Dreamliner Pre-flight Maintenance
On Wednesday, the 16th of June, British Airways flight 881 from Moscow arrived at Heathrow airport. The aircraft was registration G-ZBJB, a Boeing 787-8 which had been converted from a passenger aircraft to cargo transport. This was one of four Dreamliner aircraft that British Airways began operating in 2013.
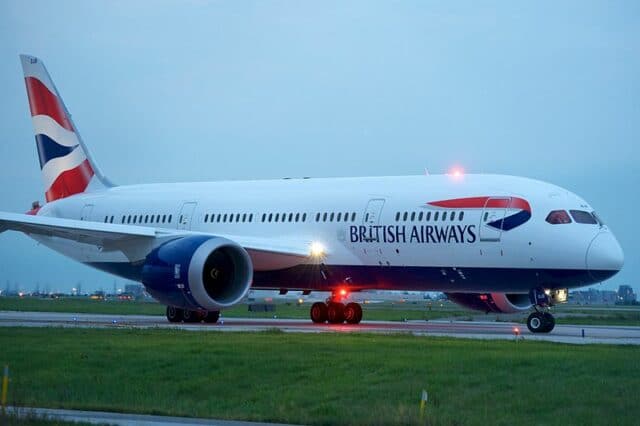
The next scheduled flight for the Dreamliner was on Friday the 18th, a cargo flight from London to Frankfurt. The flight crew arrived at the airport at 6:20 and went straight to the aircraft.
There, they found three ground engineers in the cockpit doing pre-flight maintenance. The aircraft had thrown up three status messages related to an Acceptable Deferred Defect, a door-closed solenoid valve related to the nose landing gear.
The engineers told the flight crew that they needed about forty minutes to finish up and the estimated “off blocks” time, that is, the time when the aircraft will leave the gate, was revised to 07:20.
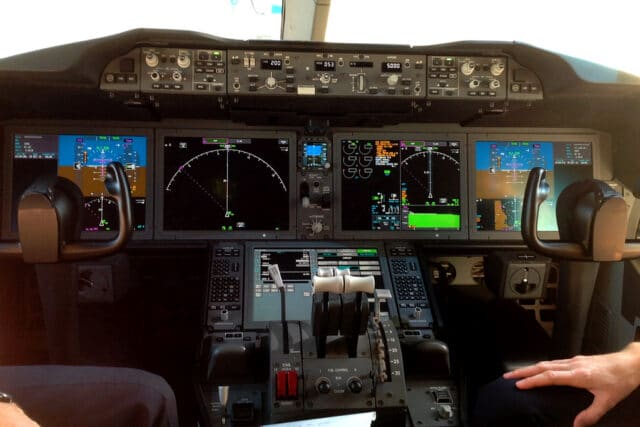
In the cockpit, the first officer sat down in the right seat with the lead ground engineer remaining in the left seat. The overseas engineer moved to the galley in the centre of the cabin. The captain and the other engineer exited via the airstairs.
The aircraft was being loaded with cargo via an aircraft pallet loader positioned under the forward cargo door on the right side of the aircraft. There were four members of the loading team: one was loading the cargo into the plane, one operating the “Tarmac Transfer Vehicle” at the rear of the pallet, one was supervising and helping to load the cargo onto the vehicle. The fourth was sent to open the rear cargo doors.
The report does not mention the weather but presumably it was good as the captain did the walk around. Then he returned to the flight deck with the dispatcher and a ground technician who was also a part of the ground engineering team. The technician reported to the lead ground engineer that the walk-round inspection was complete. He then took a seat in the forward galley where he could watch the progress on the flight deck.
The lead ground engineer in the cockpit was using his laptop to work throiugh the Nose Landing Gear status messages related to the known issues. They weren’t critical and had already been confirmed as Acceptable Deferred Defects, which meant that they could be dealt with at a later date, for example with other, scheduled maintenance. The ground engineering team simply needed to carry out the appropriate Dispatch Deviation Guide procedure and clear the maintenance messages.
This procedure is a basic test which requires the engineers to apply hydraulic pressure and then cycle the cockpit landing gear selection, that is, take the gear lever from down to up and then down again.
Obviously the problem with this is that the landing gear would retract and then extend again, which isn’t something you want to do on the ground. To get around this, each gear has a downlock, which enables you to lock the gear in the down position by inserting a pin into a hollow cylindrical hole. Now you can cycle the gear lever without actually pulling the landing gear up.
The lead engineer asked the lead mechanic and another mechanic to fit the landing gear locking pins. He also told them to attach the ground communications headset to the external connection in the nose landing gear bay.
The two mechanics collected the five landing gear locking pins and went to the nose landing gear to fit the first one. The lead mechanic wasn’t quite tall enough to reach the locking pin hole without steps but the other man was, so he asked the second mechanic to fit the locking pin, pointing to the location of the hole. Then they made their way to the right main landing gear.
On the way, the second mechanic spoke to one of the loading team who was standing on the pallet loader, letting him know that they were going to apply hydraulic power to the aircraft. This can cause the aircraft to move slightly, so the mechanic warned the man that he needed to stand clear of the aircraft and lower the pallet loader to keep it away from the cargo door.
Meanwhile, the lead mechanic picked up a set of steps and placed two of the downlock pins on the right main landing gear and another two on the left landing gear. His task complete, he returned to the flight deck and told the flight engineer that the pins were all fitted. Then both mechanics returned to the nose landing gear, where the lead mechanic plugged in the headset and put it on.
He heard the lead engineer asking him to confirm that the landing gear pins were fitted and he said yes, they were. The second mechanic stepped clear from the aircraft and stopped by some nearby vehicles to watch.
The lead engineer had the appropriate section of the Aircraft Maintenance Manual open on his laptop and so, following the procedure, he applied hydraulic pressure. Then, again following procedure, he asked the lead mechanic to verify that the locking pins were in place and that the loading team were clear of the aircraft.
The lead mechanic glanced at all of the landing gears: all five warning flags on the downlock pins were clearly visible. All members of the loading team seemed to be clear but he bent down to look under the loading platform just to make sure there were no feet visible there. Everything seemed as it should be, so he confirmed to the lead engineer in the cockpit that the pins were fitted and that the pallet loader was clear of personnel.
The lead engineer pressed the LOCK OVERRIDE button and selected the landing gear lever to UP.
The nose landing gear retracted and the nose of the Dreamliner crashed to the ground.
British Airways Boeing 787-800 (G-ZBJB, built 2013) suffered a nosegear collapse while parked on a remote stand at London-Heathrow Intl Airport (EGLL), UK. @MZulqarnainBut1 pic.twitter.com/KzWcmdN1zO
— JACDEC (@JacdecNew) June 18, 2021
The nose of the aircraft crushed the articulated arm of a ground power unit, destroying the cable arm. The lower forward fuselage, nose landing gear doors and both engine cowlings struck the ground and were damaged. The left-side door connected to the airstairs was ripped off of its hinges as the aircraft lurched forwards, leaving the door hanging from electrical cables.
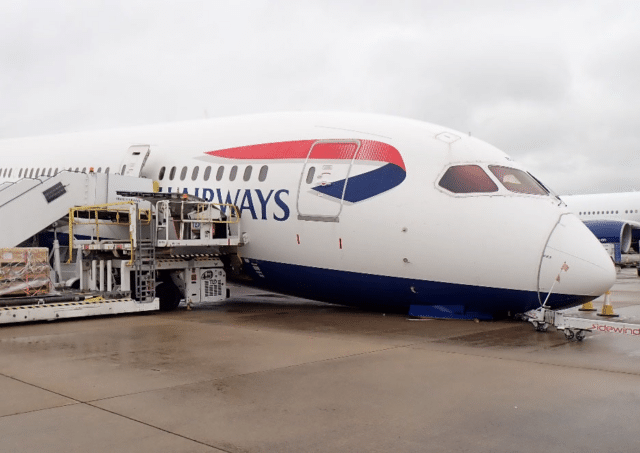
One of the ground loading team who was on the pallet loader was struck by the cargo door as it dropped. Inside the cockpit, the lead engineer and the first officer were thrown forward. Three personnel in the cabin and galley fell to the floor.
During the recovery operations, investigators found that the nose landing gear downlock pin had not been placed into the correct hole. It had been placed into a very similar hole next to the downlock, the nose landing gear apex pin bore.
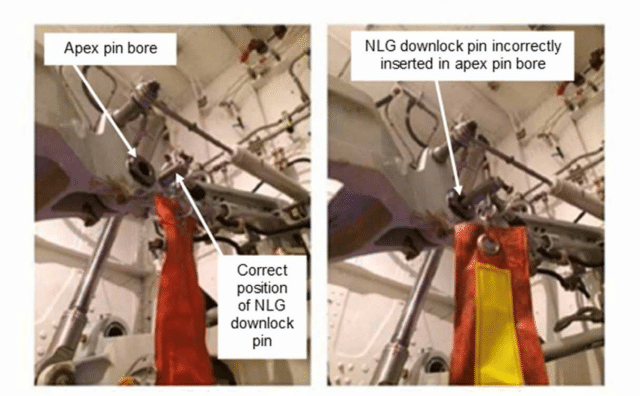
This isn’t the first time this has happened. In 2018, another operator suffered an almost identical accident when during maintenance, the downlock pin was placed into the nose landing gear apex pin bore and the nose lever gear was moved to the UP position, leading to the nose landing gear retracting. As a result of this accident, Boeing released a service bulletin for installing an insert into the apex pin bore in order to stop the downlocking pin being inserted into the wrong hole. In January 2020, the FAA made this service bulletin mandatory as an Airworthiness Directive for all relevant Boeing jets, allowing for a compliance period of 36 months.
Obviously, this particular aircraft had not yet had the insert placed in the apex pin bore, although British Airways have stated that they are now expediting the procedure on their remaining Dreamliners.
The final report is still in progress at the British AAIB. Thanks to Mendel who spotted this special bulletin.
Some red faces, no doubt.
Reading this, there is obviously a small but very significant difference between the 787 and most (older?) types of aircraft.
Raising the undercarriage on the ground is in most, actually all except for aircraft with fixed landing gear, aircraft prevented by a so-called “squat switch”, in many aircraft two are fitted on both main undercarriage struts. This will prevent the gear to be retracted when on the ground, full stop. UNLESS the switch malfunctions of course.
So normally, lifting the landing gear handle to the “UP” position is not possible. The squat switch will as an extra precaution also bring a baulk into position that physically prevents the handle to be moved when on the ground. Testing the landing gear and its proper retraction will thus require the aircraft to be brought in a hangar and be put on jacks. A rather time-consuming procedure.
The landing gear pins (the captain has to verify that all are on board and properly stowed before departure) are just an extra precaution.
Apparently, Boeing devised a maintenance shortcut whereby the engineers can override the squat switch and the baulk, and place the gear handle in the “UP” position on the ground. Which, obviously, requires the proper installation of the gear pins to prevent inadvertent retraction of the wheels… OOPS !
My former copilot on the Corvette joined BA and indeed told me that the captain will perform the walk-around when the weather is good him or herself. Why? Because, he told me, the walk-around is good for an extra payment
The Corvette was based at Shannon Airport and looked after by a company called SRS.
Once they were doing a major check on a Boeing 707 for which the undercarriage had to be removed for overhaul. So it was placed on jacks. But the overhaul took a few weeks and in the meantime the jacks were required for another job.
The solution was found by going to a garden centre where they bought the entire available stock of bags of moss peat.
The bags were placed under the wings and tail section, the jacks were removed and the aircraft rested safely on a bed of moss peat.
But when the landing gear was returned, ready to be installed, the bags had been compressed under the weight of the aircraft.
So the mechanics had to return to the garden centre to re-peat the process. ;-)
Good to see the second line of defense working, like looking for any persons below the plane and standing back ‘just in case’.
It wasn’t working, there was a guy on the pallet loader who suffered an injury.
Mitch,
I think that was the third line of defence?
Btw there is no separate handle to operate the nose landing gear. The locking pins were correctly fitted to the main gears that is the reason why only the nose gear retracted
Who in their right mind designs TWO similar holes in a crucial piece of equipment? And what does this say about the airline regulator asking for a fix to be done in THREE years? Meanwhile, a simple a sticker the landing gear that read “WRONG HOLE!” would have sufficed.
First, he two holes are not at all similar.
Secondly, over the service history of the aircraft, obviously very few mechanics have been stupid enough to use the wrong hole.
Thirdly, this is the correct hole if e.g. you want to ultrasound check the bearings, or other purposes.
Therefore, forthly, there is paperwork an procedures that need to updated along with the fix (even if the fix was “just a sticker”); and it also needs to be documented.
Because of that, fifthly, it is most effective to implement this directive as part of a general scheduled overhaul of the aircraft; I don’t know how often these are required to occur, but if it’s “every two years”, the a 3-year deadline seems a good way to ensure that airlines will implement this change as part of these overhauls, which maybe are done by Boeing anyway?
Don’t worry Richard. Mendel put me in my place on an earlier post too. Which is why I only come to this website sporadically now.
It’s just a difference in opinion?
I don’t intend to be impolite (I’d never start a comment with “who in their right mind”), but I’m usually quite direct, and that can come across as rude; I swear it’s not intended as such, and if it did appear so, I apologize.
This post is a followup to https://fearoflanding.com/accidents/ba-boeing-737-8-nosewheel-collapse-at-heathrow/ . The comments there show that Colintd (Colin T. D.?) mentioned the special bulletin, not I.
I’m wondering what the proper procedure for the lead meachnic should have been to ensure that the handlers were all clear: ideally, he should’ve counted them.
I predict that the guy who thought that inserting a round pin into the eye hole of a hinge would lock anything won’t have much of a career as a mechanic…
Thanks Mendel for the acknowledgement (and you’re right the TD is for my two surnames!).
What I’d love to know is exactly how high up the holes are, and what the view from the ground looks like? The suggestion in the press that the lead mechanic was too short, makes me wonder if it might not be right at arms reach. Whilst the pictures in the report clearly show the wrong hole in the pivot pin, these seem to have been taken from an elevated position. I wonder whether from the ground it might not be as obvious?
Was the real issue that using a ladder it would be clear, but from the ground, inserted by someone tall with long arms, it might not be?
I’ve been trying to find a good photo on this from the ground and have been struggling. However it appears from those I’ve found that the holes are indeed right at arm’s reach, and critically the nose wheel doors seems to prevent easy sideways viewing of the holes, instead forcing you to look up at a very oblique angle. As such the photos in the report, talken from a ladder, don’t seem to represent what the mechanic would have seen.
Can anyone with experience of flying this aircraft comment on the actual ground visibility of this area of the nose wheel?
What is it about the British and Safety Pins?
I met the pilot of this ****up in Gibraltar when we needed a lawyer to handle a property transfer. He screwed up the legal work as well, what do they say, “unlucky in the sky, unlucky in court”?
Here’s the story:
https://aviation-safety.net/wikibase/82611
The pilot(s) happened to be present but that does not necessarily mean that they were involved in this, or any, maintenance procedure. The only one is the pre-flight or “walk-around” inspection that they are legally entitled to sign off. Splitting hair? Maybe, but aviation is rife with rules and regulations.
I remember that, many many years ago, in the maintenance base of airline “X” a mechanic working on a ladder dropped a screwdriver. An electronics engineer walking by picked it up and handed it back to the mechanic. It caused a walk-out because the electronics engineer had handled something that was not in his department.
If a piece of luggage on a trolley, on its way to be loaded in the belly of an aircraft, falls off the trolley nobody not directly involved is allowed to pick it up, even if the trolley is stationary, nearby waiting e.g. for a taxying aircraft to pass. Sometimes the rules are very bureaucratic.