Never Just One Thing: Air Midwest flight 5481 part 2
Last week, we looked at the weight and balance of Air Midwest 5481, which had been underestimated for a number of different reasons. However, although the aircraft was overweight and the centre of gravity was outside of the limits, it didn’t explain the fatal crash. The captain reacted immediately and should have been able to correct the steep climb that the Beechcraft 1900D entered upon take off. From the CVR, it was clear that she attempted to regain control of the aircraft but failed.
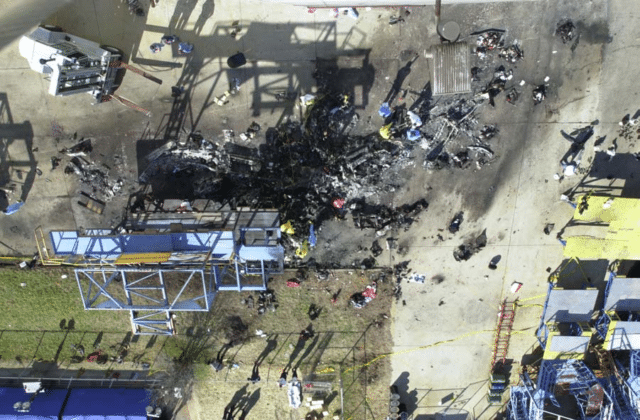
To understand why she could not, investigators had to go back to the maintenance carried out two nights before the crash. There’s an interesting connection to recent events in that the FAA, responsible for overseeing airlines to ensure that they are complying with regulations, was already aware that Air Midwest maintenance was not up to the standards that were (and are) expected. These concerns were brushed out of the way in order to support the airline in its expansion.
The FAA had assigned a principal maintenance inspector (PMI) to Air Midwest. This PMI was based at Air Midwest’s Wichita headquarters and dealt with the airline full time. After the accident, the PMI said that he tried to visit all of the Air Midwest maintenance stations two to three times per year for at least 3 days each time. He rarely announced his inspections of Air Midwest’s maintenance stations: he usually took a morning flight to a maintenance station, visited the station after arriving, and met with the maintenance managers to discuss any of their concerns. The PMI would also return to the station at night to observe maintenance operations.
From the accident report:
In October 2000, the principal maintenance inspector noted that a recent FAA inspection could not be completed because Air Midwest did not have adequate records to demonstrate that it was compliant with a requirement to use only persons properly certificated, trained, qualified and authorised for performing required inspections. The required maintenance training records were not complete, not up-to-date and in some instances could not be found at the Wichita headquarters at all. A meeting was held to investigate the issues and in December 2000, the principal maintenance inspector asked the carrier to submit a strategy to resolve issues with the Air Midwest training manual and training records. Air Midwest Director of Maintenance (also the company Vice President) agreed that they would rewrite the training manual, forward the training records to Wichita and add a manager to the training department. After many revisions, Air Midwest’s revised maintenance training manual was finally accepted in February 2002.
At the same time, the principal maintenance inspector contacted Air Midwest to say that he still could not determine whether Air Midwest was in compliance with the Federal Aviation Regulations. He voiced concern that Air Midwest’s program lacked an auditor-training curriculum. Air Midwest’s infrastructure had not kept up with its growth, he said, and the procedures in the General Maintenance Manual were inadequate. Other FAA staff were similarly concerned about deficiencies in Air Midwest’s pilot training programme.
The FAA continued discussions with Air Midwest over the next year looking for a resolution to the inadequacy of their training manuals and the required training that was still needed for their maintenance personnel.
Air Midwest had big plans to expand, based on a 2-year Department of Transportation contract worth $13.4 million awarded to Mesa Air Group for providing service to seven new essential air service markets. Air Midwest was to provide the air service starting in the autumn of 2002.
In April, the principal maintenance inspector wrote to Air Midwest that the FAA would delay Air Midwest’s planned expansion because of the unresolved concerns.
He wrote again in August, citing exactly the deficiencies which would need to be addressed before any route structure changes could be approved.
Emphasis mine. Here’s where it gets ugly.
An FAA operations supervisor advised against the delay, arguing that Air Midwest had consistently been willing to meet with the FAA to address its concerns. As a result, the FAA approved the route expansion. This meant the PMI no longer had leverage against the airline to resolve his concerns, which included the need for aircraft familiarisation training and better supervision of on-the-job training. The deficiencies in Air Midwest’s training were brushed under the carpet.
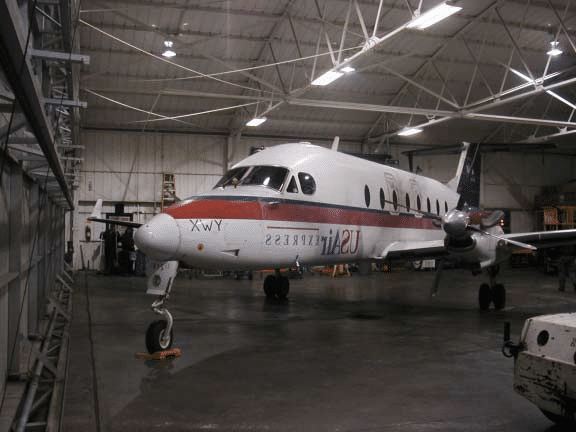
Around the same time, in July 2002, Air Midwest opened a maintenance station at Tri-State Airport in Huntington, West Virginia.
Air Midwest contracted Raytheon Aerospace LLC to provide mechanics, quality assurance inspectors and a site manager for the maintenance station. Structural Modification and Repair Technicians, Inc (SMART) supplied the mechanics.
Air Midwest was responsible for all of the maintenance performed and yet there was only one Air Midwest representative at Tri-State airport, the regional site manager who worked the day shift. There was a high turnover of mechanics at Tri-State airport; one manager estimated that the average length of employment for SMART employees was three months.
Weekdays at Tri-State airport, the overnight shift started at about 22:00, and usually one aircraft was scheduled per night. Between five and seven maintenance personnel normally worked the overnight shift and they remained on duty until the work was completed. The aircraft would arrive around 22:30 and the shift would end about 06:30. Maintenance personnel said that they were not pressured to return an aircraft to service. They described the workload as “fairly stable”.
The Air Midwest Continuous Airworthiness Maintenance Program included a periodic service check, a routine check, a detail check and a structure check.
The detail check was divided into six different phases, which are known as detail one to detail six. One major aircraft section is inspected during each phase. A different detail phase is checked every 200 hours along with a routine check. Details one to six must be completed for each aircraft each year. Detail six covers the aft fuselage and empennage (tail assembly).
It was the night of the 6th of January 2003, two nights before the accident, when N233YV was brought in for its detail six maintenance check.
Five of the six SMART mechanics on duty that night had worked at the site for less than eight weeks. Not one of them had completed training for the detail six maintenance check.
Air Midwest required a manager to complete on-the-job training before being allowed to perform a procedure unsupervised; however, there was no guidance as to how to provide on-the-job training. Air Midwest audited the Tri-State Airport maintenance station in November 2002. The training for new hires was considered satisfactory, although the auditor reported that overall staffing was not sufficient.
The foreman was responsible for providing training to the mechanics and for signing off their on-the-job training records. He told investigators that if a mechanic hadn’t done a job before and there was someone available who had previously done the job, he would assign the job to the experienced mechanic and the other would be trained as time permitted.
He was not on duty that night but assigned the Raytheon quality assurance inspector the task of providing on-the-job training for performing an elevator control cable check to a mechanic who had previously done control rigging work on DHC-8 aircraft.
The foreman routinely assigned on-the-job training to the quality assurance inspector, who believed that it was standard practice for inspectors to provide this training.
In fact, the inspector should not have been providing on-the-job training but apparently no one had trained either the foreman or the inspector in that detail.
That night, the inspector did not feel he needed to supervise the mechanic closely because the mechanic had previous flight control rigging experience. Also that same night, the inspector was providing on-the-job training to two SMART mechanics on specific tasks to do with the detail six maintenance check, which consists of an elevator check, a rudder check and a trim tab check. Neither of the mechanics being trained had previously performed a complete detail six check.
The inspector had performed elevator control system rigging once before. It was his first time training two mechanics while also performing inspector duties. The investigation report notes that current regulations (as of 2003) did not explicitly prohibit inspectors from training a mechanic on a task and then inspecting that same task, although the benefit of a “second set of eyes” to ensure that errors are detected and corrected before returning the aircraft to service is lost.
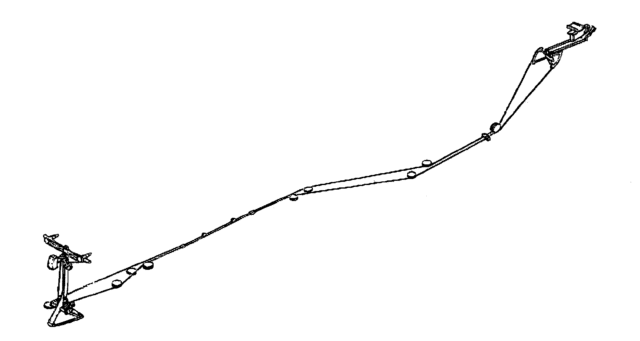
The pitch control system (also sometimes referred to as an elevator control system) is mechanically operated on the Beechcraft 1900D. The primary elements are the elevators, the control column and the connecting rods and cables.
The left and right elevators are attached to the trailing edge of the horizontal stabiliser, which is mounted at the top of the vertical stabiliser. When the pilot pushes forward on the control column, the elevator trailing edges move down, which results in the aircraft pitching AND (Aircraft Nose Down). When the pilot pulls back on the control column, it moves the elevator trailing edges up, which results in the aircraft pitching ANU (Aircraft Nose Up).
Before that night of maintenance, the Beechcraft 1900D had the full range of downward elevator travel available, 14° to 15° as specified in the Beechcraft 1900D Airliner Maintenance Manual.
One of the mechanics was given the job of inspecting the elevator control cable tension. The checklist said that the cable tension was to be checked according to the procedures in chapter 27 of the Raytheon Aircraft Beechcraft 1900D Airliner Maintenance Manual. The aircraft maintenance record had a note on the 6th of January that the elevator cable tension was low.
The mechanic said he was supervised by the quality assurance inspector as he adjusted the cables to the proper tension range. He filled in the word card to say that the ANU cable had been adjusted to 57 pounds and the AND cable to 62 pounds tension.
The form had a required inspection item stamp and was filled in to say that the elevator cable tension had been adjusted and the operations check was normal. The stamps show the roles: AM for the mechanic and DI for the designated inspector, which shows at a glance that the mechanic signed off on the work and the inspector checked it (and if appropriate, QA to show that the quality assurance inspector inspected it). Air Midwest’s Maintenance Procedure Manual states that “no person may perform a required inspection if [that person] performed the item of work required to be inspected.”
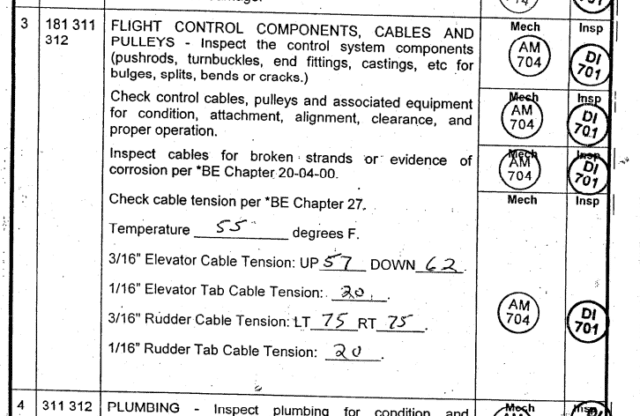
The mechanic’s on-the-job training records show that he completed training on the detail six inspection procedure on the 7th of January, 2003. The mechanic said that he performed the elevator and rudder checks but not the trim tab check on the night of 6th of January. He also told accident investigators that while he was adjusting the cable tension, he bypassed several steps of the complete elevator control system rigging procedure.
To be clear, the Beechcraft 1900D Airliner Maintenance Manual did not contain a stand-alone procedure for checking elevator cable tension, as called for on the detail six work card. So although the card appeared to simply call for the elevator cable tension to be checked, the manual had no procedure for doing this without rigging the entire elevator control system.
The quality assurance inspector said that he discussed with the mechanic which steps could be bypassed and confirmed that he allowed the mechanic to adjust only the cable tension.
So, the procedure for the elevator control system rigging says to locate and remove the flight compartment seats, carpet and floorboards on the right side of the passenger compartment to gain access to the elevator cable turnbuckles. But the mechanic says that the quality assurance inspector told him that he did not need to follow step c, to remove the seats and floorboards, in order to comply with the rigging procedure. Instead, he gained access to the rig-pin hole through a small access panel which the foreman had shown him.
And so the night went on, with the mechanic also skipping step f, step g, step h and step i as not necessary. He found that he could adjust the cable tension by tightening cables without releasing them before the adjustment, allowing him to bypass the release of cable tension in step n. He also bypassed step s, to perform the control column support roller inspection procedure, because he decided that it was not required.
The mechanic, with the agreement of the quality assurance manager, skipped all of these steps and still they both somehow believed that they were complying with maintenance requirements.
The most telling was the final step. They agreed not to perform step u, the Flight Data Recorder pitch adjustment procedure, because the quality assurance inspector said that he didn’t think that a Flight Data Recorder was installed on the aircraft.
He was wrong: most if not all Beechcraft 1900D aircraft have a Flight Data Recorder and this one was no exception. It was not hard to verify: the flight data recorder was in plain sight in the aft cargo compartment and there was a circuit breaker for the Flight Data Recorder in the cockpit. They never checked.
If they had attempted the calibration, they would have discovered that it was no longer possible to move the elevator to the first setting at 14° because the elevator travel was restricted to about 7° AND (nose down). In other words, they would have known immediately that the elevator was misrigged.
The mechanic did check the controls in the cockpit after he had adjusted the cable tension. He ran the elevator full travel a few times and checked the cable tensions to make sure they hadn’t changed. It appeared that the elevator travelled from stop to stop and there was no one at the tail of the aircraft observing the limited movement of the elevators.
The Raytheon quality assurance inspector was not authorised to decide whether a specific step of the maintenance manual could be skipped. However as the work card specifically mentioned a cable replacement and not cable tensioning, both men believed that the steps were not necessary.
This wasn’t a case of carelessness. The inspector never tried to hide what they did; he said that he did not think the manufacturer intended for mechanics to follow the entire rigging procedure and that the entire procedure had not been followed when past cable tension adjustments had been made to other aircraft in the past.
Again, he was wrong. All of these steps were required and for good reason. He was right about the other aircraft, though.
The aircraft was returned to service. The flight crews who flew the Beechcraft did not notice that the aircraft elevators were no longer responding as they should.
The only visible sign of the misrigging was a change in the elevator resting position. The normal elevator resting position is between 14° and 15°. After the maintenance, the elevator resting position was about 7°. But the flight crew doing the walk-around would not have been able to see this, because the horizontal stabiliser on the Beechcraft 1900D is about 15 feet (4.5 metres) above the ground.
To recreate the scenario, the investigators misrigged a test aircraft. Walking around the aircraft before and after, they did not see any conspicuous change.
This brings us back to the weight and balance.
Air Midwest flight 5481 was the most aft-loaded of the flights after the misrigging event. When the nose pitched up, the captain immediately reacted by pushing forward, commanding the elevators to bring the aircraft’s nose down. Both flight crew attempted to forcefully bring the aircraft back under control but the incorrect elevator rigging, which reduced the ability of the elevator to travel nose down, meant that the crew were not able to control the pitch.
Who was to blame? Air Midwest Vice President and Director of Maintenance wrote to the board to state that a review of the Raytheon Aircraft Beechcraft 1900D Maintenance Manual did not have clear instructions. Air Midwest argued that there were deficiencies in the manufacturer’s elevator control system rigging procedure and that if more explicit instructions were included, the elevator misrigging could have been avoided. And finally, Air Midwest said that the staff members in question were lying when they said that they believed that they were fulfilling requirements and that it had always been done this way.
Air Midwest Submission to the Hearing
The question is why did the foreman, the inspector and the Raytheon Aerospace site manager, all experienced, licensed A&P mechanics, state during the investigation and at the Public Hearing, that they had interpreted the RII rule correctly, when in fact they had not. Air Midwest, Inc., believes that the three individuals clearly knew and understood the RII requirement. However, since they had not complied with either the FAR or the Air Midwest manual requirement, they choose to offer a different interpretation to explain their actions. Each of the three individuals evaded answering direct questions about the RII rule and the OJT sign off requirement–they never directly answered any of the pertinent questions posed by the Safety Board staff or any of the Parties. Instead, the record indicates that they responded to questions on the RII issue and the OJT sign off/qualification issue with the statement that they had done it this way since 1999 at MESA, Arctic Slope, Raytheon Aerospace LLC and Air Midwest. The FARs and the maintenance manuals are clear on these subjects yet the three individuals would have the Safety Board believe that for four years, at different companies, these blatant violations of the regulations were commonplace.
Air Midwest also revised the detail six card, adding specific steps for performing an elevator cable tension check.
Not surprisingly, there were some staffing changes over at Tri-State airport. The quality assurance inspector lost his authorisation to perform maintenance and RII inspections on Air Midwest aircraft. He is still employed by Raytheon Aerospace LLC and working as a mechanic at another station. The mechanic also lost his authorisation to perform maintenance on Air Midwest aircraft and is no longer employed by Structural Modification and Repair Technicians, Inc (SMART). The Raytheon Aerospace LLC site manager now works as a mechanic at another maintenance station.
A different primary quality assurance inspector and SMART mechanic were given “disciplinary time off” when it was discovered that they had falsely completed an on-the-job training record the same night as the misrigging took place. The training was for the detail six procedure including the elevator maintenance. However, the night that the training supposedly took place, the inspector was not on duty and the mechanic was unable to complete the maintenance procedure and did not perform the elevator check.
The FAA released an emergency airworthiness directive to notify all owners and operators of the Beechcraft 1900, 1900C and 1900D models of the potential to misrig the elevator control system to restrict elevator travel.
Air Midwest complied with the emergency airworthiness directive and found that of the 45 Beech aircraft they ran, seven of them were misrigged, two of them dangerously so.
Raytheon Aircraft Company received 296 reports from the initial control column sweep and stop bolt inspection. The reports showed that 40 aircraft failed this initial check and thus required another rig.
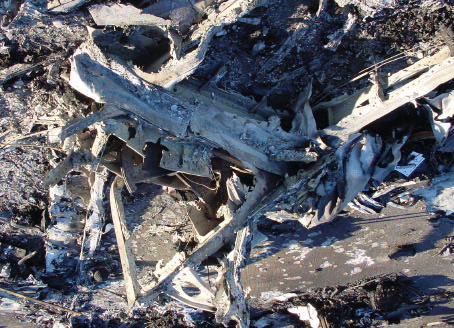
From the accident report:
Probable Cause
The National Transportation Safety Board determines that the probable cause of this accident was the airplane’s loss of pitch control during takeoff. The loss of pitch control resulted from the incorrect rigging of the elevator control system compounded by the airplane’s aft center of gravity, which was substantially aft of the certified aft limit.
Contributing to the cause of the accident were
(1) Air Midwest’s lack of oversight of the work being performed at the Huntington, West Virginia, maintenance station;
(2) Air Midwest’s maintenance procedures and documentation;
(3) Air Midwest’s weight and balance program at the time of the accident;
(4) the Raytheon Aerospace quality assurance inspector’s failure to detect the incorrect rigging of the elevator control system;
(5) the Federal Aviation Administration’s (FAA) average weight assumptions in its weight and balance program guidance at the time of the accident; and
(6) the FAA’s lack of oversight of Air Midwest’s maintenance program and its weight and balance program.
Completed in February 2004, the investigative report also pointed out that Air Midwest’s weight and balance program still included a risk of unintentional misloading when applied to the accident aircraft.
From the accident report:
If Air Midwest’s revised (May 2003) weight and balance program had been in effect for flight 5481, the flight crew would have had to take some action to bring the airplane within the Beechcraft 1900D certified weight and balance envelope (17,120 pounds and 40 percent MAC, respectively). If the flight crew had, for example, off-loaded two passengers seated in the last row of the airplane and three bags from the AFT1 cargo compartment, a calculated weight of 17,106 pounds and CG position of 35.9 percent MAC would have resulted. Even though this calculated weight and CG position would have indicated that the airplane was within the Beechcraft 1900D weight and CG envelope, the actual weight would have been almost 100 pounds more than the weight limit (17,233vpounds), and the actual CG position would have been slightly under the aft CG limit (39.9 percent MAC).
The risk of an accident like this should reduce dramatically as technological advances are adopted onto modern aircraft. Onboard weight and balance systems already exist. One, called STAN (Sum Total Aft and Nose system), uses pressure transducers on the main gear and nose gear shock struts to determine the exact weight and balance of the aircraft. At the time of the accident, the FAA had resolved that cockpit displays of weight and balance information were not reliable or accurate enough to be required on commercial aircraft. However in 2008 the FAA released an Advisory Circular recommending Onboard Weight and Balance Systems (OBWBS), because they calculate the actual weight and centre of gravity of the aircraft and remove the need to use average figures. A certified OBWBS is accepted as the primary means of providing weight and balance information.
The modernisation of the cargo industry means that it may also be possible to obtain this information without requiring additional equipment and systems built into the aircraft. When dealing with international transport on a large scale, it is critical to track weight and location of the shipments; and many large cargo companies (DHL, FedEx, TNT, UPS) have supported technological innovations in the interests of efficiency and security. It is now standard to use wireless bar code scanners for inventory tracking from acceptance of the shipment to delivery. It should be possible to quickly and unobtrusively weigh passengers as a part of check in and then track the exact weight and location of everything on board the aircraft, offering an automated calculation of actual weight and balance.
As a final footnote to this story, Air Midwest was shut down by its parent company, Mesa Airlines, in June 2008.
While I don’t wish to comment on the usual corporate attempts at blame-shifting, it seems to me that a root cause here is the innate inability of humans to deal instinctively with low-probability events. The standard pattern for people who let their feelings override their training goes something like “we’ve done it this way a few times before, nothing went wrong, therefore it’ll be fine.” And if people follow the full procedure, well, that takes longer and costs more. So both management and ground crew have an incentive to cut corners.
This is why you need detail-orientated nitpicky types to say “no, actually these rules are here for a reason”, even though it makes them unpopular with the people who just want to get the work done and go home.
Of course the FAA saying “they’ve been in violation for over a year, but we like them so we’ll allow them to continue to fly” doesn’t exactly promote an attitude of compliance either.
Yes, there seems to be a pretty clear case of normalisation of deviance here, muddied by the engineers saying “this is the way it is correctly done” and the airline throwing them under the bus. Did they know they were taking shortcuts or not ?
This was some time ago but I was horrified that the inspector was undercut like that and very glad that the NTSB called it out.
Sylvia, I’m a little baffled that ‘Before that night of maintenance, the Beechcraft 1900D had the full range of downward elevator travel available, 14° to 15° as specified in the Beechcraft 1900D Airliner Maintenance Manual.’ If all the mechanic did on the night was re-tension the cables, I don’t see how that could have made such a major difference to the control surface rigging. It seems that, on the facts you’ve summarised, the rigging must have been faulty since the last re-rig. This is supported by the mis-rigging found on several of the fleet aircraft after the accident. Is there something in the report that explains the statement that rigging had been correct?
I speak as an ex-RNZAF Maintenance Flight Commander on a couple of squadrons, who has authorised the odd short-cut.
I suspect your confusion is an artifact of my trying to keep things short and chopping out a bit too much. If I understand it correctly, while tightening the tension on the cables, the steps they skipped directly led to the misrigging:
Step f – Adjust the center-to-center length of the push-pull tube assembly between the control column and the forward elevator bellcrank to a dimension of 15.12 +/- 0.06 inches (in). M1 determined that this step was not required. The QA Inspector concurred.
Step g – Adjust the surface stop bolts on the elevator control horn support for up travel of 20° +1°/ -0° and down travel of 14° +1°/ -0°. M1 determined that this step did not require taking a measurement. M1 had manually pushed the elevators up and down to determine if the
elevator was hitting the stops, but never verified the movement at the control column.
Step h – Verify the bob weight stop bolt clearance is 0.5 +/- 0.06 in. M1 determined that this step was not required. The QA Inspector concurred
Step i – Adjust the forward bellcrank stops for 0.37 +/- 0.06 in clearance from the stop bolts. M1 determined that this step was not required. The QA Inspector concurred.
Step j – Verify the forward bellcrank stop bolts make contact before the bob weight stop bolts make contact with the weight. M1 determined that this step was not required. The QA Inspector concurred.
Step n – Remove the safety clips from the turnbuckles and release cable tension. As per the interview with M1, the cable tension adjustments were made by tightening the cables up to the desired tensions. The cable tensions were never released.
The list goes on but I think (bear in mind I’ve never rigged a thing in my life) the above shows how the re-tensioning ended up mis-rigging the flight. I suspect you will be able to make a lot more sense of this than I can, though, so if you’d like to look at section 6 of the maintenance report (from which I took the above), I’d love to hear your conclusions.
Aircraft Maintenance and Records Factual Report
Basically, the cable goes around a pulley. There are two tensioners for what is in effect a single cable, and obviously you can adjust the tension with just one of them. What happens then, though, is that the cable becomes misaligned and hits a stop before the elevator is fully down.
They should have tightened both tensioners equally, and checked their work, using the full access that removing the floor panels would have given them.
Thanks Sylvia and Mendel. I’ve now managed to find and read NTSB AAR-04/01, 1.1 ‘The AND turnbuckle was extended 1.76 inches more than the ANU turnbuckle. After the accident, Air Midwest surveyed its entire fleet of 42 Beech 1900D airplanes, which represented 25 percent of the 164 Beech 1900D airplanes active in the North American fleet. Air Midwest data submitted to the Safety Board indicated that, on average, the AND turnbuckle was extended 0.04 inch less than the ANU turnbuckle.’
I agree that the accident was caused by doing all adjustment on a single turnbuckle, and not using the rigging board to confirm movement after adjustment. I do think that Raytheon should have either produced a separate, complete procedure covering only tension adjustment, or said that full rigging procedures must be carried out any time the tension is adjusted. Something I hadn’t seen before is that the aircraft actually arrived for maintenance with a defect noting that the elevator cable tension was low – presumably pilots felt a little more free play in the system. If this hadn’t been reported I suspect that the whole procedure may have been omitted. Thus, ironically, saving a lot of lives.
I once authorised an elevator cable change on a Sioux without the official rigging board (we’d gone to Samoa without it), but we made one up and marked the travel limits on it before the change.
“These concerns were brushed out of the way in order to support the airline in its expansion.” I remember when the US Atomic Energy Commission was being described as dangerous because it was simultaneously responsible for promoting nuclear generation of electricity and ensuring the safety of this process. The AEC no longer exists; the Nuclear Regulatory Commission took over its safety functions, and the Department of Energy deals with promotion. Maybe someday enough people will realize that the FAA has the same issues, and similarly divide it.
I have my doubts about “unobtrusively weigh[ing] passengers”. An OBWBS works because the airplane is just sitting there, with built-in sensors; passengers can be relied on not to stand in a defined place for long enough that their weights can be individually determined (leaving aside the cost of systems that could approximate this). Building a scale into each and every security scanner might be possible — but that would require much more extensive tracking, and cooperation between systems not built to be compatible, to get the info where it’s needed. I suspect the least unworkable answer is a combination of more-accurate estimates, OBWBS, and procedures for offering people incentives to get off of overloaded airplanes. (I sat through an example of the last in 1995; our takeoff from Gatwick was delayed (due to late arrivals of connections) during an unusually warm summer, such that the expected outside temperature for our new slot was too high for the engines to run at high enough power to get us safely off the ground. Additional delay ensued.) I don’t expect this to be easy, but ISTM it’s necessary given the increasing amount of luggage being brought into the passenger compartment to avoid checked-luggage fees.
Re your last sentence, I caught a flight from Italy to Malta in 2019. The two bags we checked in were (literally) the only ones to come off the conveyor in Malta. The very large amount of baggage on the flight was all, somehow, carried on, despite most of it being way outside size limits and the number of bags permitted per passenger. No crew attention was paid to the issue.
I just remembered that Mendel asked about the travel board, which comes up in regards to step G — the mechanic did not state that he used the travel board for measuring the elevator deflection. I hadn’t really dug into this so I’ve shown my work here, even though I know you could happily find this.
The scan of the Raytheon maintenance manual explains that you should install an elevator travel board on each elevator at station 50.00 (step e), tighten the elevator-up cable until the elevator rises to neutral (0° on the travel board) (step p) and finally remove them from the horizontal stabilizers (step v)
In the report, it says:
Code 7700 explains it as a calibrated template which attaches to the trailing edge of the horizontal stabilizer that allows a person positioned at eye level to see exactly how far up or down the elevator has moved.
You can buy an elevator travel board which intriguingly is listed specifically as a Raytheon aircraft part.
Leaving the technical details aside, and they are deeply troubling.
I have been openly trying to make sense of a scenario where an aircraft’s C of G can be so far out that it could prevent the crew from regaining control when the aircraft stalled immediately after take-off. My process was akin to a written form of “thinking aloud”. And when I tried to come to a conclusion, I was very far out. It made no sense.
The truth as now revealed by Sylvia is deeply disturbing. It reveals a mentality of “don’t rock the boat”, commercial interest above safety standards.
The facts are very different, but there are parallels with the problems with the Boeing 737 Max. The FAA had relegated most of the supervision of standards to Boeing and the in-house culture at Boeing had shifted in favour of profits This is in fact not all that dissimilar to the leeway given to Air Midwest and Raytheon when it came to proper supervision of maintenance standards and ensuring qualifications and relevant experience of the engineering staff.
The original B737 was a short-range airliner, designed for 70 passengers.
The Max is a totally different aircraft. Short- to medium range it can carry in the order of 230 passengers. Engines, instruments, performance, systems, engines and engine management are all vastly different. Worse, the aerodynamic characteristics of the Max had also undergone a dramatic change. Essentially, the much more powerful engines have a larger diameter. In order to maintain certain features, such as the retractable forward air stairs, the engines were placed further forward.
This resulted in changes in the aircraft’s behaviour that were in fact not desirable. By now, the Max was actually a new design. But Airbus had introduced the 320 Neo. Boeing felt the competition breathing down its neck and managed to persuade the FAA to maintain the “737” type designation, meaning a vastly reduced certification process and a common type rating for maintenance- and cockpit crew.
The intricacies of the MCAS that had to counteract the changes in behaviour were “brushed under the carpet”. The flight crews did not really receive sufficient “differences training”, as a result maintenance staff did not always realise the implications of a malfunctioning or not calibrated MCAS.
Although this scenario is very different from what happened in the Air Midwest Beech 1900 crash, it suggests to me that the FAA, at least in its role as a body of supervising maintenance and certification standards, is a severely flawed, even discredited agency.
Wikipedia: “The 737-100/200 original variants were powered by Pratt & Whitney JT8D low-bypass engines and offered seating for 85 to 130 passengers.” So not quite as small as 70 passengers, but still a lot smaller than what it has become.
The FAA has been behaving debatably for a long time — witness the common type rating between the (narrow-body) B-757 and the (wide-body) B-767.
As a PS: I flew both the Fokker F27 and the F50. There is a vastly greater commonality, especially the handling characteristics, between these two types than between the 737-200 and the Max. Yet, the airworthiness authorities ruled that the difference between the F27 and the 50 was sufficient for the new type not to be called the F27-50, thereby ruling out a common type rating. With added cost for an operator wanting to upgrade.
OK Chip, 85 not 70 passengers, but as you mentioned the seating capacity of the 737 was just about doubled over the years. But that was not the point that I was making and you are right when it comes to the FAA having behaved “debatably” for a long time. I had forgotten the common rating for the B757 and 767, but even though they differ in size – quite substantially and not just in seating capacity – the actual management of these types was surprisingly similar. The F27 differed from the 50, the engines were different, with an acoustic noise cancellation system that required electronic engine- and propeller control, the pneumatic systems were replaced with hydraulics and cockpit with screens and an FMS system had been very much updated. The 50 was approved for cat 2 operations. But the actual handling of the two was not really much different and some later F27s, before the introduction of the 50, actually had a “glass cockpit” that bore resemblance to what the 50 was going to offer.
There had been a number of regional airlines in Europe that had been operating F27s. A common type rating might have made the difference between upgrading to the Fokker 50, or ordering the ATP, DH Dash 8 or ATR 42.
The 737 Max may have similarities with previous 737 variants, very strong ones even, but the model deviates substantially from the 100/200 or even the 737 Classic. How far can a type be developed down the line before it becomes a new one, requiring a new type rating?
All this suggests an FAA not fit for purpose! Am I right in thinking that whilst passengers lose their lives as a result of their horrifically deficient oversight, the worst that can happen to them is that they MIGHT (if unlucky) lose their jobs?