The Unstallable Plane That Stalled
The Cessna 185 Skywagon is a high wing, single engine aircraft: basically a Cessna 180 with six seats, a strengthened fuselage and a slightly more powerful engine. It’s a popular aircraft in remote areas where access to modern airstrips may be minimal.
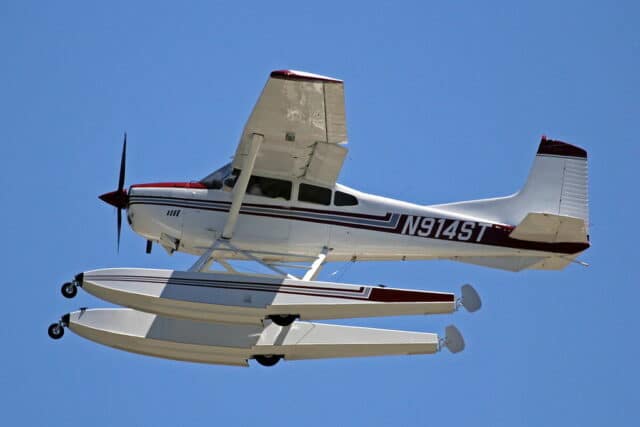
The Skywagon can be fitted with floats or skis: this particular one, registered in Finland as OH-CVT, was equipped with floats. It also had a cargo pack and a Robertson STOL (short take-off and landing) kit, which reduces the stall speed.
The aircraft was owned by Polar Lento Ltd. Originally, the aircraft and the pilot were operating under Polar Lento’s certificate. However, on the 30th of April 2003, the Finnish Flight Safety authority cancelled the certificate, as the maintenance manager of the company was not approved. Polar Lento Ltd applied for the aircraft to be added to the certificate of Ivalon Lentopalvelu Ltd. The authority added the aircraft to Ivalon Lentopalvelu’s operations on the 2nd of May 2003. The contract between the two companies stipulated that Polar Lento Ltd would cover all fixed and variable expenses of the aircraft while operated by Ivalon Lentopalvelu.
The pilot held his commercial licence and had 2,176 hours on floatplanes, most of which were on Cessna 180-types.
On the 24th of June, the day before the accident, the pilot flew the Skywagon from Lake Kilpisjärvi to Lake Ounasjärvi, Enontekiö , the Finnish part of Lapland. His fuel load had been close to the maximum when he departed Lake Kilpisjärvi. The floatplane landed at Hetta fishing harbour and docked there overnight.
The morning of the 25th, the pilot did his preflight checks and pumped the water out of the floats with a hand pump. When the passengers arrived, he weighed the baggage. He loaded some of it into the netted cargo pack under the fuselage and the rest in the cargo area behind the seats.
It is common for flight operations in the wilderness to have the take-off weight close to the maximum. After the luggage and the passengers were loaded, the aircraft weighed 1,460 kilograms (3,220 pounds); the maximum take-off weight was 1,520 kilograms (3,351 pounds). The centre of gravity was within limits, though close to the forward limit.
They taxied from the pier to the take-off position. During the taxi, the pilot checked the engine. He then took off along the lake, heading due east into a light headwind of three knots. The waves on the lake were about 10 cm high (just under four inches).
When looking at the length of an aircraft’s take-off, we usually split it into two parts: the ground roll or ground run, where the aircraft is moving along the ground, and the distance from when the aircraft leaves the ground (rotation) until it reaches 15 metres (50 feet). Acceleration is based on the propeller thrust, which has to overcome the surface friction of the wheels and the aerodynamic drag of the aircraft.
On water, however, the hydrodynamic drag of the water causes the most resistance to acceleration. Take-off is effectively broken down into three phases. The aircraft starts its take-off run until the resistance reaches its peak (at about 27 knots). Then there is a short second-stage take-off phase where the floats are placed so that the aircraft is “on the step”: the floats have lifted partway and are hydroplaning across the surface of the water. The aircraft is no longer fully supported by the water but retains just enough surface friction to manoeuvre. Each successive wave is struck with increasing severity, so the pilot has to use elevator pressure in order to skim across the waves as the aircraft continues to accelerate. An error at this stage risks capsizing the aircraft; but soon, especially with a good head run, the aircraft will lift off the water (rotation), transitioning to the final stage of take-off.
At this stage, when the aircraft “unsticks” itself from the water, the pitch angle needs to be reduced — that is, the nose pitched slightly down — in order to give the aircraft a chance to gain speed. When the friction between the floats and the water disappears, the pitch up is briefly unbalanced; for how long depends on the float type. In addition, as the aircraft climbs, the ground effect reduces. The downwash behind the wing increases, the horizontal stabiliser angle of attack changes and the downward load on the stabiliser increases. As a result, the aircraft pitches up unless the pilot controls the flight path using the elevator. If this pitch up is not controlled, the aircraft is at risk of exceeding the stall angle of attack. The aircraft accelerates more easily when it is close to the water because the aircraft-induced drag is less in the ground effect. Thus, it is even more important for the floatplane pilot to control the pitch of the aircraft and gain airspeed before climbing away.
The Cessna 185’s take-off run on Lake Ounasjärvi that morning was approximately 500 metres (1,640 feet) of which the last 300 metres (980 feet) was on the step. The pilot noticed that the wind was coming slightly from the left (easterly).
The pilot had set the trim so that the aircraft would lift off from the step and begin to climb away. The rudder trim was set almost as far right as it could go. The pilot described the take-off as quick and easy. “I let it lift off by itself. It was well-trimmed and it lifted off normally by itself.”
The aircraft suddenly yawed and rolled to the right. They were about 15 metres above the water, ready to transition to the next phase of flight. The pilot immediately applied full opposite aileron and left rudder in an attempt to straighten out the aircraft. He pressed his right foot on top of his left foot in an attempt to gain full left rudder.
It didn’t help.
The aircraft yawed more than 90° to the right; that is, it turned at a right angle to its direction of travel. The right wing tip hit the water first, throwing the aircraft into a cartwheel. The nose and right wing hit the water, followed by the empennage as the cartwheeling continued. The left door and windshield were torn off of the fuselage.
When the tail impacted the water, the aircraft capsized and came to a halt, floating upside down in the lake, buoyed up by its floats. The water at the crash site was approximately 30 metres (100 feet) deep.
The cabin roof was at a depth of two metres (6.5 feet) and the cabin filled with water immediately. 170 litres of aircraft fuel and 10 litres of engine oil spilt into the lake. The water temperature was 8-10°C (46-50°F).
The pilot unbuckled his seat and tried to undo the seat belt of the passenger in the right-hand seat next to him. He couldn’t find the buckle. The passenger didn’t move and showed no signs of life. Running out of air, the pilot had to dive to get to the surface.
The passenger in the middle row, a 14-year-old boy, unbuckled his seat belt. He saw the surface through the left door opening and dived through it and swam to the surface.
A number of people witnessed the crash. Boats raced to the capsized aircraft, arriving within three minutes of the accident. One bystander dived into the water twice to try to reach the passenger trapped in the right-hand seat. It had been five minutes since the aircraft had capsized. The diver touched the passenger’s lifeless hand but was unable to free him from the aircraft.
The Enontekiö fire brigade arrived on the scene about twenty minutes later. One of the fire brigade with scuba diving gear attempted to recover the passenger but was unable to free him. The aircraft was towed towards the Hetta shore but became stuck in the bottom of the lake about 60 metres (200 feet) from the shore.
Two hours later, another, more experienced diver arrived on the scene. He was able to release the seat belt, which had tangled around the right ankle of the now-drowned passenger who was trapped in the front. Although the front seats were equipped with shoulder harnesses, neither the pilot nor the passenger had worn them. The diver carried the body to shore where a doctor pronounced him dead. The cause of death was later confirmed as by drowning. The passenger’s face was badly bruised, probably from hitting his face on the instrument panel. Although wearing a life jacket would not have saved the passenger, as the seat belt was not released in time, wearing the shoulder harness would have meant that he would have been conscious and able to escape once the aircraft had capsized. However, at that time, in Finland, there was no obligation to do so, although some countries do require this.
The surviving passenger said that the pilot did not give any safety briefing before they took off. The pilot said that he had given the briefing, including how to use the life jackets, seat belts and doors.
The pilot suffered a cut to his face and bruises around his body. The surviving passenger also had some bruising but no serious injuries. In both cases, most of the injuries were on the left side. The aircraft was beyond repair.
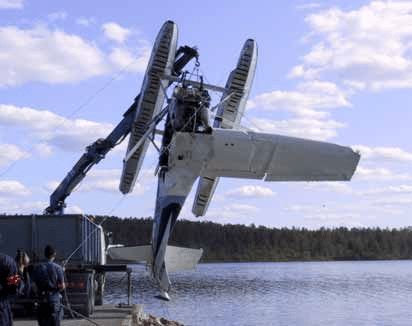
No one in the plane was wearing a life jacket. Although this wasn’t a factor in the accident, the Finnish report points out that passengers on a boat naturally wear life jackets and it seems illogical that sea- and floatplane operators do not usually wear them. One reason for this is that the certification of airworthiness inspection standard requires that the life jackets be stored in their original plastic bags. Aircraft life jackets are not very rugged because they are intended to be used only once, in an emergency. Floating and automatically operating life jackets aren’t practical, specifically because of cases like this where the occupants have to dive out of the capsized aircraft in order to escape the cabin. However, there are approved life jackets which could be used to deal with these circumstances.
The life jackets are required to be easily accessible; but, in most instances, there would not be enough time to put the life jackets on in an emergency unless the aircraft is planning a forced landing from cruise altitude. The investigators of the accident put forward that, if the intent is to have life jackets practically available in all phases of flight, the occupants of the aircraft should be wearing them throughout.
In interviews after the accident, the pilot said that the aircraft lifted off easily and quickly. When it suddenly rolled and yawed to the right, he tried to stop the movement by using full opposite aileron and rudder. He said that the aircraft was gaining altitude and speed at the time. He said that he tried to stop the roll and the yaw and continue the take-off. He never considered aborting the take-off or lowering the nose. The aircraft continued to roll and yaw and the nose dropped. The pilot remembered that he held the yoke with two hands but could not remember whether he pushed or pulled.
The investigation focused on the control systems. The impact damage to the aircraft made this difficult: the left wing was attached to the fuselage only by the aileron cables and one of the flap cables. The right wing was still attached, with the flap set to 20° down, which matched the setting of the flap control lever in the cockpit. The elevator control cables were intact and, although they were loose as a result of the bent empennage, investigators were able to confirm that movement of the yoke still transferred to the elevator. The elevator trim system position indicator showed neutral and the tailplane was in the neutral position. Both the left and right rudder pedals were intact. The rudder trim was ⅓ turn (one-third turn) from the extreme right position.
There was no reason why the control systems would not be working normally during the flight.
The pilot didn’t know the speed at which the Cessna 185 lifted off that day, although he said that it was normally around 55 knots. He didn’t have any observations about the speed during the take-off run or the initial climb. He never lowered the nose to gain airspeed as the aircraft lifted off, nor did he consider any other manoeuvres to increase his airspeed. He simply let the aircraft lift off and climb by itself.
The pilot had flown since 1988 in north-east Lapland, mostly for the reindeer industry or tourist flights. His home bases were Lake Ounasjärvi and Lake Kilpisjärvi; most of his flights had been short hops to the lakes around the area. He had had no previous accidents nor incidents in 2,940 hours of flight, with 8,125 take offs.
However, the investigation discovered that despite his experience, he had never practised stall recovery on the Cessna 185. The pilot had no knowledge of the aircraft’s stall behaviour at all. His opinion was that the Cessna 185 simply didn’t stall.
A further issue was that his Cessna 185 had been extensively modified. The addition of floats, cargo pack, short take-off and landing kit and a three-blade propeller had never had their combined effect documented.
The stall speed, at least, should normally have been documented as a part of the airworthiness check. A test flight was logged from four years previous by another pilot. The checklist showed that, at that time, with floats installed, the clean stall warning was triggered at 64 knots indicated airspeed (KIAS) and the aircraft stalled at 56 KIAS. The landing configuration stall warning was triggered at 58 KIAS and the aircraft stalled at 48 KIAS.
However, the aircraft had undergone further modifications and maintenance since then.
Earlier that year, a hangar roof had collapsed onto the aircraft at Enontekiö airport during a storm. The collapse dented the upper wing surfaces, ailerons and flaps. The aircraft was flown (carefully, one assumes!) to Rovaniemi airport for repairs.
The maintenance team discovered an incorrect right wing geometric twist, which was unrelated to the hangar roof collapse but probably happened during repairs done previously in the USA. As a result, the aircraft had a tendency to roll and had been uncomfortable to fly because of a lack of aileron trim. This might explain why the pilot had the aircraft trimmed full right rudder on take-off: to correct for this roll. When they repaired the damage to the right wing, they also corrected the geometric twist, removing the aircraft’s tendency to roll. They did not notify the Flight Safety Authority for the correction as they considered it to have been a minor repair.
The repair and maintenance were finished on the 20th of June, five days before the accident. The accident pilot ran up the engines and flew a test flight. He confirmed that, after the adjustment of the geometric twist, the aircraft no longer had the tendency to roll.
Then he filled out the test flight documents . . . except for the section on level flight where data was missing. The documents included blank fields for the pilot to fill out for the speed at which the aircraft stalled.
- Stall speed clean ___ KIAS (knots indicated airspeed)
- Stall speed landing configuration ___ KIAS
- Stall warning ___ KIAS
The pilot had put dashes in the blank fields, instead of noting the speed where the aircraft begins to stall when clean and the speed at which the stall begins when the aircraft is configured for landing. The last blank field, which should have stated the speed at which the stall warning sounds, had been filled in with the word OK.
The maintenance company received the document and gave the aircraft a certificate of release to service.
No one had any idea what the stall speed of the aircraft was. With the changes to the right wing geometric twist, the angle of incidence of the wings had been changed, which would have affected the stall speed. It seemed that the pilot had no knowledge of the aircraft’s stall behaviour at all. His opinion was that the Cessna 185 simply doesn’t stall. The investigators believed that he may have been afraid of stalling and so never tested the aircraft.
The Skywagon was a write-off but the investigation needed to understand the aerodynamics of the accident flight, taking into account the modifications. So, they re-created the aircraft. They equipped a Cessna A185E to match the accident aircraft, adding a Robertson STOL, floats (although not exactly alike), a cargo pack under the fuselage and a three-blade propeller. The aircraft’s weight was approximately 50 kilograms below the maximum take-off weight.
The first simulation of the accident scenario was done at 3,000 feet. The test pilot set idle power and then maintained altitude in order to allow the airspeed to reduce. Then when the airspeed had dropped to 48 knots, the test pilot applied maximum power. The nose pitched up by 10° which increased the angle of attack by 10°. The increased angle of attack caused the right wing to stall violently and the aircraft rolled and yawed to the right. The aircraft was travelling at 55 knots at the time.
The test pilot recovered the aircraft using the normal procedure, losing only 150-200 feet. The stall warning horn sounded throughout. The simulation was then repeated with the same result. Further flights, however, did not always result in the violent right wing stall. In five of the fourteen attempts, the aircraft rolled 50-70 degrees to the right in two seconds. Nothing significant happened on the other nine attempts, even when the speed was reduced to 40 knots.
Further test flights were done to check the stall warning and air speed indicators of the aircraft. The stall warning horn did not sound during take-off.
The investigation shifted their focus to aerofoil aerodynamics. They covered the test aircraft with hundreds of 90 mm wool threads. These threads made the airflow around the aircraft visible. The thread movements were filmed in flight with five video cameras: two cameras attached to each wing strut and one on top of the fin.
This allowed the study to document the airflow direction and turbulence from the movement of the threads. There was also a sixth camera attached to the cabin roof filming the instrument panel and horizon as well as recording the cabin sounds.
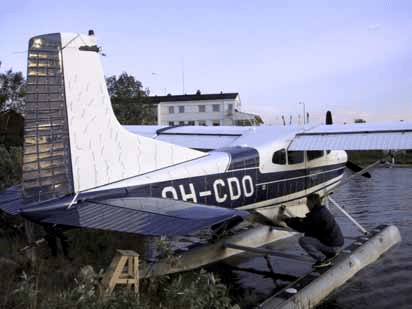
The wool threads showed that, on those occasions where the aircraft rolled to the right, the airflow separated first from the right wing tip and immediately after this, from the right wing root. The separation line progressed rapidly from the trailing edge to the leading edge and led to the sudden roll. The sudden aircraft roll was immediately stopped and the aircraft recovered when the pilot moved the yoke forward, reducing the angle of attack.
The investigators discovered that it was possible to suddenly stall the aircraft at a speed of 50-55 knots in the take-off configuration. The aircraft regularly suffered a sudden right wing tip stall, which caused the right roll and pitch down. They concluded that the cause of the right wing tip stall was the aileron angle, which caused a sharp edge to form on the upper surface. The short take-off and landing kit incorporates a link between the flaps and the ailerons. The ailerons turn downwards in the take-off configuration. Cessna aircraft have a hinge line on the upper surface. As a result, turning the aileron down causes a sharp angle on the upper surface. The air is unable to flow around such a sharp edge and stay attached. The result is a sudden right wing tip flow separation.
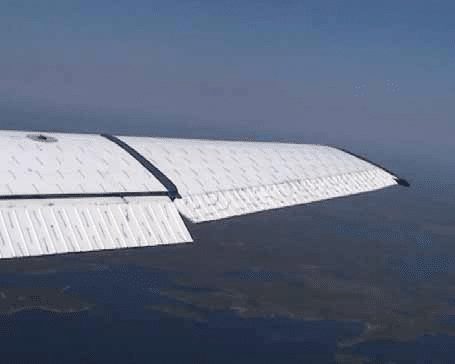
Despite this detailed study, they were never able to make sense of why this only happened a third of the time. By rights, the aircraft should have stalled every time. In any event, the pilot had been lucky up until the day of the accident.
The commission named three direct causal factors of the accident.
The first factor was the pilot’s take-off procedure, which allowed the aircraft to climb after getting airborne, rather than controlling the pitch in order to increase the airspeed. As a direct result of this, the angle of attack increased and the right wing stalled.
The second factor was the tip-stalling tendency of the STOL kit. The flow separation of a standard Cessna aircraft begins from the wing root area. The sharp edge on the upper surface induced flow separation which caused the right wing tip to stall.
The third factor was the pilot’s response. There was no evidence that he pushed the yoke forward to unstall the wing, which in the flight tests consistently dealt with the issue. Instead, he applied full left aileron and rudder. If he had pushed the yoke forward, the aircraft may still have crashed but it was unlikely to have cartwheeled across the water and injured the passengers in such a way. Instead, his full opposite aileron turned the right aileron downwards, which made the right wing tip stall worse.
The indirect causal factor was the pilot’s lack of experience with stalling the aircraft. He told the investigation that he had never stalled the aircraft, which meant that he was unable to recognise the stall during the take-off. He was quite convinced that the aircraft would not stall and believed it was such an abnormal flight condition that he saw no need in practising it.
With the changes to the right wing geometric twist, the angle of incidence of the wings had changed, which affected the stall speed. The maintenance organisation should not have given the aircraft a certificate of release without verification of the slow flight and stall characteristics. Of course, even if another test pilot had completed the flight test, the pilot should still have practised stalls in the aircraft, knowing that the slow flight and stall characteristics of his aircraft had changed.
But, even though he knew both wings had been taken off the aircraft and maintenance done which would affect the stalling characteristics of the aircraft, he did not see the point in any stall manoeuvres as a part of the test flight or for general practice.
One last indirect causal factor was not wearing the shoulder harnesses in the front seat.
The Finnish Safety Investigation Authority has published the full accident report in English.
The conclusion of the accident report:
Probable cause
The pilot let the aircraft continue to climb after getting airborne without reducing the pitch angle to gain airspeed. The aileron and flap connection of the R/STOL kit of the aircraft combined with the aileron type caused right wing to tip stall in the take-off configuration.
The pilot did not recognise the stall and did not act in the required sense to recover.
Two recommendations were made by the investigation commission.
The first was that pilots be informed about the stall behaviour of the Robertson short take-off and landing kit on the Cessna 185 aircraft, both by listing the issue in the aircraft flight manual supplement and through education through the aviation authority.
The second was that the Finnish Flight Safety Authority revise existing regulations so that all persons on board must wear a life jacket during water operations, rather than insist that they be kept in plastic bags.
I didn’t see life jackets while flying being in the slightest bit comfortable, but then I googled aircraft life jackets, and they were very different than what I was familiar with. Instead of being canvas bags of kapok or styrene or whatever, they’re thin flat plastic one-use balloons. Yeah, I don’t see them being daily use items.
Also, the 3 paragraphs after the first picture are repeated after the second one.
Eep, not sure what happened there but fixed! Thank you.
I’m realising that I don’t actually know very much about types of life jackets used in aviation.
I am terribly impressed by both the building of a test plane and the wool threads. That’s just incredible. I wish every industry took things as seriously.
Yes, I thought that was ingenious!
“Tufting” https://en.wikipedia.org/wiki/Tuft_(aeronautics) is a fairly standard technique in aerodynamic research. Computerised flow simulations have made it old-fashioned, but it still works.
I don’t think OP is impressed by the technique more so that the investigators went to that length to ascertain the root cause of the issue.
Great write-up. Really important for all pilots to be safety-minded. Yes, a stall is not a “normal flight condition” but is involved in a large percentage of accidents.
Not sure how you engineer an inflatable life vest that is robust enough to be repeatedly re-worn. I suppose it would be worth looking at what military pilots wear.
That’s a good idea! Sorry that you had to wait for this to be posted; I have pre- approved you for future comments.
Sailors wear that kind of life vest. They are comfortable enough to be worn all the time when uninflated, and they inflate automatically when they are immersed in water. Here’s an example:
https://www.crew-safe.co.uk/shop/150n-lifejackets/crewsaver-crewfit-150n/
I am baffled by the notion that an aircraft would be unstallable; I’ve read about (but never flown) the Ercoupe, which supposedly was unspinnable due to interconnections between controls (I wonder how it behaved in crosswind landings?), but never of an aircraft that couldn’t be stalled. I don’t see anything in the report about asking the pilot where he got this notion, but that level of human factor was probably outside the investigators’ mandate.
And I’m also impressed by the research.
I wondered if the reference to the pilot being possibly nervous about stalls, not the type of supposition you’d usually see in an accident report, may be why they didn’t push this further.
I owned and successfully flew 300 hours in 1946 Ercoupe N99404. Yes, an Ercoupe is unspinnable, but not unstallable, as you note. There is of course, a big difference. But an Ercoupe is brilliantly designed and tested, and it’s quite rugged. The wings stall at the wingroot, and the elevator stalls much later, so you remain in a kind stall entry, but as the wings stall, the nose drops keeping the Ercoupe “mushing” forward with full aileron control. The rudders are interconnected with the nose wheel and ailerons via the yoke, so in the “stall entry” condition, you can’t cross-control and enter a spin. If you are stalling and turn, you simply turn. Even an aggressive power-on, abrupt nose up stall.. the Ercoupe just drops the nose in whatever direction you are pointing it and gains airspeed and keeps mushing.. That “mushing” characteristic can be useful when needing to quickly lose altitude, unlike a conventional aircraft where deliberate cross controlling ailerons and rudder might be the technique to lose altitude.
Cross wind landings: You simply crab the Ercoupe appropriately, and the trailing link main landing gear make contact with the runway behind the CG, which pivots the fuselage into alignment with the runway. You hold the nose up a little before you let it drop to contact the runway after the fuselage is aligned with the runway. It’s an easy, natural technique. CAUTION: Cross wind landings at night need the PIC’s full awareness that your landing lights will crab with the aircraft: They will not be pointing down and illuminating the runway surface. You can choose to install one flood light to help in these situations.
Cross wind gust upon landing: Having landed at or near stall speed is important. You maintain directional control of the nosewheel and rudders with the yoke. If a gust lifts the upwind wing, you immediately apply sufficient main wheel braking to stall the lifting wing.
Interesting discussion.
Most pilots, flying in the bush, wouldn’t takeoff in a float plane, even empty and practice stalls. Floats can cause a pendulum effect too.
While I have never flow the C-185, I have flown a C-172 on floats. (on wheels too). Flown a C-210 a lot too, same engine as C-185, but on wheels. Many other types.
The C-172 float version is quite a dog lifting off. even with light fuel load and only one passenger. One has to start the takeoff run, with no flap, get it up on the step. Then as it accelerates skimming on the water, put out say 10 degrees flap. That may give one lift off. If not, you are still scooting across the water, then slowly lift up one float, to break the surface tension, then the second float .
Now stay in ground effect, just above the water and slowly raise the flaps to zero. Stall horn may be going off at this time !
Finally you have enough airspeed to safely climb away.
Went on to fly a J-3 on floats, hand swing the prop but with a C-90 engine, and no electrics much better performance.
Flying on floats , in a friends plane two summers ago, I did wear a pull to inflate life jacket.
Survived this “flying” went on to 30 year career with a major Airline.
Thanks for the detailed description. Sorry for the wait in the moderation queue. Your future comments will go straight though.
Supposedly the Antonov AN -2 can’t stall. See a discussion on Aviation Stack Exchange. That’s an exaggeration as it loses lift and “mushes” to the ground, but it does not upset. Supposedly still flies at 35-40 knts per https://www.an2flyers.org/an2specs.html.
It is a very large biplane with a large wing surface area and “automatic” low speed lift device deployment. Automatic is in quotes because they are primitive spring loaded contraptions in keeping with its simple bush plane concept. Does anyone have any first-hand experience with that plane?
The F/A-18 Hornet keeps flying after a stall because of its cool aerodynamics (wing may be stalled, but the vortices from the leading edge extension maintain flow over the wing and over the horizontal tail too, for controllability)
First of all stall occurs at a specific angle of attack (AoA) for a certain configuration – flaps, gear, CG, airflow behind propeller… The stall speed will vary with g loading. Then there’s gusts that will change speed over surfaces as well as AoA.
There are aircraft lifejackets that are designed for constant wear that can be inflated once out of the aircraft.
The pilot seems to have been faulted for incorrect stall recovery, but let’s face it, at 15 m he’s hitting the water before stall recovery could have been accomplished.
There’s a large number of survivable accidents where pilots and passengers were fatally injured because they did not use shoulder harnesses.
Robertson owns a piece of this, but how much is hard to determine as this kind of accident is rare.
Here is a .pdf file about the Robertson STOL kits.
Note the aircraft in story above had the “fence” on upper wing between flaps and aileron on test plane. This would prevent span wise flow from the upper wing root surface out to wingtip.
While I don’t know the Cessna wing from an aerodynamic perspective, I would imagine there is “washout” in the outer wing area. This is a subtle twist in the wing, so that the wing root area will stall first as the stall limit is reached, whereas, the outer wing leading edge, has a reduced Angle of Attack and ailerons will remain effective ..to a limit.
https://skyway-mro.com/wp-content/uploads/2019/04/RSTOL-brochure_2019-web-2.pdf
This is very useful, thank you!
I got my pilots license in Canada, training on Cessna 172’s. They are very similar aircaft to these 185’s, which are slightly larger, with slightly bigger engines. When I did my flight training (first Vancouver, then completed in Oshawa, Ontario), we stalled these things regularly. The Cessna 172 stalls very gently, and it was tough to get a good spin going. But we did power-on stalls (the nose pointing way up!), and for excitement, the instructor might kick a rudder pedal over as the incipient stall began. That would provoke the start of a good violent stall/spin, which one would correct with alerions neutral, full opposite rudder. But the Cessna highwing is a very forgiving aircraft. You had to work to get it to spin, which is as it should be. But really, you can stall it quite easily – just reduce power, and keep pulling the nose up. The horn will go off, the aircraft will shudder, and it will drop a wing and enter an incipient (the beginning of a spin). We were discouraged from spinning them too violently but it’s really important when learning to fly, that you get a good chance to really toss the aircraft about. The 172 is not rated for aerobatic flight (no loops or inverted flight), but stalling was both OK, and back in the 1980’s, was part of the training. A Private Pilot Licence Flight Test, I think actually required that the pilot demostrate stall and stall/spin recovery to pass the test. Stall, drop a wing, and recover was a key part of the training.
It also developed pilot-confidence. We practiced stalls, and something called “box-canyon turns”, where you simulated flying into a box-canyon, with a rising surface, mountains on three sides, and you find you are trapped, and with the a/c in a crazy full-on power regime, with the nose pointed up, and the stall-warning horn blarring, you had to turn the a/c 180-degrees, back in the direction you came, without dropping a wing. In the 172, you could actually do this. It’s a good, stable aircraft.
Thanks for posting this accident report. It is really interesting. I don’t get to fly much anymore, but I have a place on a lake, and the local float plane operators practice circuits on our lake often. I’ve been to FInland, and it looks exactly like Northern Ontario – lovely place. Accident reports like this are really helpful for all pilots. We used to have a sign at my flying club which said: “Study the reports of Aircraft Accidents. Learn from the mistakes of others, since you won’t live long enough to make all the mistakes yourself.”
Also, I liked “Captain Ray’s” comments about the 172 on floats. Once you have big floats on, I would expect it would really increase drag and make for a very different flight-feel. Thanx for the info.
Intriguingly, I may have reason to go to Ontario in the coming years, so I’ll get to compare for myself!
‘The air is unable to flow around such a sharp edge and stays attached.’
This sentence is a bit contradictory. Could there be an extra ‘s’ in ‘stays’?
Nevertheless, great writeup, thank you!
Good catch! Yes, of course it is unable to stay attached. Thanks for that. And further comments from you are now preapproved.
I can see where they were coming from with the life jackets, but is a life jacket really that useful when you’re stuck in an upside down aircraft? Surely the extra buoyancy would make it harder to swim out?
The idea is that you wouldn’t inflate it until you were out of the aircraft. That said, if it’s true that the pilot didn’t do a briefing, I’m not sure his passengers would have known that.
As for “The air is unable to flow around such a sharp edge and stays attached.’”
I think that should be the air flow separates over the downward deflected aileron, from the wing surface, boundary layer. Some operators install VG or Vortex Generators on the wings to reactivate the boundary layer on the wing, and lower stall speeds.
https://www.aircraftspruce.com/catalog/appages/microvgkits1.php
Mark Langdon, After my instructor, during my Private demonstrated spin recovery in a Cessna 150, I would go out , solo building hours for the flight test, and spin the 150 frequently. I enjoyed that sensation of being weightless, as you kicked in some rudder at the stall, holding the yoke back, and suddenly the wing would drop as the airframe shook. Hold the elevator back and do two turns or so in the spin. Then move the yoke forward, and apply opposite rudder to the spin, instant recovery. C-150 spun easily.
I never had to demonstrate spin recovery for a Cdn or FAA flight test.
The scariest (?) thing i had to demonstrate for an FAA Commercial/IFR flight test was VMC in a light twin; a Seneca II. An aircraft I knew well having flown them in Africa. One engine at idle thrust, then reduce airspeed, until you run out of rudder authority. Didn’t have to do this for my Cdn Commercial flight test.
That was my mistyping a sentence that was badly phrased to begin with. — the air is unable to stay attached to the sharp edge.
This is clickbait, right? Or written by someone who knows nothing about airplanes?
An “unstallable” airplane?
I take it you didn’t read it.
Of course not. If the headline contains such a massive error as that, the entire article is most likely useless.
My goodness, in the time it took you to post your two asinine comments, you could have read enough of the post to realize they were unnecessary! And you’d have likely also enjoyed it as a well-researched and written piece.
Good grief Don – the headline describes the false belief of the pilot whose belief and actions were the major reason for the crash, the details of which are presented in the article. You would know this if you actually read the article.
With 9000 hrs total time including 2000 hrs on water plus A&P/IA it seems to me that the long analysis misses the main issue. Rudder trim was full right for some unknown reason on a single engine aircraft (usually required only on twin engine aircraft when the left engine has failed). Consequently the pilot needed two feet on the left rudder pedal. I suspect that low airspeed close to stall resulted in entry to a spin. I am always amused by the assumed level of aviation knowledge from non aviating persons.
Well, I’m amused that you’re dismissive of the “level of aviation knowledge” at the Safety Investigation Authority, Finland (SIAF), who conducted the investigation, and whose conclusions Sylvia Wrigley is presenting in her article. (Sylvia is “an aviating person”, too! Her book, “You fly like a woman”, is linked in the upper right corner of the page.)
Sylvia, from the looks of it this article is in the running to become your most popular post of 2024, and well-deservedly so!
It sure is looking that way — feels a bit like lightning striking!
Peter Goldstern
Yes the full right rudder trim. I wondered about that too. The impression I had was that,
” the aircraft had a tendency to roll and had been uncomfortable to fly because of a lack of aileron trim. This might explain why the pilot had the aircraft trimmed full right rudder on take-off: to correct for this roll.”
But now the twist (?) in the right wing had been corrected, so this rudder trim wasn’t required ?
As an aside, years ago, I took off from Nairobi Wilson in a Cessna 402B twin after a service check.
As I was accelerating down the runway, there was an increasing tendency for the airplane to pull to the right. Power was good on both engines. I lifted the nosewheel off the pavement, but kept mains on the tarmac as it accelerated. Not enough runway to reject.
With extra airspeed and lots of left rudder input, lifted off. Fly the airplane first. At 1000 feet or so, I checked the rudder trim. It was dialed hard to the right !
So as part of the service check in Nairobi, I believe mechanics had checked rudder trim in both directions, but hadn’t centered it again at the end.
I was the only pilot who flew this aircraft, so I didn’t check this before starting takeoff roll. My bad?
Ouch. Very glad you made it up and safe!