Unintended Tail Dragger: Prolonged Tail Strike at Milan
I can’t believe this video from Milan taken by CCTV last month. I’ve never seen a tail strike quite so… prolonged.
The video was taken on the 9th of July 2024 at Milan Malpensa Airport in Italy and reported on by Corriere Della Sera (in Italian). The eleven-year-old Boeing 777-300ER, owned by Latam Airlines and registered in Brazil as PT-MUG, was operating flight LA8073 from Milan to São Paulo, Brazil. I’ve not seen any numbers for souls on board but the 777-300ER’s configuration data as listed on Planespotters.net (C38W50Y322) is for 38 Business Class, 50 Premium Economy and 322 Economy.
The CCTV surveillance footage captured the aircraft attempting to take off from runway 35L. The nose is high in the air with the Boeing’s tail scraping along the runway as a grey plume of smoke forms. As they were already at take-off speed and with most of the runway behind them, the crew continued in hopes of getting the aircraft into the air. Eventually, the video shows the Boeing gain enough airspeed to lift off and climb away.
Once safely off the ground, the flight crew climbed to 5,000 feet and informed Air Traffic Control that they would be returning to the airport to have the aircraft checked over. They then climbed another thousand feet and entered a holding pattern, circling for over an hour to burn off or dump excess fuel, reducing the weight of the aircraft.
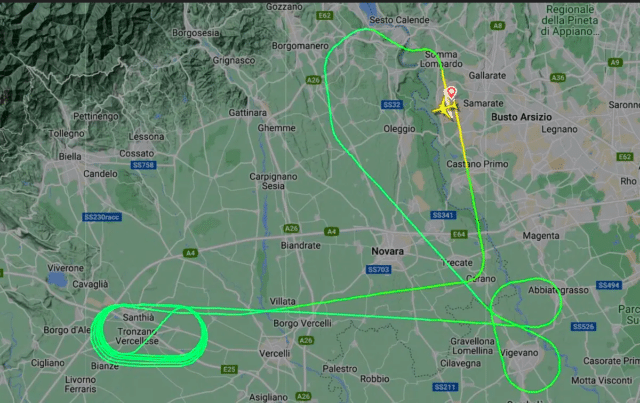
They then made an emergency landing at Milan on runway 35R. The Boeing landed safely and was able to taxi to the gate. There were no injuries to passengers or crew. The aircraft was grounded.
Based on the Boeing’s ASDB data, it flew the 9,500 kilometres back to São Paulo on the 14th of July and is still located there.
Local media initially reported that the back end suddenly dropped after an apparent malfunction; however, the first comment I saw on the matter was “Oh dear, someone has badly miscalculated the take-off data on that aircraft.” This seems like the more likely answer to me.
There are a number of tail strike incidents caused by the take-off weight being logged as lower than it actually was. This affects the take-off performance calculation, as the airspeed required for take-off is lower if the aircraft is lighter. The Pilot Flying gently applies back pressure on the control column, pitching the aircraft nose up to transition from rolling on the ground to flying in the air. This transition of lifting off is called rotation. However, if the take-off performance calculation is off, the heavier aircraft cannot achieve sufficient lift at that speed to safely rotate, and the tail strikes the ground as the aircraft struggles to take off.
Under normal circumstances, the Boeing 777 takes off with a pitch angle from 7 to 9 degrees, with the tail lifting off at around 8.5°. The pitch angle looks closer to 10° in the video.
As we can see from this video, once the aircraft gathers more speed, it is able to lift off and enter the climb.
There are many checks and balances which should catch a slip like this, as the wrong weight has serious consequences: not just that the airspeed is too high or low for rotation, but that all of the V-speeds are off, which affects go/no-go decisions.
Generally, the sequence is pretty simple. The crew gives the final fuel figures to the load controller. The load controller also verifies whether all planned passengers are accounted for and receives the final baggage and cargo weights from the airline staff. The loadsheet is then generated from this information and passed to the flight crew. The captain checks the loadsheet and signs it. The captain then enters the information into his or her Electronic Flight Bag and reads the data aloud so that the first officer can confirm the data and also program it into his or her own Electronic Flight Bag, as well as the Flight Management System. Then the two pilots will crosscheck the take-off performance calculation, including the take-off reference speeds.
I make it three specific checks where someone should notice if the weights or speeds are not as expected. But obviously, it doesn’t always happen that way.
The same aircraft had an incident in 2016, when it suffered electrical problems and had to land overweight. Twelve tyres burst on landing and it was out of service for two months.
Another aspect is that the Boeing 777 has Tail Strike Protection (TSP) specifically for this circumstance. The TSP system automatically adjusts the elevator in an attempt to limit over-rotation during takeoff. If the TSP was activated and functioning correctly, the pilots would have had to override the TSP inputs to continue at that pitch. Under normal circumstances, as soon as the aircraft did not rotate, the best option is to stay on the runway and gather more speed.
The Italian agency for flight safety, (ANSV) has opened an investigation. This is a rough translation:
The ANSV has opened a safety investigation into the serious incident that occurred on July 9, 2024, at Milan Malpensa Airport involving the Boeing 777-300ER registration PT-MUG, flight LA8073 of the airline LATAM Brasil. After collecting the initial evidence, used for the correct classification of the event, the ANSV initiated a safety investigation, classifying the event as a serious incident.
As per ICAO Annex 13, the investigative bodies of Brazil (country of the operator) and the US (country of manufacture) have been invited to take part.
In 2020, the Dutch Safety Board released a report on Erroneous takeoff performance calculation, Boeing 777 (pdf) following a tail strike at Amsterdam Airport Schiphol. In this instance, the load sheet was manually corrected when a passenger did not show, but instead of reducing the full load of 299,075 kg by 100kg, it was corrected to 229,075, making for a difference of 70,000 kilograms. The Dutch Safety Board strenuously recommended that Take Off Performance Monitoring Systems be developed and required in order to catch this issue before the aircraft is on the runway.
At the time of writing this report the overall feasibility of TOPMS has still not been demonstrated because of the complexity of such a system. As a result, no technical specifications or guidance materials to define the operational performance of such a system have been drafted. At the same time, takeoff performance occurrences continue to occur, and therefore the development of technological solutions is still urgent. Systems detecting gross input errors and deviations in parameter settings or comparing predicted and actual aeroplane acceleration during the takeoff run are systems that are considered feasible as a first step towards a more complex TOPMS.
To end on a lighter note, a comment on PPRuNe from DogTailRed2 made me laugh out loud. It says only: “Probably needs worming.”
As aircraft get larger, the distance between the main landing gear and the tail increases.
It is a simple mathematical exercise to calculate the nose-up angle at which the tail may strike the runway at rotation.
This will limit the maximum angle at which the nose may be raised during rotation, obvious.
Modern airliners are being produced with various fuselage length. E.g. Superliner 123 dash 4, -5 or -6. Of course, I am making this up but all versions will be covered by one type rating.
But the differences may be more profound than the length, and subsequently the seating capacity.
There may be differences in engines, range and some operating, even procedural criteria.
Handling will be one of the differences.
The Douglas DC 8 initially seated about 150 passengers, but in later stretched versions this was increased to around 270..
Due to the substantially longer fuselage, there was a real risk of a tail strike in these versions, and the crew had to rotate twice: Still on the runway the nose was not to be lifted beyond a certain angle. One of my IFR renewal instructors was a DC 8 captain, later 747. If I remember correctly the nose was first lifted to a maximum 8 degrees at VR,, and only after getting airborne and at a certain height above the ground could the pilots continue to rotate to the normal computed climb angle.
No doubt, the elongated versions of the B777 will also have a maximum pitch-up angle during rotation, that is not determined by performance calculations, but by the initial risk of a tail strike.
Yes, it seems logical that the weight of the aircraft may affect the “feel” of the controls when rotating, although this does not really make sense.
The B777 has conventional cockpit controls, but does the 777 have a fly-by-sire control system? This would take care of at least part of the difference in the force required by the crew when rotating.
But I can also imagine that the centre of gravity, aft or forward, may also affect the behaviour of the aircraft.
Modern instruments are very accurate and it is easy to read the nose angle during rotation on the flight director.
I may be behind the curve with up-to-date knowledge. My last flight was in the dim past, now nearly 16 years ago.
So how this crew could get it so wrong is a bit of a mystery.
Most likely explanation: Wrong weight data entered in the computer. Maybe even a discrepancy between the data the crew used for their calculations, and the real figure?
Modern engines have a tremendous amount of power, and a corresponding excess.
Airliners can continue take-off after an engine failure at V1.
So even if the Vee-speeds have been miscalculated, and the aircraft rotates prematurely, as long as both engines deliver full take-off power it probably can muscle its way into the sky.
But in such a case a tail strike may well be inevitable.
Guys and gals, I have been speculating throughout my comment.
So I may well be completely off course. Of course !
I looked up how an actual tail dragger (an aircraft with a wheel in the back) takes off. Obviously, they rotate the other way, so with some models, there’s actually a danger of having a prop strike while rotating. Try to recover from that!
That said, while tail draggers often lift the back end off the ground before becoming airborne, not all of them do. The counterpart to the 3-point-landing is the tail-dragger’s 3-point-take-off!
Well Mendel,
You are talking about a tail dragger.
And I have plenty of time on those babies: Piper Cub, Super Cub, Cessna 180, Tiger Moth, Stampe SV4, Boeing Stearman. Probably over 4000 hours. On tail draggers alone.
Some of those airplanes may have enough power to gain speed and lift off with the tail still on the deck.
But in general, as soon as the airspeed is sufficient for the control surfaces to be effective, the pilot will raise the tail to allow more speed to build up and fly away.
A prop strike is not very likely, unless the pilot is really very incompetent. Or inexperienced.
It is a possibility if the pilot makes a “wheel landing”: Normally, just before touch-down the pilot will have closed the power and hold the aircraft off the ground, gently allowing the speed to bleed off until it nearly stalls and sinks gently to the ground with all three wheels.
Light “tail draggers” are normally landed like this, unless weather conditions, e.g. strong wind or crosswind, dictate a “wheeler”.
Heavier tailwheel aircraft are normally always doing a wheel landing, e.g. Beechcraft D18, Douglas DC3.
A wheel landing means that the aircraft is gently brought to touch-down at a low flying speed, so not in a near-stalled condition.
The advantage is of course that the pilot retains full control authority and can make corrections during roll-out..
The disadvantage is that on touch-down the controls are brought gently forward to keep the aircraft on the ground. Some less experienced pilots overdo this, and bring the nose a bit too forcefully down.
A twin can take it, but in a single-engine tail dragger the prop may hit the ground if the pilot pushes the stick a bit too far forward.
In all cases, in a crosswind the aircraft may make a ground loop.
Especially (very) light airplanes: the tail fin acts as a weather cock, with most of the ‘plane (and its weight) being relatively far aft of the wheels. Once the aircraft comes to taxy speed, the tail may swing and the nose wants to point into the wind,
Sometimes even experienced pilots can not prevent a ground loop.
In a crosswind, the rule used to be to land on the downwind side of the runway. This would give the pilot some free tarmac in a ground loop.
I have on at least two occasions landed across the runway. Ground staff were alerted, I would make a near-vertical landing and the assistants would grab the tail and wingtips.
On one occasion, actually it was at Schiphol, the mechanics had not yet arrived. The wind was strong enough for me to “hover” the Super Cub and move sideways over the taxy way.
The controller told me “(call sign) your landing time was …”.
I responded “I am still airborne”.
The controller angrily told me to land immediately and hold position.
All well and good, but the wind was so strong that I had to keep a lot of power on to prevent me from being blown backwards.
So I maintained the hover until the mechanics arrived.
The reason for this flight: the aircraft was owned by a company called Reclamair, then a subsidiary of the air charter company Martinair.
As the name suggests, the Super Cubs were mainly used for aerial advertising. Which happened to be my first paid flying job.
On average I flew between 700 and 1100 hours a year in those aircraft.
So I was extremely experienced on the Super Cubs.
Some of the inspections of the Super Cubs were carried out in the Martinair hangar at Schiphol. And for a positioning flight under less than marginal conditions it fell to the most experienced pilots to do the job.
Yes, in those days rules were nowhere nearly as rigidly adhered to !
Caveat: I got away with a lot of stupid things, I can admit to them now but I do not recommend that any of the readers here try them.
Landing across the runway would be called a “short field landing” nowadays. Sylvia has blogged about the STOL competition at Valdez before. I expect you could’ve done well there!
The anecdote I found is this:
Source: https://aviation.stackexchange.com/questions/35660/how-does-a-taildragger-take-off-does-it-rotate
Mendel,
Thank for this information.
Some aircraft have been built especially for a (very) short field take-off and landing capability.
Famous, of course, was the WW2 Fieseler Storch, that managed to land on the roof of a castle to snatch Mussolini from captivity and bring him to Germany, from where he was reinstated as the Italian “Duce”.
The Maule is a more modern aircraft with extreme short-field abilities.
I have never flown this type, but apparently the engine, in combination with an oversized prop, is able to accelerate to flying speed in a three-point attitude in less than 100 metres.
I also remember that we were doing some banner towing flights from Bremerhaven in Germany.
A small airport with a paved runway.
It was very close to the coast, a very strong wind was blowing directly across the runway. But there were no obstacles to disturb the flow of the wind, so with ground assistance we brought the aircraft to the runway. We took off across, with maybe 5 metres of forward ground roll. Virtually vertically.
The normal pick-up was impossible: flying with a grapnel behind the aircraft, to try and catch a loop attached to the banner tow line.
The solution was simple: “Hover” low enough for the ground assistant to grab the grapnel hook, put the loop in it and signal to move forward and climb. Only possible in a very steady wind, without turbulence.
Sometimes, even from our home base Essen-Muelheim (EDLE), the wind might on occasion be so strong that we flew half an hour (or more) in one direction, and a 180 degree turn brought us back to the starting point in just one or two minutes.
Dropping the banner was another tricky one: normally we would fly at about 150 feet over the zone assigned to banner operations, and pull the release. But in strong wind that could mean that the banner would be picked up by the wind and blown over the fence.
So in such a case, we would approach a bit higher, with full power, and dive to the dropping point. That would ensure that the banner would be behind, not below the aircraft and even have a forward momentum.
We would release about 50 feet above the ground and pull up.
In those circumstances, taxying to the holding point, or vacating the runway, was risky.
Normally, in a taildragger, the stick is held back during the taxy.
But in a strong tailwind, the opposite is necessary: The stick must be pushed full forward to hold the tail down. Otherwise the wind can flip the aircraft on its nose. Turning to, or from the runway required a coordinated reversal of the forward-to-backward stick, as well as bringing the stick into the wind, now with the wind from the side. Otherwise the wind might have blown the aircraft on its opposite (downwind) wing tip.
It has happened more than once. To other pilots, it never happened to me. If I was not sure that the wind would not catch the tail, I asked for ground assistance. My colleagues derogatorily gave me the nickname “Rudy Rollhilfe” (Rudy Ground Assistance), but they stopped laughing once they themselves had been caught out. The damage usually involved a bent propeller and a shock-load check of the engine.
But that often involved no more than only a ground check by the engineers.
Sometimes we would fly 40 to 50 hour A WEEK.
Or 700 – 850 hour in one season (March to October).
I was one of the small number of pilots that remained over the winter, so I probably accumulated more than 1000 hours in the first year after getting my CPL. All VFR, mostly in PA 18 Super Cubs. In all kinds of weather, even snow, low visibility and strong wind.
Foolish? I admit: yes.
Many incidents, but there were no fatalities. I don’t even recall injuries.
The company owned about 30 Super Cubs.
Usually 21 of them would be in the air, on a daily basis.
This sort of experience would of course be useless to any kind of professional airline operator, but we were undoubtedly very good “stick-and-rudder” pilots.
In the present days of automation probably a dwindling skill set.
Oh, I forgot:
In those conditions of (very) strong wind we would not make 3-point landings, but always “wheel landings”.