Lion Air flight 610 and the AOA Disagree alert
I wrote before that Lion Air’s Boeing 737 had a faulty AOA sensor which was replaced the day before Lion Air flight 610. The new sensor was out of alignment by about 21°, one of the key factors leading to the uncommanded MCAS trim which caused the crash.
Under normal circumstances, this would have been flagged immediately by an AOA DISAGREE alert.
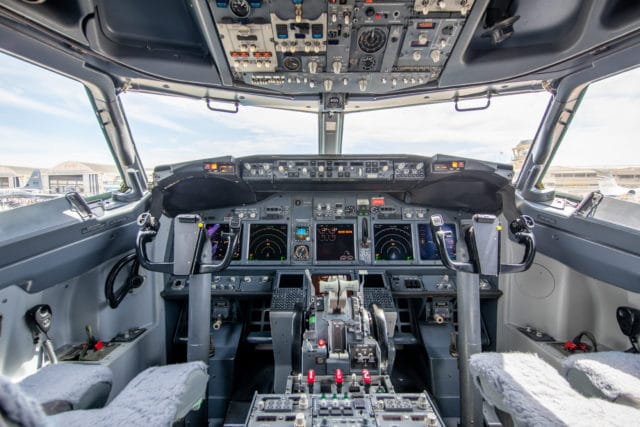
The FAA granted the 737 MAX aircraft an amended type certificate on the 8th of March 2017. The AOA DISAGREE ALERT was included as a standard cockpit feature. The Lion Air Flight Crew Operations Manual provided by Boeing in August 2018 gives the following information for an AOA DISAGREE alert.
Condition: The AOA DISAGREE alert indicates the left and right angle of attack vanes disagree.
1. Airspeed errors and the IAS DISAGREE alert may occur.
2. Altimeter errors and the ALT DISAGREE alert may occur.
We know that the accident aircraft showed IAS DISAGREE and ALT DISAGREE faults, which is a symptom of an AOA DISAGREE. However, no one ever reported an AOA DISAGREE alert. That’s because the AOA DISAGREE annunciator never lit.
My original understanding was that this fault alert was only available as a pay-for service, which seemed criminal. The truth is not that simple, although it remains a shocking failure.
In order to understand the situation better, I had to work my way through the Air Data Inertial Reference System (ADIRS).
The Air Data Inertial Reference System is a combination of functions which provides flight data to the flight management computers, the flight and engine controls, the flight deck display panels and any other system requiring inertial reference information and air data.
- Inertial reference information consists of position and attitude.
- Air data includes airspeed, angle of attack and altitude.
The functions of the Air Data System and the Inertial Reference are combined by the Air Data Inertial Reference System into a single device, which is the Air Data Inertial Reference Unit (ADIRU).
The ADIRU calculates basic air data information based on the information from the Air Data Module which interfaces with the pitot and static system. The Air Data Module is located in the pressurised cabin.
The ADIRU uses the Air Data Module information to calculate and pass parameters (including altitude, computed airspeed and true airspeed) to the aircraft systems. Important to us right now is that the ADIRU provides angle of attack information directly to the Flight Control Computers. This corrected angle of attack is used as an input to the MCAS function.
The Boeing 737 MAX has three pitot probes and six flush static ports. The Air Data Module connected to the captain’s pitot probe and static ports sends information to the left ADIRU, while the Air Data Module connected to the first officer’s pitot probe and static ports sends information to the right ADIRU. The standby air data instruments receive their data from the right-side auxiliary pitot probe and alternate static ports (first officer’s side).
The data from the ADIRU (and other aircraft systems) is processed by two Display Processing Computers (DPC 1 and DPC 2) so that the data can be displayed on the display units on the flight deck. In the case of a system failure, the data may be invalid. In this case, the Display Processing Computer and the Primary Flight Display shows an amber flag on the parameter instead of displaying the erroneous data. This is what we discussed in the maintenance section where the flight crew repeatedly reported the appearance of ALT and SPD flags on the captain’s Primary Flight Display.
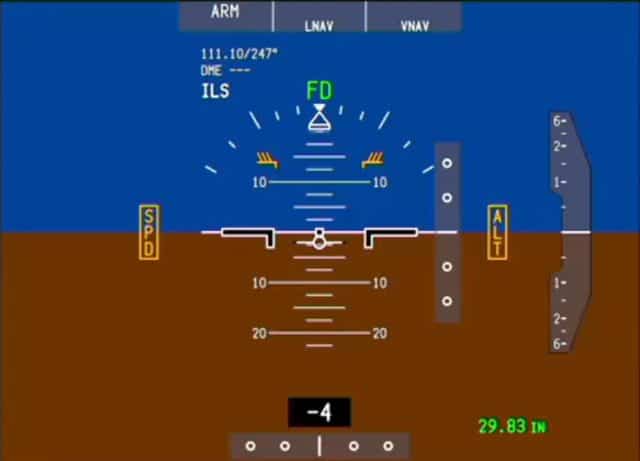
They also reported IAS DISAGREE and ALT DISAGREE messages. The two Display Processing Computers compare each other’s data and if the data is not similar, then a DISAGREE message is displayed on both Primary Flight Displays. The IAS DISAGREE message appears if the indicated airspeed differs by more than five knots for more than five seconds and the ALT DISAGREE message appears if the altitude is different by more than two hundred feet for more than five seconds.
Finally, the AIRSPEED LOW is an aural alert which warns the flight crew of a low air speed, as calculated by the Enhanced Ground Proximity Warning System (EGPWS) and the MAX Display System. The Pilot’s Flight Display shows a minimum manoeuvre speed (in amber) and a minimum speed (red and black barber pole), where the top of the bar is the speed where the stick shaker will begin to shake the control, in order to alert the pilots to the situation. In the case of an over-speed, a clacker warning will sound until the airspeed is reduced to below the Maximum Operating Speed (MMO or Vmo).
It can be tempting to feel that all of these systems interacting with each other is overly complicated. Many pilots and aviation fans express a longing for the “good old days” of stick and rudder flying, where it was just man and the machine. But that is to fail to recognise the role that aviation now plays in modern society. A perfectly acceptable aircraft with an acceptable level of risk for barnstorming cannot be compared to an acceptable aircraft with an acceptable level of risk for public transport. I can love a trip in a horse and carriage while still understanding that they cannot provide the same services as buses and trains do.
Over time, aviation has become much more extensive and also much more complicated but at the same time it has become safer than ever before. That’s what makes the 737 MAX failure so shocking. There have been many reasons given and many attempts to assign blame but at the heart of the tragedy is a simple corporate decision that a software upgrade could wait.
But I want to say that if the interactions of these modules (let alone the alphabet soup of the acronyms) are hard to follow, then please don’t dismiss all this as unnecessary complications or dangerous in itself. These systems and displays and interactions are there to support the pilot, not to take control away from him or her.
This brings us to the angle-of-attack sensors. Most passenger airliners have angle-of-attack sensors; this is not new technology and not specific to Boeing. On the 737 MAX, an AOA sensor is installed on each side of the forward fuselage, just behind the nose.

The sensors measure the amount of lift the wing is generating, using an external vane which rotates to align with the airflow. The vane is connected to two internal resolvers, each of which independently measures the rotation angle. The vanes then provide the measured angle of the direction of the airflow relative to the fuselage. One resolver is connected to the Air Data Inertial Reference Unit (ADIRU) computer for its side (left or right); the data from the left-side AOA sensor is processed and passed on by the left side ADIRU to the captain’s flight displays. The second resolver is connected to the respective Stall Management Yaw Damper (SMYD), which uses the data to calculate and send commands to the Stall Warning System.
AOA sensors are managed by “on-condition” maintenance, which is to say they are only maintained in response to a fault or malfunction. We previously looked at the faulty AOA sensor and its maintenance on the accident aircraft. It is clear that the AOA sensor was faulty and the replacement AOA sensor was misaligned and misinstalled. However, at no time did any of the flight crew receive a clear message that the AOA data was unreliable. The fact that the left-side AOA sensor and the right-side AOA sensor did not match should have triggered an AOA DISAGREE alert. The AOA DISAGREE alert should display on both Primary Flight Displays when the values of the left and right AOA data transmitted by the ADIRUs differ by 10° or more for ten continuous seconds.
It’s worth noting that the AOA DISAGREE alert cannot be tested on the ground.
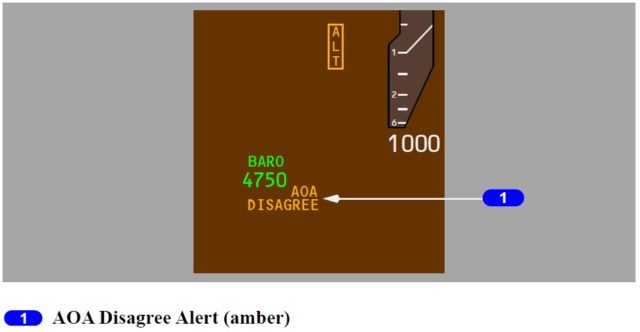
This AOA DISAGREE alert was first implemented in 2006 and since then has been installed in all newly manufactured Boeing 737 NG aircraft. But although the angle of attack is a basic principle of flight, the actual angle is not considered a primary parameter. Flight crew must know their airspeed, attitude, altitude, vertical speed, heading and engine thrust settings in order to operate the aircraft safely. An elevated angle of attack is signalled to the pilot through the stick shaker. As the angle of attack in itself isn’t considered critical information, an AOA indicator isn’t considered a necessary piece of equipment.
The Boeing 737-8 (MAX) design included the AOA DISAGREE alert as a standard feature on all aircraft, just as for the 737-NG. In addition, the operator could choose to install an AOA indicator on the Primary Flight Display, which would show the angle of attack as transmitted by the AOA sensor on that side. Only about 20% of the airlines who purchased the Boeing 737 MAX chose this optional extra.
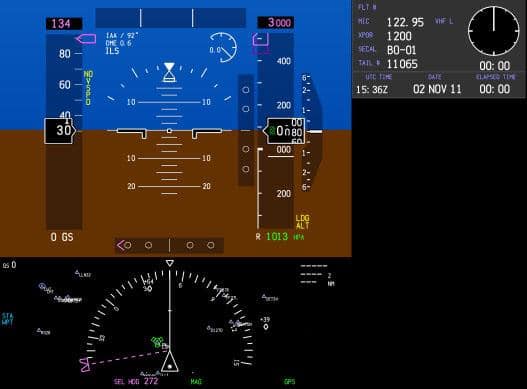
The 737 MAX was certified in March and Malindo Air flew the world’s first 737 MAX commercial flight, Kuala Lumpur to Singapore, on the 22nd of May 2017. A few months after that, Boeing realised that something was wrong.
The display system software was not producing the correct behaviour for the AOA DISAGREE alert. Instead of including the alert as a standard feature, the software linked it to the optional AOA indicator; that is, only those customers who chose to pay extra for the AOA indicator display received the AOA DISAGREE alerts. This meant that 80% of the airlines flying the Boeing 737 MAX had the standard AOA DISAGREE alert disabled, including Lion Air. This was not the intended behaviour.
The AOA DISAGREE alert was meant to be available on all aircraft, not only those who had opted for the optional indicator. However, when Boeing discovered that the software was incorrectly inhibiting the alert, they decided that this wasn’t an aircraft safety issue. There was no immediate need to patch or upgrade the software. They also saw no need to inform the airlines operating the aircraft that the alert wasn’t activated. Neither did they bother to tell the FAA, who had certified the 737 MAX with the AOA DISAGREE alert as a standard cockpit feature.
Boeing had authorised representatives who were tasked with representing FAA interests at Boeing, specifically ensuring compliance with FAA requirements. At least one of them knew that the 737 MAX was delivered with inoperable AOA Disagree alerts and apparently saw no reason to inform the FAA about this.
This software was verified and accepted by Boeing in 2015. Boeing reported the problem to the software provider in August 2017, specifically stating that the AOA DISAGREE alert was tied to an optional AOA Indicator display and therefore was not functioning on the vast majority of the 737 MAX fleet world wide.
Boeing Statement on AOA Disagree Alert
When the discrepancy between the requirements and the software was identified, Boeing followed its standard process for determining the appropriate resolution of such issues. That review, which involved multiple company subject matter experts, determined that the absence of the AOA Disagree alert did not adversely impact airplane safety or operation. Accordingly, the review concluded, the existing functionality was acceptable until the alert and the indicator could be delinked in the next planned display system software update.
In one of the costliest single decisions Boeing has ever made, both in terms of finance and in human life, the aviation giant determined that they would implement the fix to activate the AOA DISAGREE alert as a part of a planned display system software upgrade, which was scheduled for the third quarter of 2020. They fully intended to fix the problem but not for another three years, tying it to the rollout of the 737 MAX-10 aircraft. A Boeing authorised representative (again, whose role was to represent FAA interests, not Boeing’s) agreed to the postponement without ever informing the regulator.
A “Fleet Team Digest” was written to inform Boeing customers that the AOA DISAGREE alert was inoperable but it was never sent. Once again, they told no one that this apparently unimportant alert did not work in most of their delivered aircraft; not the aircraft operators, not the pilots, not the FAA.
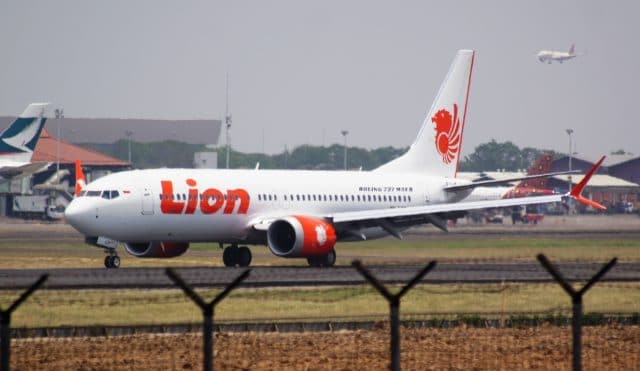
In August 2018, a year after they discovered that the AOA DISAGREE alert wasn’t functioning as intended, they provided a Flight Crew Operations Manual to Lion Air, which included the passage I quoted at the start.
Condition: The AOA DISAGREE alert indicates the left and right angle of attack vanes disagree.
1. Airspeed errors and the IAS DISAGREE alert may occur.
2. Altimeter errors and the ALT DISAGREE alert may occur.
Lion Air had not purchased the optional AOA indicator. Boeing failed to indicate in any way that the aircraft delivered to Lion Air did not have a working AOA DISAGREE alert.
The manual referenced an AOA DISAGREE light which effectively was not installed on the aircraft and did not reference the MCAS, which was.
In December 2018, almost two months after the loss of Lion Air 610, Boeing convened a Safety Review Board in order to consider, in the context of this fatal crash, whether the lack of an AOA DISAGREE alert presented a safety issue. The Safety Review Board concluded, again, that it did not.
The FAA finally couldn’t help but discover that most of the 737 MAX aircraft in service did not have a functioning AOA DISAGREE alert, fourteen months after Boeing had discovered the problem. The Acting FAA Administrator stated that “although an AOA DISAGREE message was not necessary to meet FAA safety regulations, once it was made part of the approved type design, it was required to be installed and functional on all 737 MAX airplanes Boeing produced.” And yet, the FAA still failed to take any measures against Boeing, saying that, although earlier communication with the operators would have helped to reduce or eliminate possible confusion, the inactive alert was considered to be low risk. The FAA issued an emergency Airworthiness Directive about runaway trim stabilisation but they were happy for the 737 MAX to keep flying while the design issues were fixed, despite one projection that predicted 15 similar crashes would occur over the lifetime of the aircraft if the situation wasn’t rectified.
The next crash was just five months later. On the 10th of March, 2019, Ethiopian Airlines Flight 302 crashed in remarkably similar circumstances.
Not until May 2019, a year and a half before the planned software update and seven months after the Lion Air flight 610 crash, did Boeing concede that the software fix might be urgent. They confirmed that they were issuing a display system software update to ensure that all aircraft could have the AOA DISAGREE alert that the aircraft should have been shipped with. It was, of course, too little, too late. Two aircraft had been lost with no survivors and aviation authorities around the world had grounded the Boeing 737 MAX.
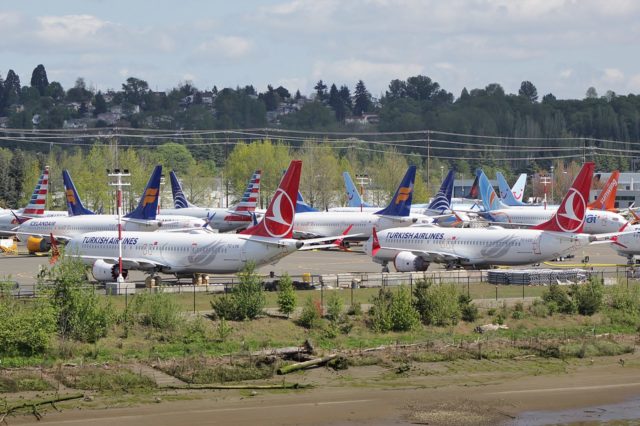
References:
- Aircraft Accident Investigation Final Report by the Indonesian National Transportation Safety Committee
- T1 Preliminary Investigative Findings
- Malindo operates world’s first 737 Max flight
- Boeing Held Off for Months on Disclosing Faulty Alert on 737 Max – Bloomberg
Who made this projection? Boeing or the FAA?
The FAA. I should have elaborated on that. There’s more on that here: https://www.flightglobal.com/safety/faa-2018-analysis-warned-of-15-fatal-max-crashes-months-before-second-accident/135747.article
Caption: “Angle of Attack (AOA) sensor on right-hand (Captain’s) side”.
That’s the left-hand side.
Oh argh. Thank you Ed, I’ve fixed it.
Who installed the misaligned aoa sensor and how much training and experience did they have? That looks like a ridiculous mistake.
See Sylvia’s earlier reports here https://fearoflanding.com/accidents/accident-reports/lionair-flight-610-the-maintenance/ and here https://fearoflanding.com/accidents/accident-reports/lion-air-610-the-faulty-aoa-sensor/
Very interesting, as always. I used to work in engineering and we occasionally discussed the “cost of being wrong” when deciding when to dismiss/delay a fix. Fortunately our equipment wasn’t airborne and we were normally discussing money, or up-time, or productivity, not lives. I would have been a bundle of nerves if I was working on planes (with hundreds of civilians on them).
Small typo. “This AOA DISAGREE alert was first implemented in 2006 and since than (THEN) …”
Fixed!
AOA is the poor cousin of basic flight parameters and not used to its fullest capabilities. AOA is an combined powerful indicator of the safety of your flight parameters. It encompasses your energy envelope to manouevere out of trouble. You could be at a high speed and still have limited manouvereability but the AOA being a great combination of speed, attitude and ROD would provide you with a sense of your energy. To me, it was an also indicator of having adequate thrust settings for certain profiles
Whilst this is taught in ground school, pilots should also be taught how to use it at the flying schools
Brings to mind the “swiss cheese” model of accidents (aircraft, chemical plants, medical equipment, etc) – each individual element doesn’t directly cause the problem, but can be imagined as a hole in one slice of cheese, with multiple slices in a stack. Problems occur when you’re unlucky enough to have a whole series of holes in individual slices lining up, letting the accident happen.
In a safety critical environment, the design approach can involve stacking more slices, reducing the size and number of holes, and trying hard to avoid systemic causes of hole alignment.
In this case, to my mind, the missing AOA disagree would have had minimal impact, except for: MCAS auto trim, lack of easy override, retriggering after manual intervention, stacking with no total limits, forces preventing manual override at extremes, and lack of good documentation (and probably others I’ve missed).
But then again that is why it is very unwise to just ignore and delay fixes to this kind of safety critical system, because on a large project you will never know how many other people are taking the “my issue won’t matter” approach…
Let us go back to the basics of the problem, or at least: give it a try.
With the “basics” I am not referring to the technical issues, they have been looked at comprehensively already. Witness the small number of comments. Of course, it is a very complex matter. Sylvia has really done a lot of work to clarify the technical issues. Even so, it is very hard to really grasp the details. I certainly have to look hard at Sylvia’s (as per usual superb) explanations even though I was once, in a previous life, a commercial pilot.
There are of course several angles to this story, but I have the feeling that a lot has to do with good old “Dough”; in other words: Money.
The introduction of increasingly sophisticated electronic navigation systems has enabled aircraft to fly from waypoint to waypoint. The rapid increase of air travel has led to a corresponding demand on new, more efficient and larger aircraft and, of course, pilots to fly them and engineers to maintain them. It also has led to a move away from the traditional airway system, where pilots used to navigate from beacon to beacon, VOR-DME or sometimes ADF. The rising cost of fuel and demands for less pollution led to more efficient and quieter power plants. Greater efficiency was achieved by more advanced engine design and electronics. The new technology increased reliability which in turn allowed greater leeway with ETOPS, where smaller but more efficient wide-body twins are taking over from the “Jumbos”. RVSM operations, again made possible because of technological advances, together with the narrower spacing of flights, following flight paths determined by waypoints, put more demands on ATC. The result, again, more technology. More accurate lateral and vertical spacing, reducing the vertical separation in the higher airspace (RVSM), it all would have put an increasing workload, leading to an increasing overload on the human operators if the progress would not have been matched by an increasing amount of automation, taking a lot of the workload out of the hands of the pilots. ATC, likewise, had to be confronted with new electronic systems and automation. Aircraft are an expensive investment and have to be kept in the air. The electronics enable engineers to quickly download the stored data between flights and analyse them. They can monitor the health of an aircraft over an entire flight, even if no faults are indicated. The automated systems even can send data to the maintenance base in flight.
This is my own analysis of what is happening in the world of air travel, or was happening until the corona virus struck. The introduction of this mini essay. Now let us examine the problem.
The problem we are now facing is the “Human Factor”. No, I do not mean “Pilot Error”, the catch-all explanation all too often used to coveniently blame the pilots. Yes, we have discussed cases where this was the case, but now I digress.
I have been a “stick-and-rudder” pilot for most of my career. Automation was in its infancy when I retired. So yes, I may be a bit biased in favour of the good old days but modern technology need not be the bogey, either.
It all, as I mentioned, comes down to MONEY – human GREED.
We rarely read or hear about air traffic controllers not being able to cope with the demands of the new era. OK, there are no weight limits to the amount of equipment that can be installed in a control tower or an air traffic control centre. There is a lot more redundancy, more experienced staff can be rostered during peak times, but by and large ATC is operated by often cooperating governments. Airlines pay airway charges (for instance to Eurocontrol), the staff are semi-state employees with a structured pay- and pension scheme. They also are trained to a very high standard.
There is, in principle, no financial limit to the amount of training they will receive. I have only in very rare cases encountered ATC controllers who were not superb professionals. One of the best was a Nigerian at Ikeja Airport, Nigeria in the early ‘eighties. He was just very, very good.
Airlines have to make a profit. And they are facing increasing competition from low-cost airlines. No, I do not accuse them of poor training but there are limits to what airlines can afford.
And no, I do not have exact figures, but training a crew to operate a modern airliner, let’s say a 777, a 787 or a 737Max must be a very expensive business.
In my days, it was a groundschool taking about a week of intensive learning, followed by a written examination (no multiple choice then!) and a day or two in a systems trainer, a cockpit mock-up where the lay-out would be made familiar and some basic procedures practised.
After that we would be put in the simulator. Depending on the complexity of the aircraft between 20 and 25 hours, followed by a simulator check. If that was successful, we would do a few hours “base training” in the actual aircraft before starting our route training.
So far so good? But in those days we would still use fairly basic navigation systems, not all that different from what could have been installed in a light twin at the time.
Not so today. The aircraft and its systems are only part of the groundschool. I would not be surprised if the “hard” systems, like the airframe, the flight controls, the hydraulic systems, the engines, the landing gear, pressurisation, hydraulics, even the electrical systems could be covered in less than two weeks. But the modern “gizmos”, the electronics, the warning sytems, the automatics: I can well imagine that this may require another 10 days of hard work, of late-night cramming.
This, after passing the exams (probably multiple chouice now, but still tough) the crew will have to put it all into practice in the simulator.
If I may make an (only slightly) educated guess: Training ususally is conducted as a crew. A captain, who may be upgrading from a less sophisticated type of aircraft, an F/O who may be a rookie, straight out of the flying academy. The training may take about six weeks. Assuming that they are on the airline’s payroll: A captain’s salary may be in the order of € 9000 a month or more, a newly hired F/O may be on € 2800.
So we are, if we add expenses, talking about € 19000 and that is just the cost of the crew ! I would not be surprised if the cost of training, just for ONE crew, would be in the order of € 250.000.
An airline that intends to introduce, let’s say, 50 new 737 MaX aircraft would need to train, probably 3 crews per aircraft. No, I have not used exact figures so let it suffice to say that training the crews, especially for a newly introduced type, will cost the airline a multi-million dollar (or Euro) figure.
The same, maybe not to the same extent, will apply to the engineering staff who must be able to download, absorb and analyse the data that are provided by the on-board computers. They also will undergo training, again, running possibly in the tens of thousands, plus the acquisiton cost of the computer software.
So what picture do have have now?
An airline needs pilots, trained and qualified to operate the new type of aircraft. They also need to upgrade their software and train engineering staff. We are talking about millions, before even one low-fare-paying passenger has set foot on board.
There will be a limit to the amount the airline can afford to spend on training. Assuming that most or all trainees graduate and the company fleet captain and engineering captain will have ferried the first aircraft to base from the manufacturer (the first crews will have been trained at the manufacturer’s facility), they will go over the aircraft with the now newly qualified crews and wish them happy landings.
Is there anything wrong with that senario? Not really. The crews may be expected to be ready, the more experienced captains will be rostered with a novice F/O, the less experienced calptains will be teamed with an experienced F/O, often someone who is close to getting command him- or herself. This is a time-proven method, although it has led to the occasional tragedy (e.g. the Habsheim accident), but this was an exception.
But “Money” can upset the applecart. The manufacturer cut corners in efforts to maximise profits. The 737 Max was a 737 more in name than in reality because it had aerodynamic peculiarities that had to be compensated for by electronics. electronics that did not work flawlessly.
But by keeping the designation “737” the Max did not require a new typerating. A differences course is, if my guess is correct, all that would be required.
The engineers would also be inclined to view the new aircraft as just another 737, albeit with upgrades and bigger.
It saved a “helluva lot of money”, both for the operator and the manufacturer. It could have worked out if Boeing had been up front with the consequences, the virtual absolute reliance on the electronic compensation systems (MCAS) and the actions required if they failed, It also fudged the need for a more stringent quality control of routine online mainentance.
In the end, sadly, there were only losers.
The “Max” is still grounded.
The airlines did not take delivery.
The FAA has not issued a new type certificate.
And there have been losses: Losses: of lives and money.
For those who find my comments too much to digest, in condensed version:
– Boeing stuck to the “737” designation to save money.
– Larger engines, too big. Either the landing gear had to be redesigned and the retractable stairs sacrificed, or the engine pods had to be moved forward.
– This changed the flight characteristics, necessitating additional electronic “fixes”.
– The aircraft became very reliant on electronics, not only for navigation and systems operations but even to remain controllable.
o THE SUM TOTAL OF THE CHANGES IN FACT COULD and should HAVE LEAD TO A NEW TYPE CERTIFICATION.
– The FAA relied far too much on the integrity of Boeing’s internal process of certification.
– Boeing’s prime goal became making profits.
– Airline customers took it all for granted. They had relied on Boeing’s previous very good record.
– Result: No new type rating required. Gaps in training of crews and maintenance staff. This became only fully apparent after the loss of two 737 “Max” with all on board.
o THE ENTIRE FLEET IS STILL GROUNDED and production of the Max has been suspended.
o Both Boeing and the FAA have been negligent.
I knew a lot of the information that Sylvia had collected in this post; not least because of her interesting previous posts, I had investigated myself.
What suprised me, though, was this: “A “Fleet Team Digest” was written to inform Boeing customers that the AOA DISAGREE alert was inoperable but it was never sent.”
I have been musing over this for a while, and I think the key is in Boeing’s attitude as expressed in the emails that were published (a long PDF to read), and which Rudy has so eloquently explained: Boeing had to keep the FAA from noticing that MCAS was an important system, and that the AoA sensor had become safety critical. If the FAA had noticed, then MCAS malfunction would have needed to be trained in simulators, and that wouldn’t do.
Boeing relied on the buy-in of airlines in terms of pilot training costs to swing puchasing decisions away from airbus. If you can save a lot of training expenses by upgrading your existing 737 to a Max, that makes you more likely to purchase a Boeing. If the upgrade had required a more expensive retraining, then some airlines might have preferred to buy Airbus.
Therefore, Boeing could not even recommend to some of its customers to do this training, or the FAA would have become suspicious. This is very clear from the published emails.
That’s why there is no MCAS in the manual. That’s why the AoA sensor alert was not treated as safety-critical. This is why Boeing gambled on the probability of an incident with this being very low even after the first crash had already occurred. Or maybe they thought they wouldn’t get caught?
I believe all domestic customers of Boeing (certainly Southwest) received the AoA display upgrade that enables the alert. I’m wondering how that happened.
Mendel,
I think that you nailed it.
Re training cost. I have no real figures, but based on what I know it cannot be cheap. I have just tried to make an estimate, expanding on baisa of the cost of training up a pilot on the Citation.
Training of the first crews, when an operator buys new aircraft, is included in the contract. But other than that, the operator will bear the cost. Or, if not, I strongly suspect that the manufacturer will have included it in the price of the aircraft.
Major airlines have their own training facilities. We did the BAC 1-11 ground school with a ground instructor who seemed to know every nut and bolt in the aircraft, but the simulator belonged to Aer Lingus. They had the 1-11 a long time ago, but as long as there were still operators who were willing to pay, the simulator was still in operation.
“It’s worth noting that the AOA DISAGREE alert cannot be tested on the ground.“ On top of all the other Boeing failures, the installation, calibration and operation of a component their software has made critical to flight, cannot be fully tested on the ground. It’s difficult to believe that all these failures slipped through to the final product. The foremost priority of any manufacturer should be the safety of their product. Boeing’s culture has gone astray.
That is odd, because you’d think it would be the easiest thing in the world to manually move a vane to one limit and then see the alert light. Since the first 737 Max crash (but before covid lockdown) I’ve taken a number of flights with steps based boarding, and seen the AOA vanes (on a variety of planes) just out of reach. Many have “Do not touch” labels, but one wonders is that is a mistake.
I’m also very surprised that the mis-calibration wasn’t spotted by a step in the normal maintenance procedure to check that both units agree and both show neutral/zero angle when stationary on the ground.
Not sure if you’ve read the previous post but that goes a long way to explaining what went wrong with the maintenance.
As Boeing didn’t install the AOA disagree alert on this plane, there would have been no way to test it. Having said that, if the the engineer had conducted the installation test correctly, the issue would not have arisen.
The problem with this flight was that the signals were different even when the vanes were aligned with each other, so to discover this, you would have had to set both vanes to agree with each other. The problem with the vanes is that they’re on opposite sides of the airplane, which makes it hard to check that on the ground. In flight, the airflow aligns them, but on the ground, vibrations etc. may have misaligned them a little, so how can you tell?
They’re also supposed to be accurate to a tenth of a degree or better. If you touch them, you run the risk of bending them, and then this accuracy might be lost.
A real-life example is a car: if its front wheels have become misaligned, it’s usually not obvious until the tires show signs of uneven wear. It takes a precision measurement in a specially equipped garage to re-align them.