Overrun in Ireland
On the 19th of February 2023, a private pilot arranged to meet with a flight instructor at Birr Airfield to fly a Cessna 172 Skyhawk.
That morning, the flight instructor arrived early. He was rostered to do a local flight with a new club member. He held his commercial licence but was presumably new to instruction, having just 296 hours, of which 131 hours were on type. He had 15 hours flight time in the previous 90 days. Before that day, he’d spent about twenty hours in the accident aircraft, a Reims F172N (a variant of the Cessna 172 built in France under licence) registered in Ireland as EI-GWU. The Reims F172N was powered by a Lycoming O-320-H2AD piston engine driving a two-bladed fixed-pitch propeller.
Birr Airfield (EIBR) is a private airfield near the town of Birr in Co. Offaly, Ireland; about 80 kilometres from the better known Shannon Airport and in the Shannon flight information region. Birr Airfield has just one runway, a grass strip of 570 metres (1,870 feet) running north-south.
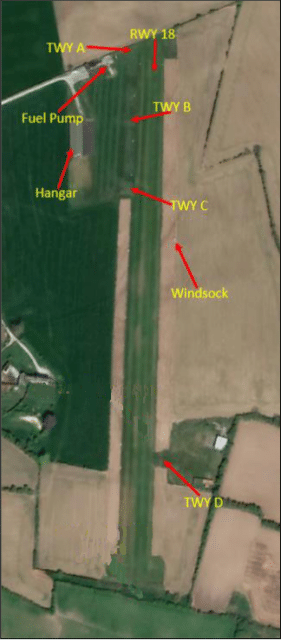
The nearby airfields are Gay Tracy Airstrip, Camus Airstrip, Borris-in-Ossory Airstrip, Pallas West Airstrip and The Forge Airstrip, and if those names don’t make you want to go flying around the local area, then there’s no hope for you. Birr Airfield is the home of a flying club which has been operating the airfield for over 30 years. The club is a registered training facility with a membership of pilots, students and enthusiasts.
It was a typically damp Irish morning. The skies were overcast with a moderate wind but visibility was good.
Condition | Details |
---|---|
Meteorological Situation | Ireland lies in a strengthening south-westerly airflow between an anticyclone to the south and a depression centred south-west of Iceland. |
Surface Wind | South-west 7-12 knots (kt). |
Wind at 2,000 feet (ft) | West to south-west 25-30 kt. |
Surface to 300 ft | West to south-west 10-20 kt. |
Visibility | 40 + kilometres (km). |
Weather | Cloudy with patchy rain and drizzle. |
Cloud | Overcast with cloud bases between 1,000-1,500 ft. |
Surface Temperature/Dew Point | 9/7 degrees Celsius. |
Mean Sea Level (MSL) Pressure | 1,028 Hectopascals (hPa). |
Freezing Level | 8,000 ft. |
The instructor walked the full length of the grass strip, knowing that his flight would be the first flight of the day. The runway was firm, although he noticed that his shoes were wet after the inspection. He went to the hangar and did a pre-flight walkaround of the 172, including checking the fuel. Satisfied, he pulled the 172 out of the hangar and started the engine. He taxied the aircraft to the fuel pump, testing the brakes on the way.
The new club member arrived at the airfield and saw the 172 at the fuel pump. Once the instructor had turned the engine off, he walked over to introduce himself. He was a qualified pilot with 187 hours of flight time, though less than six hours in the last 90 days. He had never flown a Cessna 172 of any variant before, which is why he had booked the flight with the instructor.
The instructor briefed the pilot on the training objectives for the session. He planned for them to fly to the local training area and practise general handling and then return to Birr for circuits, following the airfield’s pattern to practice take-offs and landings.
Once their aircraft was refuelled, the instructor checked the fuel again and had the student pilot complete another pre-flight walkaround.
The pilot climbed into the 172 and sat in the left-hand seat with his shoulder harness on. The instructor sat in the right seat and put on his lap belt but not the harness. He briefed the pilot on the cockpit instruments and best speeds for take-off, climb and glide.
They started the engine and verified that all of the temperatures and pressures were normal before taxying to the runway, stopping along the way to do their power checks.
The pilot had a laminated checklist which he followed. He remembered that he had applied carburettor heat for about three or four seconds. While the carb heat was on, he saw the engine speed drop by about 100 RPM, as expected. The instructor also remembers checking to see that the carb heat control was turned off. The pilot extended the flaps to 10° for take off.
The instructor ran through a Threat and Error Management briefing, covering the actions that the pilot or instructor would take in the event of an abandoned take-off or engine failure, including the process for emergency evacuation. Then they taxied to the start of runway 18, as the instructor wanted to use the full runway for the departure. “The more we have, the better.”
The pilot taxied to the holding point, checked the skies for any approaching aircraft, and lined up on the runway. They were finally good to go.
The pilot applied some aileron to compensate for the crosswind and then applied full power.
They accelerated along the runway. As the grass was wet, the instructor expected the take-off run to be a bit longer than usual. But as they passed the wind sock, situated about halfway along the runway, he became alarmed. They should have been in the air by now. He checked the tachometer which showed between 2,000 and 2,100 RPM (revolutions per minute). The airspeed was between 50 and 55 knots and was not increasing. They didn’t have enough power to take off.
The pilot confirmed that the throttle was fully open (Scotty voice: “I’m giving her all she’s got!”). He too, was realising that they weren’t going to get airborne. The instructor called out to abandon the take-off.
The Pilot Operating Handbook emergency procedure for an engine failure during the take-off run reads as follows:
- Throttle—IDLE
- Brakes—APPLY
- Wing Flaps—RETRACT
- Mixture—IDLE CUT-OFF
- Ignition Switch—OFF
- Master Switch—OFF
This serves as the emergency procedure for an abandoned take-off: you don’t need to confirm that the engine has fully failed before using it.
The pilot immediately closed the throttle, reducing the engine power to idle. The instructor pulled the mixture control, cutting off the fuel supply. Both pilots applied the brakes as they sped towards the end of the runway.
The 172 skidded on the wet grass. It finally started to slow but not in time. They ran out of runway and hurtled over the rough ground before crashing into the boundary hedge.
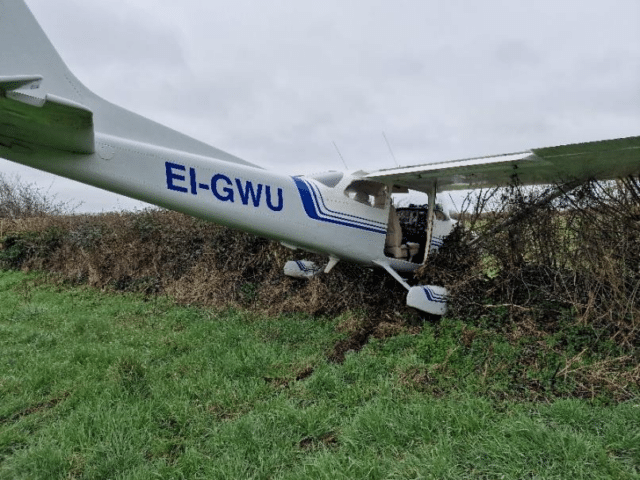
If you look at the photograph of the crash site above, you may notice the flaps are still extended for take-off.
They evacuated the aircraft and phoned the Chief Flying Instructor before taking photographs of the aircraft in the position. Another person rushed over to help. That person had been watching them and asked if they’d had a problem before they left, as it seemed to take a long time before they started the take-off roll.
They hadn’t. Everything had seemed fine during the taxi and the power checks. But now, the aircraft was in a hedge. The pilot explained that they’d suffered a partial power failure on take-off.
The aircraft’s propeller spinner was deformed with scuffing on the propeller. The engine cowling and lower section of the exhaust were damaged. The nose wheel spat had “partially disintegrated”.
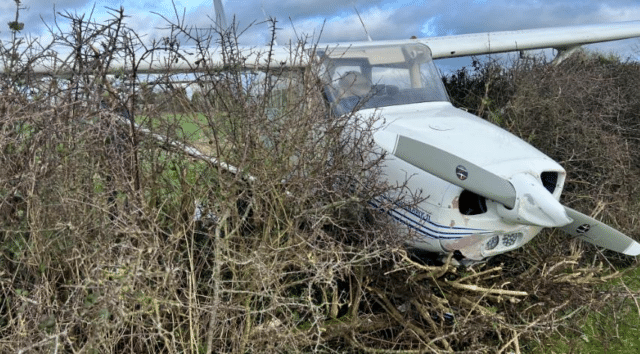
The instructor was sure that the fuel was clear, he’d taken two samples from the aircraft and one directly from the fuel pump. The student had never flown this aircraft type before but the brake system was similar to what he’d flown before.
They recovered the aircraft from the hedge and the Air Accident Investigation Unit Ireland (AAIU) was informed. Under the instruction of the AAIU, with a club official overseeing, a maintenance engineer started up the engine.
The engine started up normally with no sign of rough running. The engineer increased the power and checked the magnetos and the carburettor heat. All was normal. The engineer then applied full power, increasing the RPM to 2,300, before pulling the power back to idle at 650 RPM. All temperatures and pressures were in their normal ranges. The engineer could not find any fault with the engine.
The report quotes the UK Civil Aviation Authority Safety Sense Leaflet No. 14: Piston Engine Icing, last updated in June 2023.
The most common type of piston engine icing is carburettor icing, often referred to as ‘carb icing’. It affects aircraft in which the fuel and air mixture is delivered to the engine via a carburettor.
When the fuel evaporates and the pressure reduces, the temperature inside the carburettor can drop as much as 35°C (63°F) below the ambient temperature. As a result, water vapour in the air freezes, forming ice in the carburettor. The important point is that it doesn’t need to be cold out for carburettor ice to form; much more of an issue is the humidity.
As the ice forms, it quickly starts to choke the engine’s air supply, as if the engine were trying to breathe through a straw that’s getting smaller and smaller.
The engine starts losing power, but the effect is so gradual that it often doesn’t get noticed until a large amount of ice has formed.
To combat this, the carburettor heat is turned on for at least 15 seconds during the engine power checks. The engine power will drop a bit while the heat is on and then recover when the heat is turned off. If the engine power recovers to a higher RPM than before the carb heat was applied, then it is likely that ice had formed and further checks should be carried out until the ice has cleared.
If there is a delay between conducting the engine power checks and taking off, ice can form and build up again. In this case, the pilot should turn the carburettor heat on again for about 15 seconds before applying full power. In icing conditions, such as that day at Birr, the engine should be taken to a high power setting several times to clear any ice and confirm that take-off power is available.
Both the pilot and the instructor confirmed, after the accident, that they were aware of the issues of carburettor icing. The instructor said that he had checked the weather situation that day using the Met Éireann Self Briefing System and that he was mindful of the relationship between relative humidity and the potential formation of carburettor icing.
On that February day, the temperature was 9°C and the dew point was 7°C, marked on the carburettor icing chart with a red dot.
The temperature and dew point so close together showed perfect conditions for ice to form on the super-cooled inside of the carburettor. Normally, a pilot should notice the early signs of carb icing during the power checks. This should have come up during the power checks. However, the pilot said that he’d only left the carb heat on for “three or four seconds,” and checked to see if the RPMs fell, but did not check what they recovered to. The instructor only recalled that he glanced at the heat to ensure it was turned off after the check. Neither pilot seemed to have paid attention to the effects of the carb heat. If they had, they may have noticed that ice was accumulating in the carburettor.
Even if they had left the carb heat on for fifteen seconds and melted all the ice, this would have been undone while they sat idle at the start of the runway, discussing threats and emergencies. At the end of the briefing, the instructor should have instructed the student pilot to reapply the carb heat (and this time, watched the RPM!). Instead, he allowed the student to pull onto the runway and apply full power for take-off, thus effectively creating a dangerous situation.
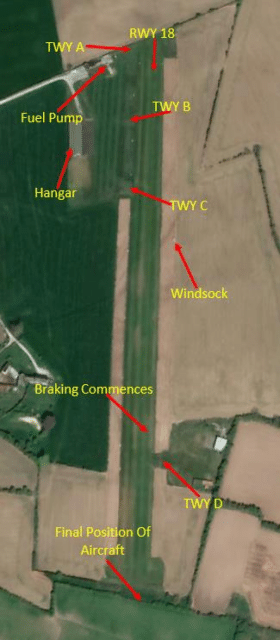
Birr Airfield, including the start point and the point at which the 172’s brakes were applied.
Investigators inspected the runway which showed that the two pilots did not apply the brakes until very late in the take-off run. The flaps had been extended for the take-off, in order to increase lift. When performing an emergency stop, the flaps should be fully retracted, to increase the weight on the wheels and allowing for better braking action. Leaving the flaps extended increased the stopping distance that the 172 required. In combination with the wet grass of the runway, there was really no way they were ever going to stop before running off the end.
You can read the full report on the website of the Air Accident Investigation Unit Ireland.
I’m particularly flummoxed at the instructor, who I would expect to be focused on ensuring that the pilot did not make any stupid mistakes. The instructor should have insisted that the carb heat was applied correctly during the engine checks and then again before applying full power. He should have been watching the power and speed during the take-off run, a critical phase of flight. He noticed too late that they didn’t have enough power to take off from the wet grass, and when he did realise, he should have noticed that the flaps were still extended after he pulled the mixture control. And finally, his decision not to wear a shoulder harness set a poor example, but that’s just me being grumpy now.
Still, a very graphic lesson in carb icing and how it can occur. The Reims F172N was last seen landing at Abbeyshrule on the 15th of September this year, so I think it is safe to say it made a full recovery.
I was curious what causes the RPM drop when applying heat, and found that the Wikipedia page on “Carburetor heat” is quite detailed.
I also learned that Sylvia spells it “carburettor” because this is a British aircraft. (Aussie planes have a carbie installed, of course.)
Theoretically, Fear of Landing (and all my aviation writing) is in British English, because most of my journalistic endeavours were in the UK and I did a UK PPL, and Cliff would only proof stuff in BE because he got sick of me switching all the time. The main thing was for it to be consistent. But now that it isn’t proofed at all (well, other than by you all), I think it is a lot less consistent.
Switching by aircraft make is an interesting angle though! “That sooted-up carbie ended up looking like a barbie!” I could definitely get into this.
In that case, the Reims was registered in Ireland, but built in France with a carburateur. ;)
I suspect both the Irish and French would be annoyed by calling this a British aircraft.