Final Report from the Contained Engine Failure of United flight 328
On the 20th of February 2021, United Airlines flight 328 made international headlines when a fan blade separated from the right engine shortly after take-off. Flight UA328 was a scheduled domestic flight from Denver International to Honolulu, Hawaii. The aircraft was a Boeing 777-200, registration N772UA, built in 1994 and powered by two Pratt & Whitney engines model, PW4077.
On board that day were two flight crew and eight cabin crew. The preflight weather forecast indicated moderate turbulence from 13,000 feet to 23,000 feet above mean sea level. The captain warned the flight attendants that it might be a bit rocky after departure and to stay seated until they were told it was clear. The cabin crew then boarded 229 passengers for the flight.
This was the first time these two pilots had flown together: the captain was the Pilot Flying and the first officer was in the role of Pilot Monitoring. The captain remembers that the right engine was a bit of a problem to start but then seemed fine thereafter. They taxied to the runway and departed normally. As the aircraft flew into the clouds at about 10,000 feet, they experienced some light turbulence. The two pilots agreed to increase the engine power to climb through the turbulence more quickly.
As the flight was flying over Broomfield, Colorado, the flight crew increased the engine power as they climbed through 12,500 feet. They felt some mild shaking. The flight crew initially thought was more turbulence, but then there was a tremendous shudder and a very large bang. The aircraft jerked to the right as the right-side (No. 2) engine shut down. An engine fire warning light appeared.
The last thing that the captain had seen before flying into the clouds was the terrain: the Rocky Mountains. “We need to turn back now,” he remembers saying. The first officer was thinking the same thing. He called the controller to declare an emergency and request an immediate return to Denver. There was no response.
I’ve noticed before that in the US, pilots will say “I am declaring an emergency” but often, they don’t actually say “mayday”, which repeated three times is the correct way to declare an emergency. So I was intrigued in this instance to see the captain see it as a clear escalation.
The captain said he told the first officer, “Do the mayday, mayday, mayday.”
First officer: Mayday, mayday: United uh 28… United 328 heavy, mayday, mayday.
The first officer remembers another pause. The transcript shows that TRACON respondeded twice asking him to say that again.
The first officer didn’t remember any questions, just that he pressed again to say that they needed to turn. They needed to turn now.
His actual words were “United three twenty eight heavy maybe aircraft uh just experienced an engine failure, need to turn immediately.”
This time ATC responded. “Right turn or left?”
The captained turned for a left 180° while the first officer started working through the checklists. As per the engine fire checklist, they discharged both fire extinguishers on the right engine, but the fire warning continued to display. They didn’t know that they’d lost the engine cowling, which meant the fire retardant was just blowing into the air.
They secured the right engine. Then one of the cabin crew called the cockpit.
The captain told him, “Hey, we’re real busy; we’ll get right back with you.”
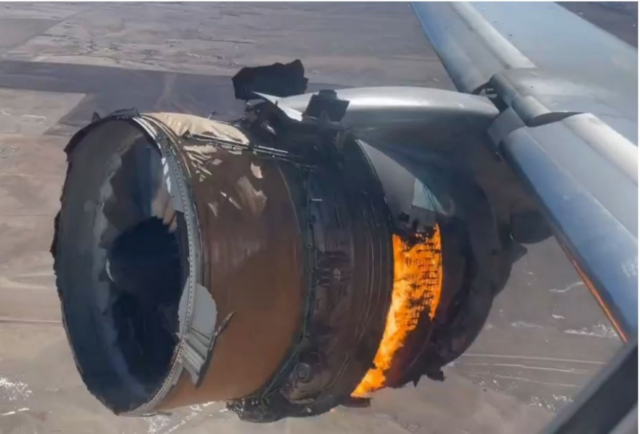
At the same time, the passenger seated in the aisle near the engine recorded a startling video of the vibrating engine and fire. Here is what I wrote about the video a few days after the incident:
The incident is frequently being referred to as an uncontained engine failure, which I suspect is because of this video showing the engine with no cowling. However, this was a contained engine failure, which means that the failed engine pieces (in this case, the fan blades) are contained within the engine case or exit via the tailpipe. Much development has been put into aviation technology to contain the fan blades of an engine in the case of a failure, as the potential hazard of high-speed debris acting as shrapnel would put the aircraft and the passengers at much more risk than the engine failure itself.
An NTSB representative confirmed that the video made the failure look “not as contained as it actually was”. He said that both fire suppression tanks were deployed into the #2 engine, the thrust was neutralised and the fuel was cut. The fire was likely residual flames from a damaged fuel line.
The aircraft was still vibrating heavily but flying remarkably well. The cabin crew member checked in again, saying he just wanted to touch base and see if there was anything the cabin crew needed to know. The two pilots said later that they were very happy with the cabin crew who did what they could without insisting on interfering. Both pilots also said that they worked well together, with the captain flying the aircraft and handling the radio while the first officer went through the checklists. The captain commented on the number of them.
There was a litany of other checklists. Like, for instance, if you get an engine fire checklist, you also get an engine failure checklist, which is redundant. And [the first officer] did that checklist. He just punched right through it. There was also the overweight landing checklist, which only has one item on it, and it’s redundant. It’s the ground prox flap override switch to override, and that’s something you’ve already done on the fire checklist. And the engine fail checklist, it’s the same thing; you’ve already secured the engine.
ATC offered them any runway. The captain chose runway 26: it was closest,and the runway was 12,000 feet long, which, based on the calculations they had just made, was three times as much runway as they needed. The first officer remembers a brief conversation about dumping fuel, as they were overweight for the landing, which seemed like a terribly unsafe thing to do with an engine on fire. “Our overweight situation was basically, in my opinion, you know, the least of our worries,” said the first officer.
On the base leg, a new alert came up with the “engine fail” checklist. The first officer remembers three more checklists.
One was overweight landing. The second that I saw was fuel imbalance. Those two, basically, to me, we know. You know? We have a situation. We’ve experienced engine loss, power loss, and everything. That’s what triggered the fuel imbalance. The overweight was obvious. And the third that came up was…I think it was TAC fault or TAC [Thrust Assymmetry Compensation] –it was amber… which I knew that was obviously the result of the problems that were going on with the right engine.
The warning light for the engine fire turned off. This might seem like good newes but actually, the only reason that the engine fire light had turned off was because the fire had continued to rage and had taken out the engine fire detection system.
They touched down safely. The controller asked them to stop straight ahead and the airport rescue and firefighting teams raced to them. The fire fighters doused the right engine with water and foaming agents for almost 40 minutes, until the engine was no longer smoldering.
Finally, the Boeing 777-200 was towed off of the runway and air stairs were brought for the passengers to disembark. It was only then, with the aircraft on the ground, that the flight crew saw that the cowling had come off the engine and the damage done by the fan blades.
The debris from the aircraft was scattered over an area of about 40 acres (about 16 hectares or a bit smaller than the area of Grand Central Station in New York).
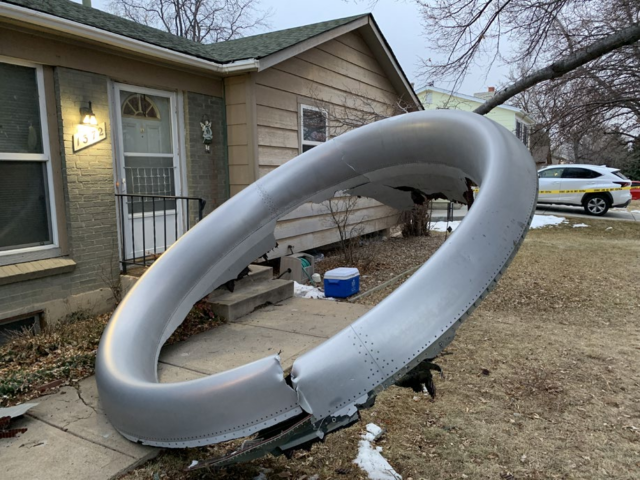
There were amazingly no injuries on the aircraft or on the ground, only property damage.
It was obvious from the start that the engine had suffered a fan blade out (FBO) where a fan blade separates from the engine. The fast-moving fan blade then severed the engine inlet lip skin, the fan cowl support beam and additional components of the inlet. This led to the cowling coming off completely as seen in the video.
Examination of the engine revealed that the separated fan blade and other fan debris impacted the fan case, which successfully contained the fan blade fragments. Damage to the nacelle inner and outer barrels was observed, and a post-accident evaluation indicated that the displacement wave of the impact resulted in a deflection of the fan case and contact with the nacelle doors and hinges, which subsequently resulted in the failure of the inlet aft bulkhead and the fan cowl support beam. The failure of the bulkhead, along with the damage to the inner and outer barrels, allowed these structures, as well as the inlet lip skin, to separate from the engine.
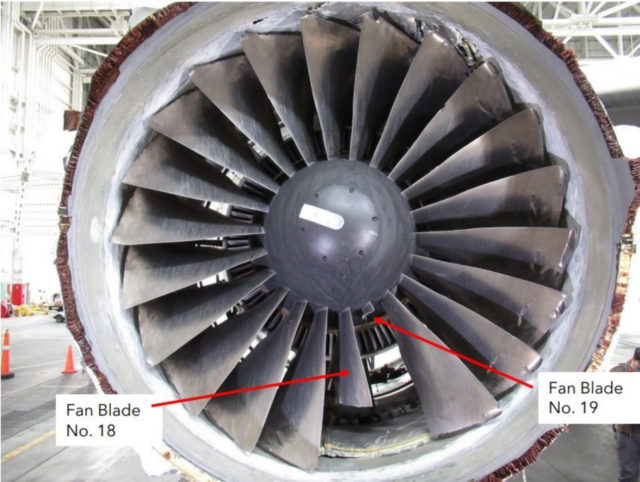
As the blade snapped off, a number of bolts broke in the impact, allowing the hot gases to escape from the engine and light the leaking fuel. The servo fuel heater fractured along with the cowling, releasing high-pressure fuel into the nacelle.
The fan blade had a long fracture (“transversely across the chord of the airfoil”) which was the result of a fatigue crack. The blades had been inspected for both external and internal cracks using a thermal acoustic imaging process, as per the overhaul inspection required every 6,500 cycles, where a cycle is a single take-off and landing by the aircraft. Since then, five years had passed, with the fan blade accumulating a further 2,979 cycles.
The imagery from the 2016 inspection showed low-level indications which were reviewed but dismissed as camera sensor noise or maybe some loose contamination in the cavity of the fan blade. The blade should have undergone a second thermal acoustic imaging inspection or at least had a team review of the anomalies. Instead, the blade was approved for continued service without any further consideration.
This was the fourth time that the PW-4000 powered 777 aircraft had suffered a fan blade out event caused by fatigue cracking. The first event took place in 2010 where the blade broke in half. Then, in 2018, United flight 1175 from San Francisco to Honolulu suffered a full-length fan blade separation while flying over the Pacific. At this time, the 2016 thermal acoustic images for the Boeing 777-200 were reviewed again; however, the “low-level indications” were dismissed as random noise. Once again, the blade was again approved for continued service.
Two of the indications on the images were exactly where the fatigue crack must have started. Investigators concluded that they were very likely the first indications of the fatigue crack which broke the fan blade.
Probable Cause and Findings
The National Transportation Safety Board determines the probable cause(s) of this incident to be:
The fatigue failure of the right engine fan blade. Contributing to the fan blade failure was the inadequate inspection of the blades, which failed to identify low-level indications of cracking, and the insufficient frequency of the manufacturer’s inspection intervals, which permitted the low-level crack indications to propagate undetected and ultimately resulted in the fatigue failure. Contributing to the severity of the engine damage following the fan blade failure was the design and testing of the engine inlet, which failed to ensure that the inlet could adequately dissipate the energy of, and therefore limit further damage from, an in-flight fan blade out event. Contributing to the severity of the engine fire was the failure of the “K” flange following the fan blade out, which allowed hot ignition gases to enter the nacelle and imparted damage to several components that fed flammable fluids to the nacelle, which allowed the fire to propagate past the undercowl area and into the thrust reversers, where it could not be extinguished.
All twenty-five of United’s Boeing 777s with the PW-4000 engine were grounded while Pratt & Whitney performed thermal acoustic imaging inspections of the fleet. They also issued a service bulletin to introduce ultrasonic testing blade inspections to be performed immediately and then at regular intervals. Finally, the thermal acoustic testing was reduced from every 6,500 cycles to every 1,000 cycles. Meanwhile, Pratt & Whitney developed a new ultrasonic inspection which can detect small cracks that would not be detected by thermal acoustic imaging. This inspection now takes place every 275 cycles.
With the increased inspection intervals and ultrasonic inspections, there are now multiple opportunities to detect internal cracks in the fan blades.
You can read the full accident report on the NTSB website. The photographs and some of the detail were taken from the publicly released docket.
We’ve been reading about spurious airplane parts with forged documents getting into worldwide circulation. Was this possibly involved in this or other incidents?
Pratt&Whitney were involved in the investigation. If this involved a forged blade, it would’ve been mentioned in the repirt.
Mendel got there first but yes, you can depend on the fact that P&W would have been the first to say that it wasn’t their parts thus it wasn’t their fault that it cracked.
Great writeup. Thank you for an exciting story.
VASAviation link
https://m.youtube.com/watch?v=G7-zh7Sebr8&pp=QAFIAQ%3D%3D
From every 6500 cycles to every 1000?!? Crikey. That’s gotta hurt.