Engineer Sucked into Jet Engine
In an awful piece of news from Mumbai, it seems that an Air India technician died at Mumbai airport after he was sucked into an aircraft engine as the flight crew began to taxi. The current reports are all expectedly sensationalistic and it will take a while before an investigation can explain how the technician came to be in the intake zone with the pilots clearly unaware that he was there. The basic information (without the sensationalism) is from the Aviation Herald: Accident: Air India A319 at Mumbai on Dec 16th 2015, sucked engineer into engine during push back:
On Dec 17th 2015 India’s UPWA (Unemployed Pilot Welfare Association) reported based on initial interviews with their colleagues, that the aircraft was being pushed back from bay 28L at Mumbai Airport following a cross-bleed engine start, when after the push back got finished the technician/engineer instructed a helper to remove the tow bar with the engineer (56) facing his tow truck and having the engines in his back, his headset was on. In the meantime the crew got taxi clearance, the captain queried with the first officer whether the aircraft was clear, the first officer affirmed, and the aircraft started to move forward with both engines operating. The engineer remained unaware of the aircraft starting to move and was sucked into the right hand engine, the helper, who just spotted the aircraft’s movement in time, instantly sat down and was saved that way. The UPWA stated following crucial points: 1) No chocks were applied after push back had stopped, 2) no clearance signals had been issued releasing the aircraft for taxi, 3) lack of proper coordination between the two pilots and ground. The UPWA stressed: “Human Factors playing important role to have patience, avoid hurrying and follow SOPs.”
Lately I’ve been noticing a knee-jerk reaction to blame the culture when it comes to Asian “human factors” incidents and so I thought this would be a good time to revisit a case in the US in 2006 where an engineer lost his life the same way.
It was winter in El Paso, Texas; the 16th of January, 2006.
The aircraft was a Boeing 737-524, registration N32626 operated by Continental Airlines. It was manufactured in 1995 and powered by two CFM-56 series engines.
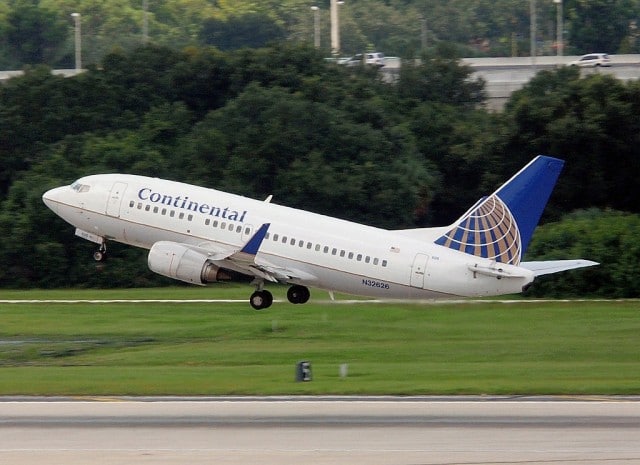
The Boeing was parked at the gate at El Paso International Airport in preparation for its next flight of the day.
The first officer walked around the aircraft for the pre-flight inspection and spotted a puddle of fluid under the right engine. The first officer brought it to the attention of the captain, who agreed that it appeared to be an oil leak. The captain radioed Continental Operations from the cockpit to request authorisation for maintenance to check the right engine. Meanwhile, the captain and the first officer continued with their preparations for the flight.
Continental El Paso Operations contacted Continental Airlines Maintenance Control headquarters and told the senior maintenance controller that the captain had noticed an oil leak. The controller contacted an FBO to investigate the pilot report.
An FBO (fixed-base operator) is a commercial business who offers services on an airport, including maintenance. Contract maintenance is frequently used at airports where the airline does not have maintenance available.
The maintenance manuals were held at Continental Headquarters Maintenance Control who transmitted extracts of the manuals to the contractor when specific maintenance was required. This procedure meant that all of the contractors would use the most current procedures without having to maintain publications libraries across several airport contractors.
Julie’s Aircraft Services, an El Paso FBO, was an approved contract agency who was under contract to provide on-call maintenance resources for Continental.
Three mechanics arrived at the aircraft to investigate the right engine. They opened both sides of the fan cowl panels and the mechanics asked the captain to conduct an engine run so they could watch for the source of the oil leak.
There were no written procedures in place at the airport requiring the flight crew to contact either the Continental El Paso Operations or El Paso Airport Air Traffic Control prior to starting the engines.
The first mechanic positioned himself on the inboard side of the right engine.
Boeing recommend the use of safety lanyards, straps with clips either end similar to those used by rock climbers, when performing maintenance near running engines. Continental interviewed mechanics at their main maintenance facility in Houston and discovered that nearly all of the mechanics did not use lanyards and were concerned about being able to quickly release and escape the lanyards in an emergency.
The second mechanic positioned himself on the outboard side. He’d done his private pilot’s licence in 1962 and had been working on planes since 1966. He’d been working for Julie’s Aircraft Services for nine years.
The airport operations for Continental Airlines gives the ingestion danger zone for this configuration of 737 as a 13-foot radius around the front of each engine and extends to a 5-feet radius behind the front of each engine. The maintenance practices manual for Boeing Aircraft defines the inlet hazard zone as encompassing a 9-foot radius around the front of each engine and extends to five feet behind the front of each engine on the inboard side and four feet on the outboard side.
The passengers were boarded via an air stair truck, as the jetway was inoperative and, by this time, all passengers and crew were on board except for one passenger in a wheelchair, who was to be boarded using a lift truck.
The captain started the engine and let it run at idle RPM for three minutes while the initial oil leak check was performed. One of the mechanics called the captain using the ground intercom and said that they’d detected a small oil leak. He asked the captain to increase the engine power to 70% for three minutes.
At the time, a Letter of Agreement was in effect between the Air Traffic Control Tower and the Airport on the subject of Engine Run-up Procedures. The Letter of Agreement specifically disallowed the crew from increasing the engine power for testing.
“Except for power-up associated with beginning taxi, engine power is restricted to idle RPM on one engine at a time for a maximum of five minutes while on any parking or service apron areas, including the terminal ramp.”
However, neither Continental Airlines Operations at the airport nor Julie’s Aircraft Services had a copy of the Letter of Agreement. In fact, none of the tenants at the airport had it; the agreement had never been distributed by the airport.
The captain spoke to the mechanic on the ground intercom.
Captain: | Clear back there? |
Mechanic: | Yeah, we’re all clear |
Captain: | ‘kay, here goes! |
The captain increased the engine power.
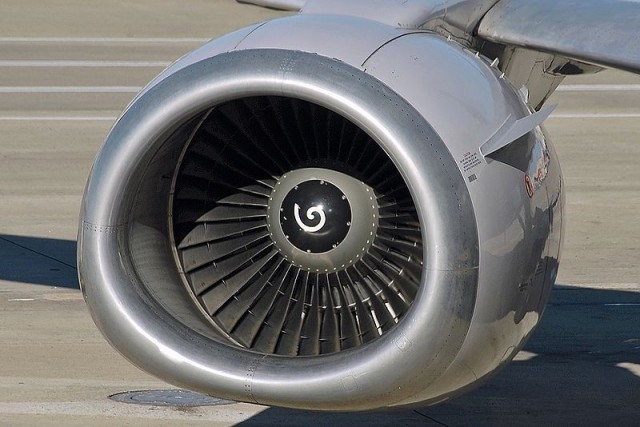
The mechanic at the outboard side stood up and stepped into the inlet hazard zone.
The other two mechanics and a passenger on the aircraft were horrified to see him sucked into the engine.
Operating at 70%, the right engine basically inhaled him. He died instantly.
The captain felt an engine buffet which increased in intensity before an engine compressor stall. He retarded the power level back to the idle position. The first officer informed the captain that something had been sucked into the engine. The captain immediately cut off the start lever.
The senior maintenance controller noticed that the flight departure time was drawing near and he still had not heard back from Julie’s Aircraft Services. He tried to phone operations to find out what what was going on but couldn’t get through to anyone. He then tried to call Julie’s directly. When he finally got through to them, the accident had already happened.
The condition of the remains were such that the El Paso County Medical Examiner could not perform an autopsy nor toxicological tests.
The investigation confirmed that Julie’s Aircraft Services did not make contact with Continental Airlines Maintenance Control for approval or documentation.
The surviving mechanic who had been positioned inboard was asked how and why he conducted the engine run with no maintenance procedures from the airline. He said that engine oil leaks were common and he continued without instructions because of his past experience.
Continental made a number of changes as a result of this accident. They purchased an additional 23 safety lanyards following the accident and “reinforced procedures” for their optional use. They also updated their check lists, along with a new one to coordinate communication between crew pilots, mechanics and operations before performing engine runs. They enhanced their contract maintenance training syllabus and created an engine safety training video which was mandatory viewing for all maintenance providers.
The National Transportation Safety Board determines the probable cause(s) of this accident as follows:
- the mechanic’s failure to maintain proper clearance with the engine intake during a jet engine run, and the failure of contract maintenance personnel to follow written procedures and directives contained in the airline’s general maintenance manual. Factors contributing to the accident were the insufficient training provided to the contract mechanics by the airline, and the failure of the airport to disseminate a policy prohibiting ground engine runs above idle power in the terminal area.
A tragic example of how a cluster of errors and omissions can lead to the perfect storm.
I remember this accident and the NTSB report, and I’ve always been curious about their finding of probable cause. I understand that the airline violated airport procedure in conducting the engine run at the gate, etc, but how did that actually contribute to the accident? It sounds like the mechanic just had a mental lapse, or lost situational awareness, or whatever you want to call it, at exactly the wrong place and time. Could have happened in a designated maintenance area just as easily.
Erica, you are only partially right.
Many jet engines idle at 55-60% and 65 may be needed to “break” the inertia of the aircraft and get taxiing. So 70% may sound high but it isn’t really as big a deal as it would seem. But nevertheless, it is higher than normal. Jet aircraft deliver their power in the higher range of power, depending on the engine type and number of “spools”, expressed in %N1 (usually fan speed).
Reading the report, it would seem that the aircraft was not parked at a gate. But the location on the apron, passengers already boarded, would have created time pressure on the crew to get the problem fixed. Mechanics working on aircraft at the maintenance base are not normally under the same time pressure because they have to fix a problem with an aircraft at the point of departure
So, indirectly, the location did contribute to this horrible accident – in my opinion.