controller that he may need the runway. The controller asked the pilot to report when two miles out and to expect runway 28.
The pilot reported two miles out. The controller cleared the helicopter to land “on the numbers” for runway 28. As the helicopter continued towards the airport, the airspeed began to decrease.
The helicopter crossed the boundary of the airport with its nose slightly pitched up. The indicated airspeed had fallen below 65 knots and was still decreasing. At a height of 250 feet, over a grass area north of (and parallel to) the runway, the helicopter’s speed decreased below 35 knots and the helicopter began to yaw to the right. As the airspeed decayed, the right yaw increased.
The helicopter was at treetop height with an indicated airspeed of zero knots when the right yaw ceased. The helicopter began to yaw to the left with a slight left roll. Then the helicopter abruptly yawed right, pitched forward, and descended rapidly as the helicopter rotated around the main motor mast. It rotated several times before crashing into the grass north of runway 28.
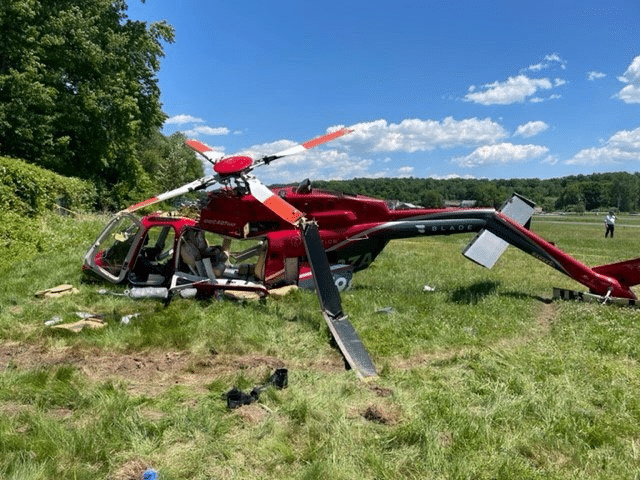
A Cirrus SR22 had just landed on Runway 4 as the helicopter was coming in. The pilot submitted an eyewitness report to the NTSB to say that he saw the helicopter descending as he began to taxi to his tie-down spot.
I expected to see it enter a hover just above the runway, but then it suddenly climbed something like 100 ft straight up.
When it stopped climbing, the helicopter maneuvered erratically drifting towards the north and descending. As it descended it spun around 2-3 times. At approximately 30-40 feet agl, the spinning stopped and the helicopter appeared to stabilize for a brief moment before continuing a nose-low, forward descent into the grass north of Runway 28. It impacted the ground at about my 9-10 o’clock position from where I was on Taxiway N. The impact was definitely hard, but I would not describe it as particularly violent, and the helicopter appeared mostly intact immediately after impacting the grass.
At about this point I asked Ground if they had witnessed the accident hoping that they were already initiating a response, which they acknowledged. The landing position of the helicopter was clearly unstable and the engine appeared to be producing power which resulted in it bouncing and twisting towards the airport fence and vegetation north of its initial landing position.
During this period I had instinctively slowed my taxi because my attention had been diverted by this startling event, but when I saw the main rotor disintegrating and throwing pieces 40 feet or more, I decided it would be best to keep moving along Taxiway N farther away from the accident site. As I taxied away, what was left of the main rotor slowed its rotation and the helicopter engine emitted a cloud of smoke. Behind me a couple of people were running across the taxiway/runway towards the helicopter, and then some minutes later the police/fire/ambulances began to show up.
This 30-second video is the interactions with Ground directly after the accident.
The pilot was seriously injured. The pilot accident report was submitted by the chief pilot of the operator, as the pilot was still incapacitated two days after the accident.
The operator confirmed that the tail rotor had been installed the day before the accident. A mechanic had found a worn feathering bearing in the tail rotor hub and blade assembly. He removed the assembly and it was sent off to have all four feathering bearings replaced. The assembly was then returned to the operator for reinstallation.
The operator’s Director of Maintenance had personally performed the reinstallation. He started by laying out all the parts on a maintenance cart. Then he followed the installation procedure, including the mast nut torque application. The mast nut torque application is a critical procedure, which ensures that the rotor assembly remains attached to the main rotor mast. As such, the process requires a second mechanic to verify the installation. He asked a mechanic to come and verify the mast nut torque.
He completed the procedure and had another mechanic verify the work. A company pilot inspected the helicopter, including ground checks at low speeds and maintenance runs. These maintenance runs are test flights, controlled flights to test the functionality of the helicopter. The tail rotor’s responses and vibrations are measured in order to adjust the weights of the rotor blades and/or the alignment of the rotor assembly. The pilot performed three consecutive maintenance runs to balance the tail rotor. Then the helicopter was released back into service. The accident flight was the first flight after the maintenance.
However, it also became clear that the Director of Maintenance was repeatedly called away during the procedure to consult on repairs for two other aircraft. He was not sure how long he’d been away before resuming the installation.
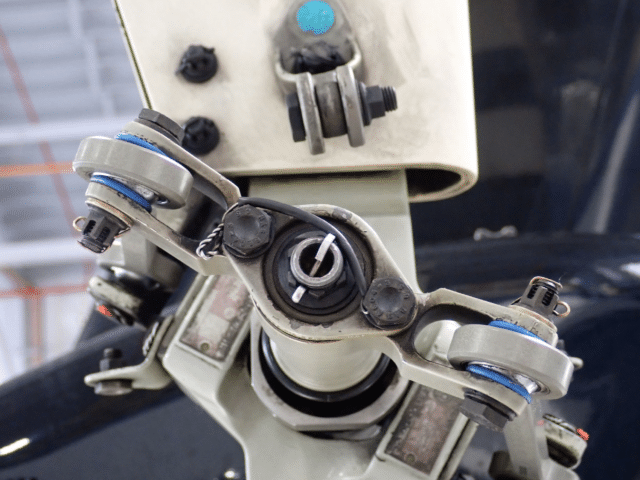
The tail rotor crosshead drive plate is positioned behind the pitch change rod attachment nut and should be bolted to the tail rotor crosshead. But directly after the accident, an FAA representative inspected the aircraft and found that the tail rotor crosshead drive plate was not bolted to the tail rotor crosshead.
There was no sign of the bolts or anything that could be the fragments of the bolts. The threads were undamaged with no sign of deformation or cross-threading.
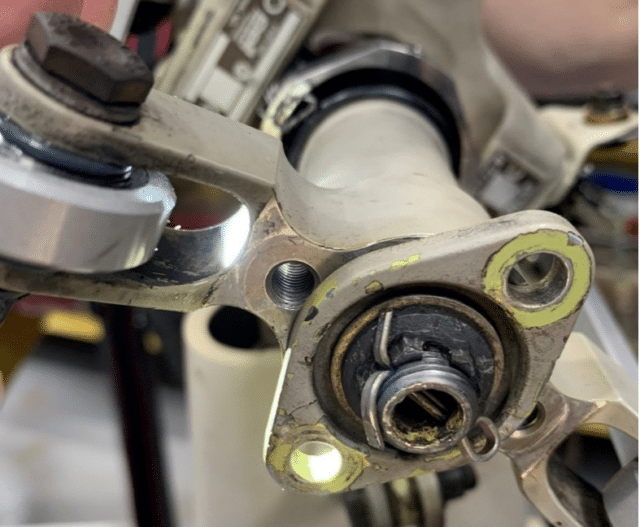
Further investigation confirmed that there were no other faults with main rotor flight control.
It was clear that the Director of Maintenance had not, in fact, bolted the tail rotor crosshead drive plate to the tail rotor crosshead.
There’s a reference to the first check in the docket which does not appear in the final report. A mechanic said that he had been approached by his supervisor and asked to verify the torque application on the tail rotor mast nut on the helicopter. He climbed the maintenance stand and applied the specified torque and then started the “safety” with 32 thousandths safety wire. He did not complete the safety although it isn’t clear why. He said that he explained the safety wire path and its final anchor point and offered to complete the safety, but his supervisor said no, he’d complete the task.
This seems likely to have coincided with the Director of Maintenance being called away to consult on on other aircraft repairs. He then completed the installation and asked another mechanic verify the final assembly. To be fair, no amount of safety wire was going to make up for missing bolts but it does underscore that the maintenance of the helicopter that day was fractured.
The operator did not have an active Required Inspection Items program, nor were they required to do so. There was no written procedure. As a result, the checks were much more informal: usually the Director of Maintenance would check the work performed by the mechanics and he would ask the mechanics to check his work. If the director wasn’t available, then “whoever was available” would check the work.
The operator had a surveillance camera inside the hangar to capture the work and the preflight inspections. However, the video was of such low resolution, it was impossible to identify the details and tools used.
During the flight, the crosshead drive plate separated, which meant the helicopter no longer had tail rotor anti-torque control.
The final report quotes the US Army Training Circular 3-04.4 Fundamentals of Flight for a great explanation of the issue here.
According to Newton’s law of action/reaction, action created by the turning rotor system causes the fuselage to react by turning in the opposite direction. The fuselage reaction to torque turning the main rotor is torque effect. Torque must be counteracted to maintain control of the aircraft; the antitorque rotor does this….
The Bell 407 Rotorcraft Flight Manual states that the key to successfully handling a tail-rotor emergency is recognising what type of malfunction that you are dealing with.
The indications for the loss of tail rotor thrust are listed as:
- uncontrollable yawing to the right (left side slip)
- nose-down tucking
- possible roll of fuselage
The severity of these symptoms is affected by airspeed, centre of gravity, power being used and density altitude.
The manual recommends the following actions in the case of a complete loss of tail rotor thrust in flight:
Reduce throttle to IDLE, immediately enter autorotation and maintain a minimum airspeed of 55 knots indicated airspeed during descent.
In other words, reduce the throttle to IDLE so that the engine is no longer driving the main rotor blades. Feather the blades to generate lift from the upward flow of air during the descent (instead of pushing the air downwards in powered flight). The aerodynamic effect allows for enough lift and control for a safe descent without engine power. Then use the collective control on what sounds to this single-engine pilot like a flare maneuver.
The point is that while the pilot was returning to the airport at cruise speed, the helicopter remained controllable. But once the helicopter dropped below 55 knots indicated airspeed, the helicopter entered an uncontrolled yaw. As the pilot increased the engine power to slow the helicopter for the final approach to land on the runway numbers, he induced a torque reaction which could not be countered, as the helicopter no longer had tail rotor antitorque control.
The final report by the NTSB offers the following probable cause
The National Transportation Safety Board determines the probable cause(s) of this accident to be:
The failure of maintenance personnel to properly secure the tail rotor crosshead drive plate and the failure of maintenance personnel, the maintenance pilot, and the accident pilot to detect the error, which led to the helicopter’s loss of tail rotor antitorque. Also causal was the pilot’s failure to maintain the helicopter’s airspeed at or above effective translational lift and perform a run-on landing, which resulted in a loss of control.
This accident led the operator to revisit their maintenance protocols. They have since developed a required inspection program which was added to their General Operating Manual. These revisions to the manual were submitted to the FAA and accepted.
It seems so easy to get into a routine on the ground and forget how essential every action you take is to the safety of those in the air.
I’m surprised there weren’t some uninstalled bolts left on the maintenance cart. Where did they go, or are they typically discarded and new ones used?
There are places where a supervisor can also do line work; e.g., most of my managers when I was a software test or development engineer also did testing or coding rather than spending their time overseeing — but I don’t know what my occasional interruptions for advice/direction cost their work. (Note also that software work tends to start with an outline, then work down in increasingly detailed levels, giving a framework to go back to after an interruption; I get the impression maintenance work is much more a linear series of steps.) I can see WHY a small operation would have the Director of Maintenance also handling specific jobs, but this operation doesn’t seem to have had a way to mark where in the process someone was when they were interrupted.