Maintaining the Stores
We don’t often talk about parked aircraft because it is not very common for them to be involved in crashes. However, one of the side-effects of these pandemic times is the pressure put on aircraft storage and maintenance, where it is often unknown how many aircraft will need to be stored for how long.
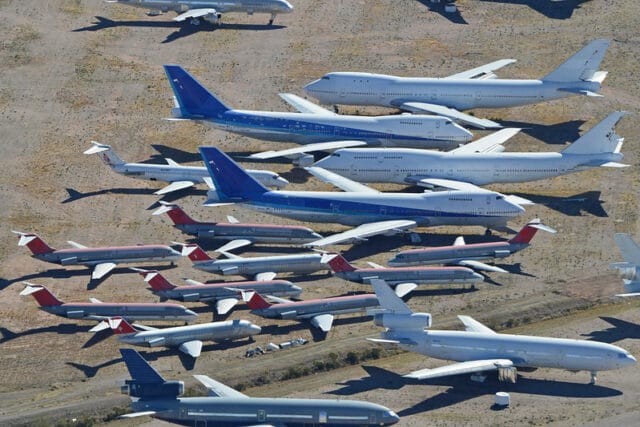
NASA’s Aviation Safety Reporting System (ASRS) have kindly granted permission for me to republish their collection of reports which highlight what can go wrong in these situations with recommendations by the technicians as to how to avoid the problem. I found it very interesting as it is full of real-world examples of just how things can go wrong. I hope you enjoy it too.
Maintaining the Stores
Aircraft storage, whether short-term or long-term, presents a multitude of challenges and a complex set of problems for all those entrusted with preserving the nation’s aircraft. The airline industry has experienced a paradigm shift where economic necessity demands that aircraft be stored for an undefined period of time, yet be capable of generating revenue in quick fashion and in the safest manner possible. Aviation Maintenance Technicians (AMTs) are the industry champions who accomplish this critical preservation and de-preservation work. Skillfully conquering today’s obstacles, they are resilient, perceptive, and responsible while implementing creative solutions to difficult storage problems.
Aircraft storage problems can be numerous and convoluted. Established procedures are sometimes difficult to implement or may not work in a new storage environment. Difficulties may arise in achieving agreement on a best approach or solution, and procedural steps may lack completeness or may need revision. Human Factors, as always, play an extensive role in problem development and resolution.
Here is a sample of maintenance incidents that occurred during aircraft storage operations. Valuable lessons may be gleaned by observing complexities of each situation, studying Human Factors involved, and dissecting responses and philosophies of the AMTs.
Parking Pandemonium
This Aviation Maintenance Technician described a frustrating event that was fueled in a new environment by vague and ill-defined procedures, differing opinions, confusion, inexperience, and a steep learning curve.
It was a busy night which included a lot of new guys assigned to this aircraft. There were several hours of very heated conversation on a parking/storage procedure that the supervisors were implementing with no guidance or help to accomplish this procedure.… Supervisors [were] telling us one way, and veteran leads [were] saying something different.… Both sides [were] arguing and going round and round about what should be done and what procedure we should follow. On a side note, the procedure has changed hourly, daily, weekly, and monthly. It’s still a fluid situation. I was given the Aircraft Maintenance Log (AML) at the end of the night to review the paperwork. The aircraft had been finished by the AMTs, and all the paperwork was done, stamped, and put into the system, but with an open write-up in the logbook. [The original write-up] couldn’t be closed, so I was advised to close out the [original] discrepancy and [reenter the] open item.
The bantering [had gone] back and forth. The discussion [was heated over] use of the General Procedures Manual (GPM) or Aircraft Maintenance Manual (AMM). Should we use the parking rule and cover the engine intakes and cover all static ports? Too many different procedures [were proposed] with no real guidance on what action should be taken. Everything that went on that night was in a large part…part of the dirty dozen Human Factors.
The procedures should be the same. [They] changed four or five times that week alone. I couldn’t see the original write-up. Also, the closing out of the logbook without leaving any open items [was improper]. The…proper procedure should be communicated, reviewed, and discussed before implementing it at zero hour. So many questions [existed] on how to accomplish [this scenario] with safety being the strongest concern.
Unmarked Hazards
An AMT reported a deficiency in a procedural task card during aircraft storage operations. The card failed to provide proper notice that should have been included for a hazardous condition. The AMT proposed a remedy.
This task card instructs [the technician] to drain water out of the fuel tanks. Stored aircraft fuel tanks have been treated with the hazardous chemical Biobor JF. There is no caution or warning in the document making the technician aware that precautions need to be taken. The fuel that is removed from the tank has to be disposed of in a particular way. There is no caution or warning for that either.
Include cautions in the step for Personal Protective Equipment (PPE) requirements and disposal of treated fuel. Include requirements in document headers under [equipment and] tooling, and under references to any applicable maintenance documents.
Gentlemen, Start Your Engines
Communication and procedural discipline were key in this A320 engine run during aircraft preparation for storage. The AMT described breaks in the chain of responsibility and in the sequence of events that led to an uncommon result.
I was made aware that Aircraft X had undergone an engine run of both engines on [date] with no oil in either engine or gearbox.… My name had come up as having signed the task card for draining both engines of oil and that the cockpit was not tagged per the AMM. I did not drain the tank or apply any part of the AMM regarding lock out, tag out (LOTO) [procedures].
On [date], I was assisting [another] mechanic during an aircraft storage preparation of Aircraft X. There were some initial questions regarding compliance with block XX of the task card as it relates to draining the oil.
After discussions with our Lead Mechanic, we decided that since it was late in the shift, and to avoid any questions for the oncoming shift regarding what needed to be done, I signed off the item at block XX on the [tablet] (actually YY on the archived copy) and made a write-up with directive instructions for a pass-down of what needed to be done going forward.
After a log page creation, the midnight shift signed for the draining of the oil per the AMM, and the next day, the log page was closed out after the remaining items in the initiating text were accomplished.
We had also discussed the extreme possibility that someone MIGHT run the engines with empty [oil] tanks, and that the mechanic [on duty] would, in addition to work accomplished by the midnight [shift], make an OPEN log page item for increased logbook visibility of the empty [oil] tanks on both engines.
Mechanics are obligated to properly document all work accomplished and defects noted. Any new write-ups or updates to existing logs should have been made immediately and the supervisor notified. Read all associated log pages, AMMs, job instructions etc., and UNDERSTAND what is being done and why. If there are ANY questions, mechanics should STOP until the actions to be taken are understood. In conclusion, KNOW the status of the aircraft by reviewing the logbook and the crew turnover briefing as necessary.… Emphasize to all run crews the importance of the proper use of checklists. Run mechanics are the critical link in this series of errors that could have prevented the [engine] runs from taking place. Lastly, my personal and professional opinion is that these two engines may not be safe for continued operation.… Why? Due to the inability to actually verify, with no margin for error, what internal damage could have occurred by running engines with no oil in the [oil] tanks or the gearboxes. A verbal or written recollection should be suspect, unless it can be backed up with run data possibly captured by the aircraft systems for verification of statements made about this event. If the no oil situation was missed, what makes the Company and FAA feel justified that the rest of the statements are true with no corroboration? Safety of the equipment should be of prime concern here. Err on the extreme side of safety, please.
Ghost Traffic
Contemplating a Pitot/Static task related to aircraft storage, this AMT noted that the specific procedure did not address a procedure-induced consequence. As written, the procedure could have negatively impacted airborne traffic and ATC.
I was assigned the tasks to drain and flush [Pitot/Static lines] and test Pitot/Static circuits on Aircraft X as outlined in job card #XXXX. I accomplished this task while working with [other] technicians…in accordance with the procedures found in the job card #XXXX.
The job card failed to ensure that the Mode S Transponders were disabled. [Disabling] prevents test altitudes from being transmitted.
Revise the job card procedures to include steps to prevent Mode S transponders from transmitting test altitudes.
Returning to Service
This AMT discovered a serious problem that had a major impact on initial flights following aircraft reactivation. Corrective steps are suggested as effective mitigation.
As aircraft come out of storage, circuit breakers (CBs) and systems have not been reactivated correctly, causing numerous rejected takeoffs or returns to airfields.
I suggest a task card or work assignment on an aircraft coming out of storage as a last item before aircraft release, depicting a graphic of that fleet’s specific CB panels and an instruction to visually check all CBs to be pushed in except those that are deferred, etc. Also, a Category 3 check should be assigned, which could capture most system failures due to improper reactivation. The best prevention would include a high-power runup.
I suspect we will see a number of issues over the coming months as aviation begins a slow recovery and already aircraft are being put back into service. I think it will turn out to be critical that Aviation Maintenance Technicians such as these keep an eye out for simple mistakes that could be made as the rush to get back on track intensifies.
Sounds to me like an accident waiting to happen
Sloppy maintenance procedures, improperly kept records, essential warning placards not prominently posted in the cockpit. Confusion about who did what, disagreements between the teams, items logged as “signed off” although the engineer in question denies that he had carried out the procedure. My goodness, this tops just about everything that I have heard regarding poor maintenance standards. And that is over the period from 1965 and 2008.
The only good thing is that these aircraft, after having been laid up for some time, will be checked over by engineering teams (although, reading Sylvia’s article that does not instill a lot of confidence) before being put back in service. They will be test flown and positioned at the airline’s base where their own engineers will inspect them. Many airlines will dispatch engineers to oversee the process of recommissioning them at the storage facility itself..
It is high time for aviation to resume. According to the latest news, Aer Lingus is fast running out of funds and the parent company, IAG, is restructuring to comply with EU rules.
What this will mean for the travelling public – not to mention the airlines’ employees – remains to be seen.
How many jobs will be lost? Will there still be a market for cheap fares air travel? The market will probably be there, but the airlines may have to raise their ticket prices. Which may well start another spiral: now upwards. Higher fares will mean less passengers, which will put more upwards pressure on the ticket prices.
The issues about recommissioning aircraft that have been laid up are only part of the problem.
We are not out of the woods yet.
I wonder how many of the people documented in this article fly with their families and just trust or hope that everything will end well.
Mike,
I hope that the airlines that own these aircraft will do their “due diligence” and go over these aircraft with the proverbial fine comb before release to service. There is little or no doubt in my mind that this will be the case.
I just came across another story, not the same subject but “sideways related”: If I understand it correctly, it is about the Boeing “737 Max” (AGAIN!).
There is some pressure now from the airlines to get back “up and running”. This also means: taking delivery of the Max that was again cleared by the FAA. When Boeing was getting a number of them that had been in storage ready for operation, in a number of them there were electronic faults that emerged during testing.
The cause is that Boeing in some, not all, of these aircraft has changed the rivets that fix frames housing electronic units to the airframe itself.
These rivets are important as they allow the current to flow BACK to the “earth”. The new type does not offer the same bonding as the other, previously used as standard. This means more resistance in the reverse electrical flow to the airframe. In turn, when in use for some time – the duration of a flight – they heat up, causing more resistance and failure, or malfunctioning of the related systems. In extreme cases, it may cause a fire (although that is not likely).
As a result, the FAA has issued an AD, effectively grounding a number of 737 Max – again.
This is a positive move. It demonstrates that the FAA is serious about restoring confidence in their supervision of airworthiness standards.
But it does not instill confidence in Boeing. It certainly is not doing much to restore confidence in what once was probably the world’s most respected aircraft manufacturer.
Maybe the covid pandemic had a positive effect of safety? Suppose these aircraft had been delivered without this fault, a different kind of rivets in SOME, being discovered? What would the outcome have been if an investigation would be unable to determine the cause of a certain malfunction because they did their tests, not aware that the aircraft undergoing these tests had the correct rivets?