Boeing 737 Runway Excursion at Kathmandu
On the 19th of April 2018, a Malinda Air scheduled passenger flight from Kathmandu to Kuala Lumpur rejected take-off and overran the runway. The Malaysian Ministry of Transport investigated and released their final report last month.
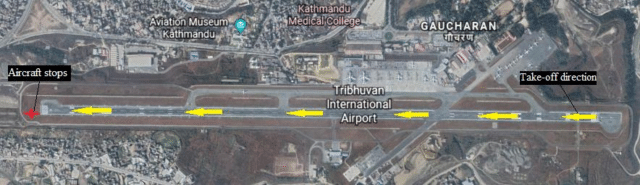
The aircraft was a Boeing B737-900 built in 2013, registered in Malaysia (9M-LNJ) and operated by Malindo Air, a Malaysian low-cost carrier based in Kuala Lumpur.
The flight crew had arrived at Kathmandu the night before for the scheduled flight from Tribhuvan International Airport to Kuala Lumpur International Airport.
Tribhuvan International is located at the foothills of the Himalayas in Kathmandu Valley. It has an elevation of 4,395 feet with the Himalayan mountains along the northwest to the southeast of the airport, with high terrain ranging from 25,000 to 29,000 feet above mean sea level. The 10,000-foot tabletop runway has steep drops on either side.
The cabin crew arrived that day, working a flight from Kuala Lumpur to Kathmandu. It was a night flight back to Kuala Lumpur and the weather was poor. The flight crew briefing before the flight was focused on the weather and the engine out procedures at Tribhuvan.
An engine failure on take-off is always challenging but it is particularly problematic at Kathmandu because of the high terrain surrounding the airport. Normally, the Captain would then brief the cabin crew but after the event, the Senior Cabin Crew Member reported that the cabin crew had not received a briefing before the flight.
Other than this, the pre-flight activities seemed normal and no issues were found. The first officer remembers specifically that he physically checked that the speed brake was stowed correctly as a part of the departure review.
The captain was the pilot flying. He backtracked and started his take off roll at 228 feet from the threshold of the 10,000-foot runway, applying maximum take-off thrust. The aircraft swiftly reached V1, also know as “the decision speed”.
This is something of an odd name because really, it is the speed at which the decision is about to be taken out of your hands.
If there is an issue during the take-off run, the Captain (whether Pilot Flying or Pilot Monitoring) must make the decision to either continue or to reject the take-off. That decision should be taken in time to start the manoeuvre for RTO (Rejected Take-Off) by V1. Having decided to reject the take-off, the captain announces “STOP” and starts the rejected takeoff manoeuvre (and, if not the Pilot Flying, assumes control of the aircraft).
Once the aircraft reaches the speed after which a rejected take-off would be dangerous, the Pilot Monitoring calls V1. After this point, the Pilot Flying is committed to continuing the take-off. This is usually trained very stringently in the simulator after multiple studies that showed that most of the decisions to reject the take-off made at or after V1 were not necessary and in fact was more dangerous than taking off with the fault. Generally, if the aircraft is not going to be able to take-off and turn around safely, the situation becomes known before V1 is reached.
V1 is the minimum speed necessary to continue* in the case of an engine failure, so even in the case of a failure or an engine fire, it is safer to take-off. There are some instances where rejecting the take off in the final stages of the take-off run have been the safer option, but they are very rare and a runway overrun is pretty much assumed.
(* See Rudy’s comment; I put this badly)
In this instance, the V1 speed was 141 knots.
The flight crew said that just as the Boeing 737-900 reached V1, they were startled by the sound of the Take Off configuration warning. Some part of the aircraft was not set up correctly for take-off but it was not clear what the issue might be.
The captain reached for the speed brake to ensure that it was correctly stowed. The Take Off configuration warning continued.
The captain had no way of knowing what the configuration error was and he was taking off in the dark, in the rain, towards high terrain. He decided to reject the take off.
At the point when the Captain started the RTO manoeuvre, four seconds had elapsed since the 739 had reached V1 and the aircraft was travelling at 154 knots calibrated air speed.
The Boeing 737 flight crew operations manual procedure for initiating an RTO above 80 knots and before V1 says that the captain must, without delay:
Simultaneously close the thrust levers, disengage the autothrottles and apply maximum manual wheel brakes or verify operation of RTO autobrake.
If RTO autobrake is selected, monitor system performance and apply manual wheel brakes if the AUTO BRAKE DISARM light illuminates or deceleration is not adequate.
Raise SPEED BRAKE lever.
Apply reverse thrust up to the maximum amount consistent with conditions.
Continue maximum braking until certain the airplane can stop on the runway.
At the same time, the First Officer verifies that the thrust levers are closed, the autothrottles disengaged and maximum brakes applied. He or she needs to verify and call the status of the speed brakes and reversers as well as any action items which have not been done.
What actually happened was that the autobrake was disconnected immediately while the captain applied pressure on the brake pedals. The autobrake would have applied 3,000 psi of brake pressure but at the point that it was disconnected, just 800 psi was applied. After a few seconds, the captain asked the first officer to also apply pressure to the brake pedals. The flight data shows that the pressure on the brake pedals increased from 30% to 90% over ten seconds, at which point maximum pressure was applied.
Reverse thrust was used but only to the second stop, rather than maximum reverse thrust.
The aircraft skidded off the runway still travelling at 30 knots before coming to a stop in the soft ground about 50 metres (165 feet) after the threshold.
Once the aircraft came to a halt, the captain considered an immediate evacuation. However, the first officer pointed out that there were no indications of fire or malfunctions other than the Take Off Configuration warning. He suggested that an emergency evacuation was not necessary and the captain agreed.
The captain made a call to the cabin:
Remain calm. Cabin crew and passengers remain seated.
The senior cabin crew member repeated the announcement in the cabin. The passengers remained calm and did not panic. They mostly remained seated, except for one passenger who went to the aft galley to ask for a glass of water.
The flight crew started the auxiliary power unit (APU) and shut down both engines.
The first officer maintained communications with the tower. He switched on all of the external lights and, within a few minutes, the airport authorities arrived on the scene.
Steps could not be placed on the soft ground where the aircraft had halted, so they instructed the crew to disembark the passengers using the slide from door 2R.
The captain made an announcement to say that they were leaving the aircraft but that this was not an evacuation. The cabin lights were switched on and the cabin crew asked the passengers to move to door 2R, where they were to sit down and then use the slide to exit the aircraft.
The captain called the airline’s Director of Flight Operations to report the situation but the phone number in the aircraft was out of date and the captain found that he had phoned the former Director of Flight Operations who was no longer with the company.
Meanwhile, all of the passengers and cabin crew disembarked safely, with no injuries. The only damage to the aircraft was a flat tyre.
The captain was the last to leave the aircraft. He left the APU on and did not pull out any circuit breakers. The reason for pulling the circuit breakers is to remove power from the Flight Data Recorder and the Cockpit Voice Recorder. Both of these recorders have a limited amount of storage which is continuously overwritten. As a part of the emergency procedures, the flight crew are expected to disable the FDR and the CVR once safely on the ground and stopped in order to preserve the information. Even when shutting the aircraft down, the circuit breakers are often used so that if power is restored, for example by maintenance, the recorders are not activated.
However, the captain did not do this. By leaving the APU on, he left both devices quietly recording the silence until maintenance engineers arrived.
When investigators interviewed the captain, he confirmed that he knew “the 11 items to be considered to reject the take-off” as documented in the Quick Reference Handbook. However, he felt confident that his decision to reject the take-off after V1 was correct, taking into account the bad weather and the high terrain on their departure route. Taking off into the dark rain towards the Himalayas with an unknown fault on the aircraft must have felt like suicide.
Maintenance investigated the aircraft to find out why the Take-Off Configuration warning had sounded. They could find no faults. The systems report showed that the speed brake lever was not in the DOWN detent, that is, the fully stowed position. But both the first officer and the captain remembered checking the position of the speed brake lever and finding it correctly in the down position.
This was a known issue.
In 2015, Boeing had issued a technical bulletin to address several reports of take-off configuration warnings caused by the speed brake handle not being in the DOWN detent, that is, the speed brake handle wasn’t stowed away correctly, despite checking the Speed Brake in the DOWN DETENT being both in the preflight procedure and the checklist.
The speed brake handle position is one of the airplane components monitored by the Takeoff Configuration Warning System. If the speed brake handle is not in the down detent or the speed brake warning switch is not properly adjusted, the intermittent Takeoff Configuration Warning horn sounds.
The recommended technique to ensure the speed brake is properly stowed is to push down firmly on the top of the speed brake handle. This technique will not prevent a false warning if the speed brake warning switch is not adjusted correctly but it should prevent a warning due to the handle not being fully stowed.
The maintenance team confirmed that the brake lever switch was out of range and thus giving an intermittent signal. After a minor adjustment to the switch, the aircraft take-off warning test passed with no further issues.
This technical bulletin goes on to say that if the take-off configuration warning occurs during the take-off roll before 80 knots, the flight crew should reject the take off. It does not state what the flight crew should do if the warning sounds after 80 knots but before V1.
At the point where the captain rejected the take-off, the aircraft was travelling at a calibrated airspeed of 154 knots.
This information was not in the Malindo Air B737 checklist and it did not come up during the briefing. There were no instructions as to how to react if the Take-Off configuration warning sounded.
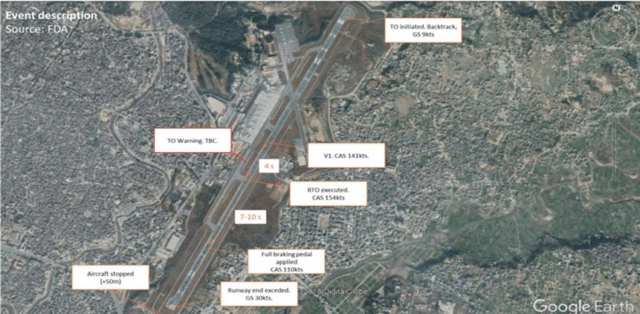
Probable Cause
The probable cause of the runway excursion was due to the PIC attempted to reject the take-off at high speed, following take-off Configuration Warning. The rejected TO was initiated at the speed of 154kts, which is above V1. In addition, the maximum braking was not applied throughout the stopping.
The report concludes with eight safety recommendations, all for Malinda Air, which mostly come down to making sure that the pre-flight briefings and training include more and better information on rejecting take-offs and that training reinforce the importance of this and the importance of the Captain’s briefing to the crew, not to mention the importance of pulling out the circuit breakers after an incident.
After the incident, Boeing were asked by Malindo Airways to supply the criteria and inspection needed to ensure that the landing gear fuse pin was in good condition after travelling along rough ground.
Boeing knew nothing of the incident and had not been contacted by the investigating body.
Their response to Malindo Air included Operational Guidance to clarify that V1 is the maximum speed at which the captain must take the first action to reject a take off. Having taken the decision to reject, the captain then did not use the full braking power available to him.
During the RTO, reverse thrust, wheel brakes and speed brakes were utilized; however not to their maximum capability which would have aided in reducing the airplane speed even further.
Boeing used the Quick Access Recorder (QAR) data and publicly available information such as the weather and the runway conditions that night to create a ground track and a performance analysis.
The analyses showed that if the captain had rejected take-off at V1 and executed the procedures perfectly, the aircraft could have stopped within 9,190 feet, leaving 817 feet of runway, even accepting the 228 feet behind the aircraft when it started its take-off roll. However, initiating the rejected take-off at 151 knots, ten knots over V1, required 10,289 feet stopping distance with no margin for error. The full runway length at Tribhuvan is 10,0007 feet. Even if the flight crew had done everything perfectly, they were never going to stop on that runway.
You can download the final report in English, including the Boeing response to Malindo Air, here: https://www.mot.gov.my/en/AAIB%20Statistic%20%20Accident%20Report%20Document/SI%200418%209M-LNJ.pdf.
What could possibly happen to an airliner that reaches V1 as expected for aborting the takeoff after V1 to be necessary? Short of both engines falling off the wing, or the cockpit going dark?
V1 is already calculated to get you in the air safely. If you don’t have a plan to get out of the mountains with one engine (or perhaps the added drag of the speedbrakes) in IFC, maybe you should not take off at all?
I ran out of time but I was looking at a study of rejected take-off decisions after V1 and it included justified/correct decisions.
That said, these cases are very rare and the study was focused on “how do we stop late rejected take-offs” rather than supporting the idea that it might be a worthwhile thing to do.
So in other words these “rare cases” were cases of “if it’s stupid and it works, it’s still stupid and you got lucky”
Haha, also possible!
A recent (2017) event was an MD-83 which aborted after V1 and went off the end of the runway – https://www.ntsb.gov/investigations/AccidentReports/Pages/AAR1901.aspx
In this case, the MD-83 elevators are capable of jamming in a way that cannot be detected from the flight deck. The NTSB specifically found that the captain could not have known that something was wrong until after attempting to rotate, and a quick decision to abort (plus excellent CRM on both pilots’ parts to commit to the abort) prevented it from being much worse.
Mendel: “What could possibly happen to an airliner that reaches V1 as expected for aborting the takeoff after V1 to be necessary?”
A failure to rotate springs to mind. Similar to Nathan’s comment, a friend of a friend had that problem with a Fokker 100 at Stanstead, England. She pulled back on the yoke but the aircraft didn’t rotate. I’m not clear if the yoke moved or not. The only option, of course, was to reject the take off. Fortunately the runway was long enough for that not to be a drama. The aircraft was inspected, rather carefully I imagine, but no fault was found.
Well, there were no injuries and damage was minimal.
It is interesting to note that the crew seemed unaware of a discrepancy, a design fault if you like, that could cause a configuration warning even if the crew had checked the speed brake handle position and were satisfied that it was stowed properly.
Under the circumstances the decision to abandon take-off was in itself not wrong. A wrong configuration set-up can potentially mean that the aircraft will not be controllable once airborne. Better to run off the end of the runway than to lose control after take-off, especially from a high density airport, in bad weather and with surrounding high terrain.
The rejected take-off, once the decision was made albeit late, seems to have been handled poorly and the checklist not properly finished.
Not a great performance, but not catastrophically poor either.
“V1 is the minimum speed necessary to take off in the case of an engine failure…” I disagree with that.
V1 is the maximum speed at which the aircraft, taking into account an engine failure, can either accelerate to a safe take-off speed or brought to a stop on the remaining runway, including stopway if available.
This is not the textbook definition, but close enough.
V1 comes before Vr, the speed at which the aircraft is rotated in order to take off. An increased time lapse may be calculated if the (paved) runway is short. The aircraft will roll until the call “rotate”. In order to meet initial climb requirements there may be a clearway after the runway ends. A few seconds are also incorporated in the V1 calculations to allow for the crew to react.
V1 is therefore also known as “engine failure recognition speed”.
Yes, V1 and the subsequent procedures, take into account performance affected by a possible engine failure, but this is not always the reason why a take-off should be discontinued.
As shown in this article. Both engines delivered normal power.
Oh fair! I knew what I meant but that’s not what I said. I’ve added a star and I’ll rephrase tomorrow.
I know everyone here knows the “swiss cheese theory” of accidents. I think this is one of the few times when all the holes didn’t line up and people died. They almost did though!
Sylvia is correct when she mentions that in most cases it is better to continue take-off rather than to abandon at high speed. But there are always exceptions.
Modern airliners are more than capable of getting airborne safely with a problem, even an engine failure. This of course assuming that the crew made proper use of the “TL tables”. Airlines provide reams of manuals to be carried on board (actually allowance is made for them in the dry weight of the aircraft). Airway manuals, operations manuals, procedures such as (expanded) checklists. The TL tables are extracted from very complicated calculations. In essence, they have been worked out by specialists. In my day one of those was Flygprestanda. This company provided manuals with the take-off data for individual airports and runways, for individual types of aircraft. It will take into consideration possible take-of from an intersection. For a take-off run starting from the beginning, the calculations are based on the distance from the end of the yellow taxiway guideline. So it is not always poor air(wo)manship to leave a small portion of tarmac behind. The calculations incorporate not only the take-off, but take into account the performance in case of a return; the computers also take into account the requirements in case of a missed approach with an engine failure after take-off. In theory the crew should be able to do this using the aircraft’s operations manuals. But it would take hours to do this accurately. The airline typically would purchase these tables for every airport (and type of aircraft) that they use. The variables would be entered, like temperature and wind. The crew then would extract the relevant data such as V1, rotate, V2, Vfr, Venr and Vref in case of a return after take-off. All complex but it soon becomes routine. Of course, I don’t know if, and to which extent, in modern aircraft some of these manuals have been replaced with computerised versions to be displayed on the screen or on-board dedicated laptops.
But to get back to the topic: generally it is preferable to “take the problem into the air”.
In this case, I am not so sure if Gene is correct. The crew did not cover themselves in glory, but there is a difference between a crew, during a rejected take-off, not managing to bring the aircraft to a stop before the end of the runway and a disaster. The aircraft was still under some sort of control, and not on fire. A typical runway, in most cases, does not end right at the fence at the far end.
Is the CVR data lost forever given that the APU was not shut off ?
Yes, both the CVR and FDR data was recorded over.
Not too familiar with this type of aircraft But in case the crew gets a warning of ‘wrong configuration’ in the circumstances they faced than I think he can not be faulted for the decision he had taken. Wrong configuration could be wrong or no flap slat setting also which would make the aircraft un-flyable.
I am not familiar with the B737 either, but if an improper flap setting would trigger a configuration warning it would come on when take-off power is selected and brakes are released. If this warning is activated during take-off, and at a high speed, this would be a difficult call for the captain.
There simply is little or no time for an evaluation, but since it just MIGHT be an indication that something has suddenly failed that could make the aircraft unflyable, the decision to abandon take-off in itself was not necessarily wrong.
The subsequent handling of the incident WAS poor. It should at worst have resulted in an extra waiting time to allow overheated brakes to cool down. This waiting time could then have been put to good use to evaluate what had happened, and more likely than not resulted in no more than a delay and a second takeoff. In other words: if properly handled it would have been no more than an entry in the aircraft log and a captain’s report to the fleet captain.
It is mentioned that there had not been a cabin crew briefing.
The airlines that I have flown with – the ones carrying passengers – had their own crew procedures for the cabin crew. The senior cabin crew member had full authority and although officially answerable to the captain, woe betide a captain who would overrule him or her without good reason.
Usually the briefing would be minimal. The senior cabin crew member would come in the cockpit to report “cabin ready”. If there was anything special, worth mentioning, this would be discussed there and then.
Any really special circumstances, such as VIPs on board, or a particular requirement that would involve a non-standard procedure would indeed lead to a more detailed briefing before the passengers would board.
How to act in the event of an emergency is part of the cabin crew training. It always, per definition, is an unexpected event and therefore not part of an extra crew briefing.
So I do not understand the relevance of the senior cabin crew member reporting that a cabin crew briefing had not taken place before departure.
What I understood from the accident report was that it was standard procedure at the airline for the cabin crew to receive a pre-flight briefing. It was referenced twice and then again in the safety recommendations:
To be honest, I’m more bemused that in an accident report that took almost two years, they didn’t think to contact Boeing for comment. The added appendix with the data from Boeing is addressed to Malindo Air in response to their query about the maintenance required.
Yes the lack of communication with Boeing is not speaking well of the maintenance department of Malindo Air, unless they knew about the problem and deemed it under control.
On the other hand, a cabin crew, as I mentioned, will have received specific training related to their role, and laid down in their manuals.
It used, in the time when airliners had piston engines, be part of the formal flight preparation in the airline’s crew briefing room. The cockpit crew and the cabin crew would assemble and go over the flight, route, passengers and their requirements.
In the jet age there simply is not that much time allocated for all that.
The briefings have been laid down in the manuals.
For the cockpit crew every departure is different: Airport, runway status, time of day or night, summer or winter, elevation, weather and precipitation, including that at destination, surrounding terrain, performance, fuel requirements, NOTAMs, SID and aircraft status, as well as action and procedures in case of a problem after take-off. They can all vary and therefore are part of the pre-departure flight crew briefing.
There are a number of questionable acts by both the aircrew and the airline — although a number of the crew’s decisions had to be made quickly. But what really stuns me is that Boeing’s fix for a handle that wouldn’t travel far enough to be recorded as set (while both being set and appearing to be set) amounted to “Hit it harder!” In the computer world we would alternately snicker and complain about manufacturers who suggested “percussive maintenance”; ISTM that this is of a piece with the attitudes that led to the 737-MAX disaster.
Chip, I agree. It sounds a bit like the old days of television. Sometimes the thing would not work, or only display flickering lines and hisses.
A firm tap on the (rather large) box usually would solve often the problem.
But now we live in the computer age.
The cavalier attitude of Boeing with regards to “percussive maintenance” (I love that !) was a major factor in this incident. Fortunately it did not lead to an accident. Chip suspects that this was similar to the attitude of Boeing, covering up a design flaw in the 737 MAX with a “gizmo”, the existence of which was not properly revealed, let alone adequately explained to the operators.