Pneumatic Pressure Required
The flight crew reported for duty at Bournemouth Airport at 3am on Friday the 7th of May 2004. They were flying a thirty-three-year-old Fokker F27 Mark 500, registered in the UK as G-CEXG, to the island of Jersey and back.
The Fokker F27 Friendship was designed as a successor to the DC-3, which had been popular with KLM and other commercial operators after the war. Although a total of 787 Fokker F27 Friendships were produced between 1955 and 1987, by 2004, they were becoming a rare sight and by 2009, only 82 F27s were still in service. These days, you are more likely to see the aircraft on display at a museum rather than flying.
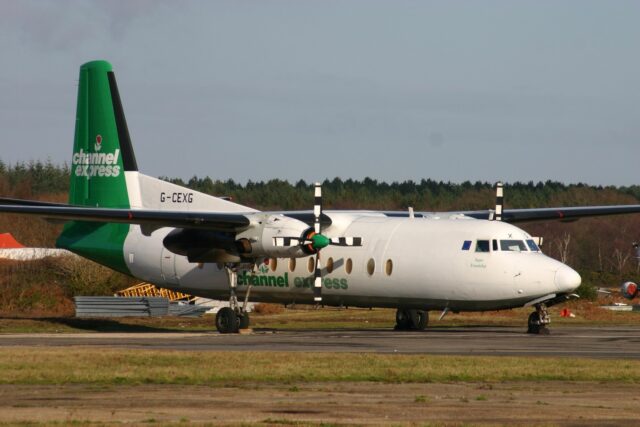
As the flight crew walked up to the F27, they saw engineers charging the aircraft’s pneumatic system. Surprised, the captain asked what they were doing, as this was not normal procedure and they did not know of any issues with the aircraft.
At the same time, the first officer entered the cockpit and spoke to the engineer there. He asked if there was a pneumatic leak. The engineer said no, there was no leak.
The engineers outside explained to the captain that there had been pneumatic problems on another aircraft, and so the operator had decided to charge the pneumatic systems on the entire fleet.
Typically, aircraft use hydraulics, using pressurised liquids, but the F27 uses pneumatics as more economical to maintain. At the heart of a pneumatic system is a pressure or vacuum-creating engine-driven air pump.
The F27 has two pneumatic systems: the main system and the emergency system. Pneumatic systems provide fluid power using pressurised air or gases. These are charged using compressors driven by the engines.
The main pneumatic system supplies the pressure that operates the landing gear, the nose-wheel steering and the wheel brakes. The emergency system supplies pressure to the alternate landing gear extension and the emergency wheel brakes, ensuring that if the main system fails, it is still possible to drop the landing gear and stop the aircraft.
The aircraft also carries compressed air in storage bottles with check valves. If there is an interruption in the supply from the engine compressors, the system charges from the compressed air supply.
Back in the cockpit, the first officer noticed that the brake bottle pressure was slightly low and remained concerned that there was an issue with the pneumatic system. He pulled out the pneumatic isolating valve pin.
The pneumatic isolating valve is used in the case of a pneumatic leak. The valve (actually, two valves operated by a single control rod) isolates the main system and the main system storage bottle. The idea is that you don’t want to let the pressure bleed out, so by isolating the main system, you preserve the remaining pressure until you need it.
Once the main system is isolated through pulling the pin, the other parts of the pneumatic system are cut off. Specifically, the landing gear, the nose-wheel steering and the wheel brakes cannot be operated from the main system supply once the main system is isolated.
If there was a leak, it was a good idea to isolate the system while doing the checklists and start-up, saving the pressure for when they needed it. The first officer was stopping the bleeding so that they would have enough pressure left when they needed it. If there wasn’t a leak, then theoretically, it would do no harm to isolate the system until they were ready to move.
The captain entered the cockpit. The first officer showed him that the brake bottle pressure was slightly low.
Here’s where it gets weird: He didn’t mention that he’d pulled out the pneumatic isolating valve pin.
The captain started the engines and the two pilots began the AFTER START checklist. Checklists like this are high-level documents. There is no room and no need to explain every detail, instead the checklist is a summary of the actual check required, where the Operations Manual gives the full checks needed. So for example, in the F27 AFTER-START checklist, it says
Pneumatics….Checked.
The Operation Manual expands this:
- Check all 3 pneumatic gauges
Minimum pressures for take-off: Brake: 1500, Main: 1500, Emergency: 2500
Confirm the pneumatic isolating valve is IN. Both pneumatic low-pressure warning lights should be out.
It is the captain’s responsibility to start the engines. Then the first officer reads out the AFTER START checklist and the captain responds to each item.
The captain agreed that pneumatics had been checked, without noticing that the pneumatic isolating value was pulled out. The first officer knew it was pulled out, but did not push it back in or mention that he’d pulled it out.
As they began to taxi to the runway, both the captain and the first officer noted that the pneumatic pressures were abnormally low but they agreed that they were still within limits, as in every case, the pressure showed as still in the green “acceptable” band.
It’s hard to imagine what the first officer was thinking, other than that he completely forgot what he had done, despite having a conversation with the captain about the low pressure as they moved from parking to the taxiway. This is utterly perplexing to me, having taken the action directly as the brake bottle pressure was slightly low. Pulling the pin likely contributed to the continued low pressures they saw, but still he did not consider his action or think to mention it.
Suddenly, the F27 veered hard to the left. The captain steered full right and applied right brake. It didn’t help. The F27 was running straight off the taxiway.
With his left hand on the steering, trying desperately to straighten the aircraft, the captain didn’t dare let go to reach for the emergency brake. This was an understandable split-second decision but ultimately the wrong one, as the emergency brake was fed by the emergency pneumatic system, which was still working. He had no way to know it, but that was the only braking he still had.
The wheel brakes did nothing. Steering did nothing.
No doubt completely bewildered by completely losing control of his aircraft which was now careening off the taxiway, the captain suddenly spotted the pulled out pin. With his right hand, he quickly pushed it back in. It was too late.
They drove off of the runway and bounced over the grass. The F27 bumped along for another 50 metres (165 feet) and finally came to a halt.
The captain shut down the engines and then called for engineering assistance. At the same time, air traffic control called emergency services to report an aircraft stopped on the grass.
The nose gear of the F27 was so damaged that even when they restarted the engines, it was not possible to taxi forward or even to tow it by the nose back onto the runway. Instead, they had to drag the aircraft tail first off of the grass and back to the hangers.
How can we explain such an elementary mistake?
The flight crew had not expected any servicing of the pneumatic systems. The investigation confirmed that they were right to question what the engineers were doing and to be concerned about the integrity of the aircraft’s pneumatic system. The entire issue might have been avoided if the flight crew had been given advance notice that the entire fleet was having their pneumatic systems charged by the engineers overnight.
The engineers outside of the aircraft had explained to the captain why they were charging the system; however, the first officer was in the cockpit and likely did not hear why the system was being charged. When he saw the low charge for the brake bottle pressure, he became concerned. He decided to isolate the main pneumatic supply and storage bottle in case his suspicions were right and there was a leak in the system.
This decision should have been communicated. To my mind, the biggest failure here is that the first officer said nothing of his action and never thought to push the pin back in when they taxied from parking.
However, the final cause of the accident must rest with the captain. After the captain started the engines, he was responsible for confirming each item on the AFTER START checklist. When it came to checking the pneumatics, he clearly expected the pneumatic isolating valve would be IN and he did not check that this was actually the case. Not until they were driving straight off of the taxiway did the captain realise that the pin was OUT. As a result, he lost pneumatics leading to the failure of the nose-wheel steering and wheel brakes. He couldn’t keep the aircraft on the taxiway without them.
The incident details were published as a part of AAIB Bulletin No: 10/2004.
It would have been nice to hear from the first officer whether he had forgotten that he’d pulled out the pin or simply didn’t understand the effects that isolating the main system would have.
The operator changed the checklist as a response to this accident, expanding the initial item to check pneumatics into two: check the pneumatics AND confirm that the isolating valve pin is pushed in. The AAIB recommended to the Civil Aviation Authority and to the manufacturer of the F27 that other operators of the F27 be alerted to this checklist change.
A strange one for a few reasons:
As Sylvia mentions, the Fokker F27 had a pneumatic system for the operation of essential services, such as braking, landing gear operation and nosewheel steering.
The philosophy behind this was simplicity and weight saving.
A hydraulic system needs return lines, but the compressed air, after doing its work, would be released into the atmosphere. A small leak would not be a great problem because the compressors would constantly replenish it. And there was no need for a hydraulic reservoir nor for return lines.
But air can more easily leak away than a fluid. In my time, it was standard practice to pull the isolating valve when parked. This ensured that there would be a reserve of air available. But after a prolonged parking time, the pneumatic pressure might have dropped, explaining the engineers recharging the system.
It was difficult to miss the valve: it was located in the cockpit entry, behind the captain’s seat and when pulled (isolated position) it presented a very visible shiny metal pin sticking out horizontally; difficult to miss as it would partially obstruct the entrance to the cockpit.
As the gear operation was pneumatic, there were safety clamps on the operating struts, They were locking over-centre to prevent accidental gear retraction on the ground if the pneumatic pressure would be low. With the high wing lay-out they were easily seen. The pre-flight walk-around included a check of the pneumatic pressures. The isolating valve, especially on the first flight of the day, would have been pulled so, before removing the gear locks it would be pushed in to ensure that the emergency accumulator air bottles would prop up the system pressure, including the gear.
Here is where I cannot really understand how things went wrong. When taxying, of course we used the nosewheel steering and the brakes. At busy airports this could cause a loss of pressure and we would watch it constantly. It could require us to delay take-off and stop at a convenient location – usually a holding point – to rev up the engines in order to build up pressure to the required minimum. Don’t forget that if the pressure was insufficient, in case of a rejected take-off we might run out of brakes and runway or, if an engine failed after take-off we might not have been able to raise the gear. Which with a fully loaded aircraft could make the difference between a safe return to the runway, or an unavoidable crash due to the extra drag.
I cannot see anything wrong with the engineers charging the pneumatic pressure before departure. It sounds like good practice to me.
A fluid, hydraulic fluid in most aircraft, cannot be compressed but air can. This led to a peculiarity of the system: Especially when applying the brakes after landing, there was a “lag” before they started to “bite”. Pilots new to the F27 could be seen swerving a bit from left to right, with audible hisses from the brakes as air was released. It never led to a problem, apart from a bit of rd face and sweat. All got the hang of it soon enough.
I was hoping you would weigh in, as I know you spent a lot a lot of time in the F27. I still find it hard to believe that neither noticed.
Oh I spotted a small typo: the caption under the photo calls it a “Fooker”. The name “Fokker” means. Breeder.
Nothing to embarrass the parish priest!
Oh noooo. Fixed.
Whereas Fooker in Ireland could cause some issues :D
Exactly Sylvia. Do you have Irish roots?
It’s all about the context. For example, asking “where’s the crack?” would get you quite different results in Dublin and Los Angeles.
Yes, although here it’s spelled “craic”.
Oh, btw: When I mentio0ned the pneumatic pressure accumulator, I described the “pin” that would be pulled to close the bottle and preserve emergency pressure.
I should have called it a “rod”. I never measured it, but from memory I guess that it would have intruded into the cockpit access by about 20 cm.
It could have been missed if it was pulled after the crew had taken their seats. But during taxi it was important to monitor the pressure constantly6 – see my original comment.
The F27 was still a very reliable workhorse when I flew it. In widespread use as a cargo aircraft, they were in use with quite a few “feeder” cargo operators. I flew the F27 until 2003. At night a small runway at Cologne Airport would be closed to park the smaller cargo aircraft, in use as feeders for UPS. Although more recent models came into use, like modified ATP and ATR as well as Bandeirante and Shorts 3-60, the majority still were F 27.
Most feeder flights were at night. The Rolls-Royce Dart engines were emitting a very high pitched, loud whining and penetrating sound. In order to meet noise regulations, a small modification was implemented: The noise was mainly caused by the radial flow compressor. By extending the air intake nacelle forward, until just behind the propeller axis, the noise was reduced considerably.
Even so, after about 4500 hours on F27 and its derivate Fairchild FH227 I have a permanent hearing loss in the higher-pitch sound spectrum.
But what eventually sealed its fate was the availability of parts. The hot section of the Dart engines was no longer available. Damage was repaired by welding, a highly specialised, critical and increasingly expensive operation that eventually was no longer an option.
For hot and high operations we used a water-methanol injection system that inevitably put more strain on the turbine section.
But to the credit of the maintenance staff, the aircraft were still eminently reliable when I flew them. But of course, the older staff with the experience on these older aircraft were retiring, and, understandably, younger mechanics were not interested in a career in old, soon phased out technology.
The FH227 was phased out before the F27, but eventually their time was up.
After the “Fooker” ;- I spent my remaining years on Citations: 500, 550, 650 and Stallion.
Outside of the scope of this blog, as an “hors d’oeuvre” about the F27s Dart engines and our Middle East ops::
The parts of the hot section that were welded as part of an overhaul were of course the “burner cans”, not the turbines. Insofar as I remember, the engineers already then were remarking that the supply was running out as the welding could not be done indefinitely.
But the turbines were also put under extra strain. The company that I flew for had a contract in the Middle East, to fly newspapers from Bahrain to Riyadh and Jeddah. The capacity was 6500 kg. Paper is heavy, it did not take a lot of space.
The aircraft were mainly converted into MK-600 from passenger operations. Interior stripped, a cargo door and reinforced floor with rai8ls where retaining rings could be fitted installed. The galley and toilet had also been removed. These had been in the aft section, behind the passenger entrance door. The cargo door was in the front, behind the cockpit. This had required fitting of a reinforced surround and motor to operate it. Meaning that the centre of gravity had shifted substantially forward. And so, the weight and balance of the aircraft demanded that there would be 500 kg in the rear section. If flying without cargo, that meant carrying 500 kg ballast.
The contract required carrying the maximum payload of 6300 kg. After offloading the last newspapers in Jeddah, we would fly empty back to Bahrain. For that purpose, we uploaded sandbags.
Logical, you’d say. In the desert there is no lack of sand.
But there were problems: We had to upload the sand in Jeddah. Sandbags are very heavy and the loaders were only contracted to handle the cargo, the newspapers.
We had to dump the sand in Bahrain, and upload it in Jeddah. We carried empty bags. But eventually the bags got damaged, sand spilled out. It became very messy. And the engineers did not like it as it went through the gaps into the belly of the aircraft.
A new system was used: drums of water. As I mentioned, the cargo itself did not occupy even 1/4 of the space, so carrying five empty 100 litre drums was no problem.
After offloading the last load in Jeddah, a tanker arrived to fill the drums now tied in the tail section. This worked very well for us, but the locals did not like it one bit when we dumped 500 litres of water into the desert at Bahrain after every flight.
Now, mas we know, it can be very warm in the area during the summer. months. The temperature may not drop below 37 degrees C AT NIGHT ! When I was there, one year the average temperature over July and August was over 41 degrees. Average over the entire period. Daytime temperatures were in the range of 47 to 53, at night as mentioned around 37. at 03:00 AM ! With those daytime temperatures we would have been very restricted in our weight carrying capacity. Even with the cargo door wide open it was very hot in the cockpit.
Under those conditions, even at night, we needed to boost the engine power. This was accomplished by spraying a mixture of water and methanol in the hot section, the turbines, during take-off. This increased the take-off power very considerably. Not only did the liquid evaporate and turn into steam, which of course increased the volume of gas driving the turbines, but it also had a cooling effect which actually allowed more fuel to be sprayed into the engines. When selected ON, the water-meth injection started at a certain power setting. We kept it going until we had reached a safe height, in this case 3000 feet when we would select it OFF. The loss of power was dramatic. We would climb very slowly to a cruising altitude of around FL 080. One “fill” would be enough for about 3 wet take-offs, so thye w/m reservoirs had to be topped up regularly.
That led to another problem: Bahrain is a Muslim country and the Islam forbids the consumption of alcohol. Water was no problem, but in order to prepare the mi9xture a special government permit was required for the importation of barrels of methylated spirits. Although ethanol is the spirit normally used for consumption, albeit not raw butt in the proper concentration, methyl is also alcohol.
And although this permit was normally granted, it made the mixture expensive. And so we devised a W/M saving method.
To calculate our take-off, runway length, speeds, etc., we used so-called TL tables, also know as RTOW (regulated take-off weight) tables. Which came prepared for e3very runway. It also indicated if an intersection take-off was permitted.
Although our take-offs were critical, the runways in those hot countries are very long. And normally we were allowed to use an intersection, even at maximum weight.
And so we would start from the beginning. We would apply power, not at full take-off setting but, just below the setting where the water-meth valves would open. Starting our roll, we would set full take-off power when passing the intersection from where we would be allowed to start, or at 60 kts (whatever came first). So we would already have gathered a substantial speed before the water-meth injection took place, saving a lot of the precious liquid without breaking any rule.
At 3000 feet we would select W/M off.
OK, for you aviation buffs this was as a kind of “encore”.
The F27 was a nice aircraft to fly, although with that large tailfin it was a b… to handle in strong crosswinds.
I once landed a Shorts 3-60 in a crosswind of over 40 kts. Not in the book, but I doubt that the F27 could have done it.
I marveled at the oversize tail fin as well. I’m guessing it was required to support one-engine-out operations?
Are the F27 engines started with an electric motor, or does that use the pneumatic system as well?
Fun fact: methylated spirits in Australia is just ethanol with a nasty taste added to reduce drinking; the whole point of the methanol was to make it undrinkable, but people drank it anyway and methanol Is incredibly dangerous, so it was eliminated.
Not sure if that is the case elsewhere (and I still won’t have a meths and Coke thanks!), but would probably be a big issue in the gulf states where prohibition seems to result in people drinking anything alcoholic