Hard Landing Within Limits
In this simple incident, we can see how a trivial failure and a simple-but-wrong assumption has knock-on effects that could have easily led to the structural failure of an aircraft.
On the 1st of December 2017, a night charter flight departed Basel Mulhouse Airport in Switzerland at 20:55 local time for a flight to Pristina International Airport (PRN) in Kosovo. The aircraft was an A320-232 (registration SX-ORG) and there were six crew members and 178 passengers on the flight. The operator was a Greek charter airline with four A320s configured for economy passenger flights (180 seats).
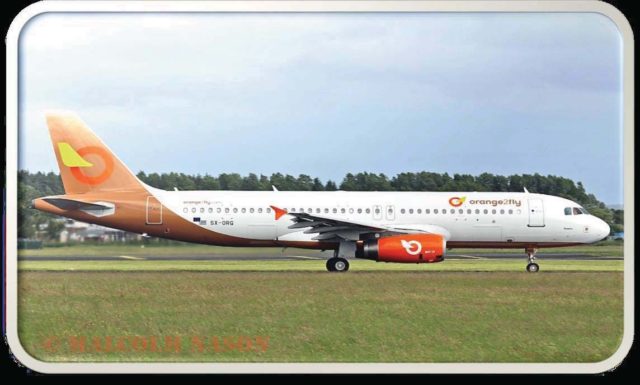
That night, the captain was the pilot flying and the first officer was pilot monitoring. Note: the Kosovo AAIIC (Aeronautical Accident and Incident Investigation Commission) also uses the terms pilot and copilot as well as CM1 and CM2 for these roles in the report. I will stick to the terms we are used to.
The procedure at the airline was that landings at Pristina Airport were to be flown by the captain. The captain had over 10,000 flight hours with 688 on the Airbus A320. The first officer had 7,350 hours with 406 on the Airbus A320.
During the flight, the left sliding window started fogging up, blocking the captain’s peripheral view. The heating in that window was not working, which had been noted through the Aircraft Technical Logbook. This was on the minimum equipment list (MEL) which lists items which are not required to be operating for the flight to proceed. The name is confusing. Effectively, instruments and equipment which are not essential to the safety of the flight can be listed on the MEL and the captain can thus take the decision to continue the flight without the listed equipment. The equipment in question should be repaired as soon as possible but the aircraft does not have to be grounded, for example, because a fire extinguisher in a lavatory has failed; it is sufficient to lock the lavatory door and stop it from being used.
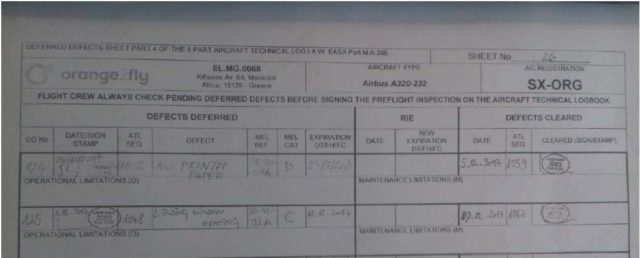
You can see in the image above that there were two MEL entries in the Aircraft Technical Logbook: NO PRINTER PAPER in the Data Management Unit (DMU) and LEFT SLIDING WINDOW HEATING. The pilots checked the logbook before the flight and were aware of both items.
This is all standard. No one wants to cancel a flight because a printer is out of paper or a window heater isn’t working; that’s the point of the MEL.
The flight was uneventful and the captain, as pilot flying, prepared for a full-flap landing on runway 35 at Pristina. He disengaged the autopilot at 2,000 feet above the ground and flew manually with the auto thrust engaged. The flight crew spotted the runway at three miles out and at 1,000 feet the pilot monitoring called out the stable approach parameters.
It was snowing with temperatures above freezing; the runway was reported as wet and slushy. The flight crew agreed to conduct a positive landing, that is, a firm landing at a higher vertical speed, to avoid hydroplaning on the wet runway surface. This allows for the tyres to make good ground contract , as opposed to a softer landing (“greasing it”) can may lead to the aircraft skimming across the water. One symptom of a positive landing is that it can be a hard landing, because you are descending at the high end of normal as you touch down.
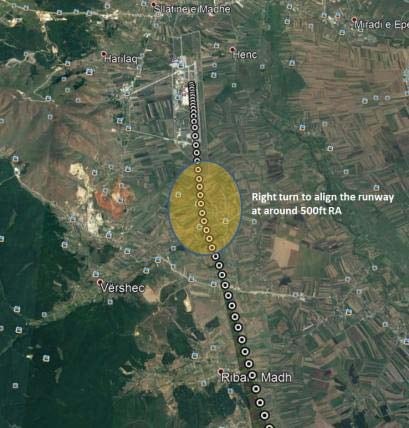
Runway 35 at Pristina has a light right turn on final approach, where the aircraft is about 500 feet above the ground. Shortly after this point, as the Airbus reached three hundred feet above the ground, there were a number of side stick inputs on the captain’s side, where the pitch angle varied between -2.5° (nose down) and +4.5° (nose up). The speed also varied, between 138 and 141 knots. The vertical descent rate varied between 2,400ft/min and 600ft/min and the vertical load factor was between 0.9G and 1.1G. The pitch deflections continued until the flare at 20 feet above the runway, ranging from +2° to +6° (nose up), with the rate of descent varying between 880ft/min and 200ft/min. Then, the captain applied full back stick, increasing the pitch angle from +2° to +3.5°. The rate of descent decreased and the airspeed dropped to 135 knots.
The aircraft touched down at a 3.5° pitch angle with a ground speed of 135 knots and the right wing slightly down (2.5°). Braking action was good.
The flight crew discussed the landing between themselves. This is important because the flight crew is expected to note any/all high load events in the log book, which brings it to the attention of the maintenance personnel who can then carry out the appropriate maintenance tasks.
The most common high load events are:
- vertical turbulence
- lateral turbulence
- hard overweight landing
- hard landing
The flight crew agreed that the the landing was “not unusual” and that everything seemed normal. Both later reported that neither the Electronic Centralized Aircraft Monitor (ECAM) nor the Flight Management Guidance System (FMGS) showed any errors.
In order to support the flight crew, the A320 has sensors which react to high load events. If such an event is recorded, a report is generated. The LOAD<15> report (“high load event printed report”) is configured by the operator to be produced either immediately after a high load event or delayed so that it does not print until until after landing.
The pilot’s report is considered primary with the LOAD<15> report there to support the post-flight analysis. When the flight crew report a high load event such as a hard landing, the maintenance personnel analyse the LOAD<15> report to determine the necessary maintenance tasks.
This report and accompanying data can be easily transferred from the aircraft to diagnostic ground support tools which are used to analyse the data and provide a list of maintenance tasks which are focused on the areas of the aircraft most likely affected.
After the landing at Pristina, no LOAD<15> report was generated. This supported the captain’s view that the landing was not unusual. The captain spoke to the cabin crew and told them that although the landing was a little bit hard, it was within limits. He took no further action.
The aircraft remained in service for flights between Basel Mulhouse and Pristina. Two days later, after the aircraft had flown a further eight legs, the first officer mentioned the incident with the airline’s Training Manager because he still felt a little bit dubious about that landing.
As a result of his statement, the Data Management Unit was inspected and loaded with paper. It immediately printed out the LOAD<15> report which had been generated after the hard landing.
This report showed that the vertical acceleration at the point of landing was 3.04 G. To put this into context, a 1G landing means that the impact on touchdown is equivalent to the weight of the aircraft. The higher the G value, the harder the landing.
For the Airbus A320, a landing with a vertical G of over 1.5G, it is considered a low severity event. At 1.6G it is a medium severity event and at 1.75G it is a high severity event. The Airbus A320 vertical G hard landing threshold is 2.6G. Any landing over 2.6G is considered to be over the aircraft’s structural limits.
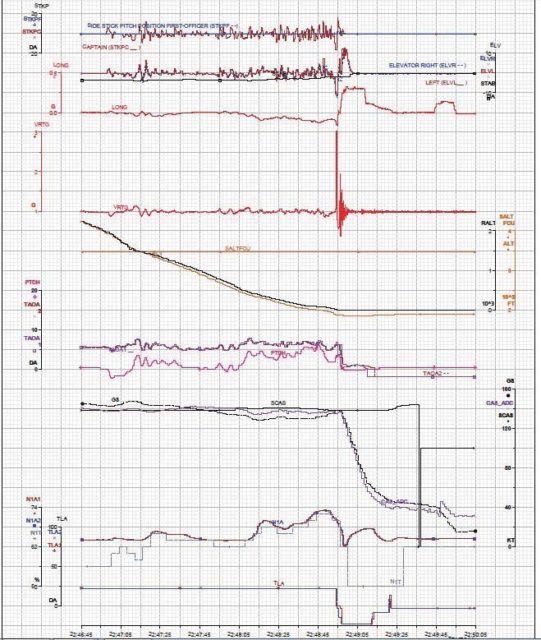
At 3.04G, the landing is classified as severe or “red status”. In the case of a severe high load event, airline maintenance personnel are told to contact Airbus for assistance.
The pilot’s report is the primary means for detecting a high load event; the LOAD<15> report is only to support the maintenance crew in their analysis of the event and what areas, specifically, require general or detailed inspection. Although the LOAD<15> report is automatically printed if specific parameters are exceeded which could point to a heavy landing, it is specifically watching for high vertical acceleration. A high load event could still take place without it being triggered. As a supporting document, if a pilot is not sure about a landing, he or she can request a print of LOAD<15> for further details.
However, it seems that the flight crew used the lack of the report to convince themselves that the landing couldn’t have been so bad. Worse, the report wasn’t missing because the parameters hadn’t been exceeded. The LOAD<15> report had been triggered based on three separate parameters: the radio altimeter descent rate, the rate of descent at touch down and the high vertical acceleration.
Although the pilots knew that the Data Management Unit was out of paper, it did not seem to sink in that there may be a LOAD<15> report waiting to be printed. As such, they didn’t do anything to see that the report was transferred to maintenance or even just let maintenance know that there was an incident. Aircraft Communication Addressing and Reporting System (ACARS) is a digital link system for the transmission of messages between aircraft and ground. The airline did not have an integrated system which would make the report transferred automatically; it was completely up to the flight crew to report.
The first mention of the lack of paper in the Data Management Unit was on the 24th of November 2017, a week before the flight. The paper was added on the 5th of December, which led to the immediate printing of the “missing” LOAD<15> report.
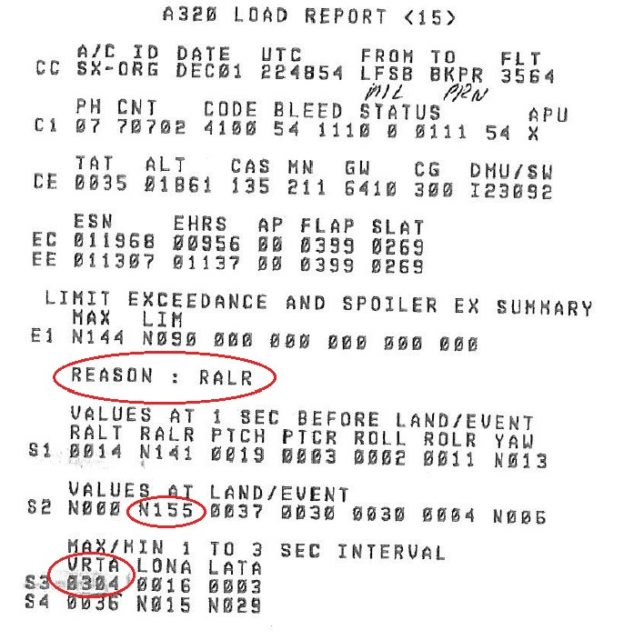
As soon as maintenance saw the LOAD<15> report, the aircraft was grounded.
The shock absorber assembly on the right side main landing gear was considered unserviceable and had to be scrapped by “component mutilation”. The operator also changed all main wheels and the rear shock absorber.
A proper conclusion for an incident report like this is difficult, as obviously a printer out of paper did not cause the hard landing. Kosovo AAIIC determined that contributing factors included the captain making multiple nose-up and nose-down inputs at low level before belatedly pulling back on the stick. They also list the snow and wet runway and, separately, the crew’s decision to come in with a high rate of descent for a “positive landing”. And finally, the fogged up left-side window which reduced the peripheral view of the captain.
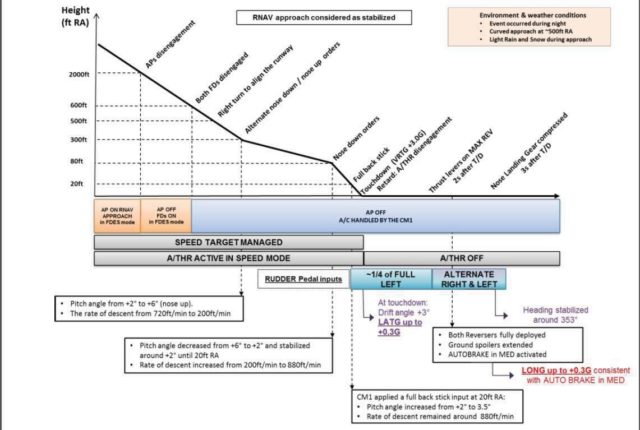
However, the hard landing and its causal factors aren’t actually the problem here and the report makes that clear. The fact that the aircraft continued to fly without any inspection was a serious risk which compromised the safety of those passengers on board for the next eight flights.
The safety actions reflect the real issue; the report wastes no time discussing how to avoid hard landings. The AAIIC recommends that the operator either implements an ACARS system so that the reports are automatically transferred or ensures that there will be paper in the Data Management Unit. Either is acceptable, simply losing a report is not. Further, they recommend immediate safety training for all flight crew regarding reporting a hard or overweight landing. Any captain who feels the need to reassure the cabin crew that the landing may have seemed “a little bit hard” should really be proactive about getting the aircraft looked at.
In researching this piece, I found a related accident report, this one by the British AAIB: Airbus A321-231, G-MARA 28 July 2008. In this case, the pilots reported the hard landing but the engineer did not quite understand the process in the Aircraft Maintenance Manual. I didn’t have the space to cover it this week but I think
you may enjoy it as an interesting related case for reading over the weekend.
Taking more than 11 days and 8 flights to load the damn paper is a bit excessive.
The G-MARA crew was lucky the nose gear failed to retract… instead of failing to extend. Also, as a software developer, the two different interpretations of the troubleshooting flowchart is very interesting.
Isn’t it? I liked how accessible they made the misreading rather than just casting him as incompetent.
I’m off thread here but not off topic. We’ve had 2 incidents in a month now (not including this one). I just want to add something that’s worrying me. We’ve got pilots taking to the skies again in aircraft that have been maintained in a different way (active or deep storage). Everything is unusual for a while now. I’ve heard some pilots saying that the rules can be “flexed” a bit in order for them to keep their type rating. I disagree with this : the pilot type ratings should be MORE stringent now rather than less. I never liked the fact that the PF can let the plane fly itself for 3 hours (with the PNF watching) then have to take over at the most critical point (landing it). How many runway excursions are we gonna have in the next year? They were already increasing in number. There was already a flight sim shortage before all of “this”. I understand that airlines want to get back in the sky but that doesn’t mean safety should be relaxed in order to do so. This should be regarded as an unwanted but necessary precaution to further accidents (i.e. tighter rules and checks rather than “flexing” the rules). ATC’s are gonna be rusty too. I would say that if an ATC detects anything to do with an incoming aircraft that is not nominal then he/she can force the PF to GA. I hope you get my point here. By all means delete or move this comment to a more suitable place. Regards.
Thanks for an interesting writeup, I didn’t know they had landing G sensors.
Are aircraft designed so that the landing gear absorb heavy Gs to protect the structural integrity of the planes as much as possible? That would make for a good blog article, imo.
Please consider explaining “auto thrust”, e.g. “He disengaged the autopilot at 2,000 feet above the ground and flew manually with the auto thrust engaged.”
It’s surprising that the tech is so primitive, all of the details of every flight could easily be wirelessly transmitted to a data house at each airport, the tech is very well understood and inexpensive.
I can understand putting off replacing the window heater as I can see the work being complicated (getting into the space between hull and inside wall?) — but how difficult did Airbus make replacing the paper? That shouldn’t be so hard that it can’t be attended to quickly. Judging from the problems I had as a software engineer getting computers that just sat in one place to communicate, an automated data transfer system would be … nontrivial; ISTM the AAIIC should have recommended an indicator on the printer that would tell people to read what it’s trying to print before taking the airplane off the ground.
Andy’s comment seems well-taken — but aren’t there already unbreachable standards for what a pilot has to do if they’ve been inactive? We know there are highs and lows in demand, such that I’ve seen various news items about pilots being furloughed and recalled; given that people are already nervous about flying, the airlines should find it in their own interest to make sure that pilots are well-practiced after a layoff before taking off in a real airplane. (This leads me to wonder whether there are any similar standards for cabin crew; I was once early enough to the waiting area for a transatlantic flight that I overheard cabin crew sorting out work, and have considerable respect for both the day-to-day work and for how they need to be ready to help in emergencies.)
And an amusing typo in the G-MARA report: “There appeared little consensus from their comments, other than that many pilots do not hold the sidestick in the manor intended by the manufacturer.” One wonders what kind of extension would be needed to hold the stick in another manor….
I was actually fairly impressed with the printer. Put paper in it, and pop – out comes a damning report from four days ago…
As far as paper goes, though, I’d bet it’s a thermal printer that requires very special paper that’s only available from Airbus and has a long lead time. They probably ordered some only after they noticed it had run out, and it didn’t show up ’til a week or two later.
J.
True that it’s an impressive printer — or (more likely ISTM) the computer behind it; I’m used to desktop printer-computer combinations that just wedge and have to have jobs removed from the queue and resent. But the paper issue sounds more like US military procurement than a way to run a manufacturer of civil aircraft; can somebody who knows more about aircraft certification practices comment on whether a specialized (e.g., fireproof?) paper would be a requirement? If it is, I can see a small operation getting behind on inventory — although that should lead to questions about whether they’re fit to operate (i.e., if they can’t keep this in stock, what else are they missing?)
The question you want to ask is, how many reports are they printing that they’re having to replace the paper ahead of schedule? ;-)
Speculation. I assume that the landing G sensor is probably fairly close to the main gear position. Given the flexibility of modern structures and the size of the aircraft, it seems possible that the sensation in the cockpit would be well damped. This might explain the lesser G experienced there. I can’t believe that crew would consider a 3G impact within the normal range, if felt in the cockpit.
Even if so it’s hard to believe that cabin crew would not have noticed such an impact.
David